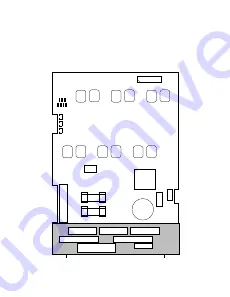
Standard and Optional Equipment
13-3
590+ Series DC Digital Converter
AH470330 (Frame 2)
(2 Quad and 4 Quad)
Power supplies for the controller are generated from the single phase auxiliary supply via a
Switched Mode Power Supply. The incoming supply is directly rectified to provide a high
voltage dc power rail. A high voltage transistor switches this rail on to the primary of a high
frequency transformer, the output of which is rectified and smoothed to provide the dc power
supply rails. The +15V dc rail is monitored via a reference element and a control signal returned
via an opto-isolator to the control element of the high voltage switching transistor. The other dc
rails (-15V & +24V dc) are generated via separate secondary windings which are rectified and
smoothed, with a separate SMPS element providing a reg5V dc rail. The SMPS operates
over a0n input voltage range of 110V to 240V ac
r
10%, 50/60Hz.
CONN 29
T5
T2
T3
T6
T1
T4
T8
T11
T12
T9
T10
T7
test points
TB 13
CONN 30 (heatsink thermistor))
CONN 47 (fan)
CONN 46 (fan)
transformer
SMPS
CONN 16
CONN 27
FS6
FS5
FS3
(to control board)
3 phase and
main contactor
coil
field fuses
aux.
fuse
transformer
option
CONN 17
CONN 44
TB5
TB6
Power Board
Terminal Board
Figure 13-4 590+ Power Board 4 Quad (AH470330)