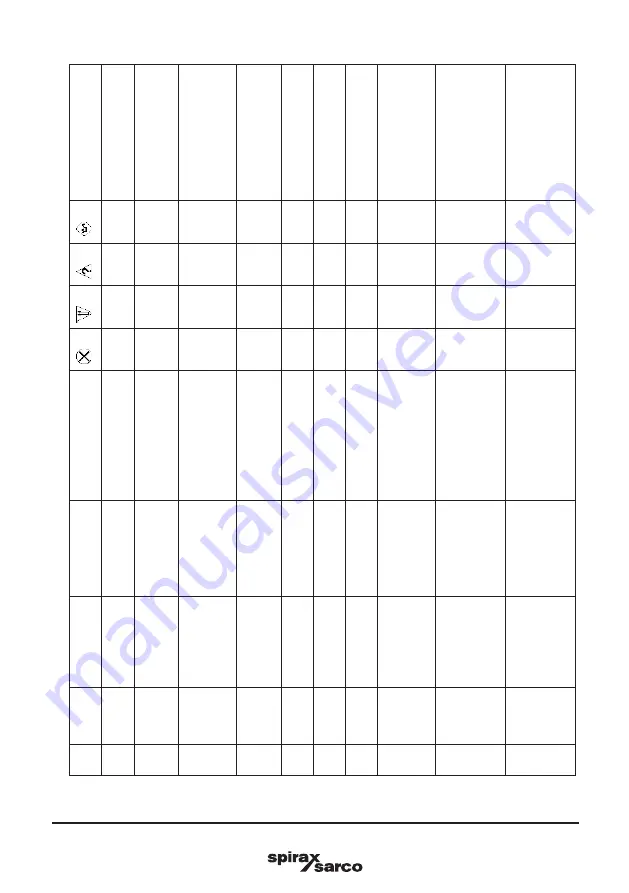
IM-P707-01
CTLS Issue 1
81
SP8-10 Smart positioner
6.
1.
2 E
rr
or m
es
sa
ge
s
(c
on
tin
ue
d)
N
o.
Pri
ori
ty
Fau
lt m
es
sa
ge
Po
ss
ibl
e c
aus
e
Tr
oub
le
sho
ot
in
g t
he
in
st
ru
m
en
t
F
C
S
M
G
rou
p
13
53
S
tr
ok
e c
ou
nt
er
lim
it e
xc
ee
de
d
M
an
y v
al
ve
st
ro
ke
s
Va
lv
e re
qu
ire
s
m
ain
te
nanc
e
X
14
54
Tr
av
el c
ou
nt
er
lim
it e
xc
ee
de
d
M
an
y v
al
ve
st
ro
kes
or
vib
ra
tin
g v
al
ve
Va
lv
e re
qu
ire
s
m
ain
te
nanc
e
X
15
55
E
le
ct
ro
nic
te
mp
er
atu
re
m
ea
su
rem
en
t
fai
lur
e
Te
mp
er
atu
re
sen
so
r d
ef
ec
tiv
e
R
epl
ac
e e
le
ct
ro
nic
s
X
E
le
ct
ro
nic
s
16
71
E
le
ct
ro
nic
te
mp
er
atu
re
o
ut
of
lim
its
Te
mp
er
atu
re
is
to
o h
ig
h o
r t
oo
low
C
he
ck
m
ou
nt
ing
con
di
tion
s
X
Spec
ia
l R
eq
ui
re
m
en
ts
17
94
C
on
fig
ura
tion
da
ta
fai
lur
e
O
ut
pu
t pi
pi
ng
m
ixe
d u
p
C
he
ck
m
ou
nt
ing
con
di
tion
s
X
Ac
tua
to
r
18
95
E
le
ct
ro
nic
s -
N
V c
hi
p d
ef
ec
t
Fa
ult
y
ele
ct
ro
nic
s
R
epl
ac
e e
le
ct
ro
nic
s
X
E
le
ct
ro
nic
s
19
96
N
on
v
ol
ati
le
da
ta
d
ef
ect
Fa
ult
y
ele
ct
ro
nic
s
R
epl
ac
e e
le
ct
ro
nic
s
X
E
le
ct
ro
nic
s
20
56
Le
ak
ag
e d
ur
in
g
ope
ra
tion
Le
ak
ag
e in
ac
tua
to
r, p
ip
in
g,
co
nn
ec
tio
ns
, o
r
po
si
tio
ne
r
S
ta
rt
le
ak
ag
e t
es
t
X
Ac
tua
to
r
21
57
Le
ak
ag
e
cham
be
r 1
Le
ak
ag
e in
ch
am
be
r 1 o
f
th
e a
ct
ua
to
r
or
p
neu
m
at
ic
s
out
put
li
ne
1
C
he
ck c
ha
m
be
r 1 o
f t
he
ac
tu
at
or
o
r p
neu
m
at
ic
s
out
put
li
ne
1
X
Ac
tua
to
r
22
58
Le
ak
ag
e
cham
be
r 2
Le
ak
ag
e in
ch
am
be
r 2 o
f
th
e a
ct
ua
to
r
or
p
neu
m
at
ic
s
out
put
li
ne
2
C
he
ck c
ha
m
be
r 2 o
f t
he
ac
tu
at
or
o
r p
neu
m
at
ic
s
out
put
li
ne
2
X
Ac
tua
to
r
Summary of Contents for SP8-10
Page 8: ...IM P707 01 CTLS Issue 1 8 SP8 10 Smart positioner Label example ...
Page 51: ...IM P707 01 CTLS Issue 1 51 SP8 10 Smart positioner Fig 28 Continued on next page ...
Page 52: ...IM P707 01 CTLS Issue 1 52 SP8 10 Smart positioner Fig 29 Continued on next page ...
Page 53: ...IM P707 01 CTLS Issue 1 53 SP8 10 Smart positioner Fig 30 ...
Page 86: ...IM P707 01 CTLS Issue 1 86 SP8 10 Smart positioner ...
Page 87: ...IM P707 01 CTLS Issue 1 87 SP8 10 Smart positioner ...
Page 88: ...IM P707 01 CTLS Issue 1 88 SP8 10 Smart positioner ...