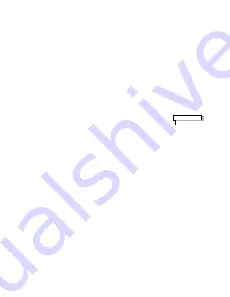
Operating the Converter
4-13
590+ Series DC Digital Converter
Performance Adjustment
Current Loop - The Autotune Feature
Now perform an Autotune to identify and store the following Current Loop parameters:
PROP. GAIN
INT. GAIN
DISCONTINUOUS
Initial Conditions
1. Main contactor open, i.e. no Start/Run signal at terminal C3.
2. Set the AUTOTUNE parameter to OFF.
3. Program Stop (terminal B8) and Coast Stop (terminal B9) should be high, i.e. 24V.
4. If the field is being supplied by a third-party controller, remove the field manually. (If the
field is internally regulated, Autotune automatically quenches the field).
Note:
The shaft may require clamping for certain motors to prevent rotation >20% during the
Autotune sequence. If using a permanent magnet motor, the shaft MUST be clamped.
Performing an Autotune
x
Set the AUTOTUNE parameter to ON.
x
Close the main contactor, i.e. Start/Run signal to terminal C3.
x
Energise the Enable terminal (C5).
The Autotune sequence is initiated. When complete (after approximately 10 seconds), the main
contactor is opened automatically signalling the end of the sequence and the AUTOTUNE
parameter is reset to OFF.
x
Perform a PARAMETER SAVE now
. Refer to Chapter 5: “The Operator Station - Saving
Your Application.
x
If necessary, restore field connections and remove the mechanical clamp.
Autotune Failed?
x
The Operator Station displays the message AUTOTUNE ABORTED
If any one of the Initial Conditions above are removed, or the Autotune sequence times out
(after 2 minutes), then the Autotune sequence is aborted causing the main contactor to drop
out.
x
The Operator Station displays the message AUTOTUNE ERROR
If during the Autotune sequence the motor speed feedback is greater than 20% of rated
speed, or the field current is detected above 6% of rated field current, then the Autotune
sequence is suspended causing the main contactor to drop out.
Note:
Refer to Chapter 9: “Control Loops” - Current Control for manual tuning instructions.
Speed Loop
You will need to adjust the Speed Loop for your particular application although in most cases
the default settings are acceptable. The optimum Speed Loop performance is achieved by
adjusting the PROP. GAIN and INT. TIME CONST. parameters.
PID is used to control the response of any closed loop system. It is used specifically in system
applications involving the control of drives to provide zero steady state error between Setpoint
and Feedback, together with good transient performance.
Proportional Gain (PROP. GAIN)
This is used to adjust the basic response of the closed loop control system. The PID error is
multiplied by the Proportional Gain to produce an output.
Integral (INT.TIME CONST.)
The Integral term is used to reduce steady state error between the setpoint and feedback values
of the PID. If the integral is set to zero, then there will always be a steady state error.
MMI Menu Map
1
CONFIGURE DRIVE
AUTOTUNE