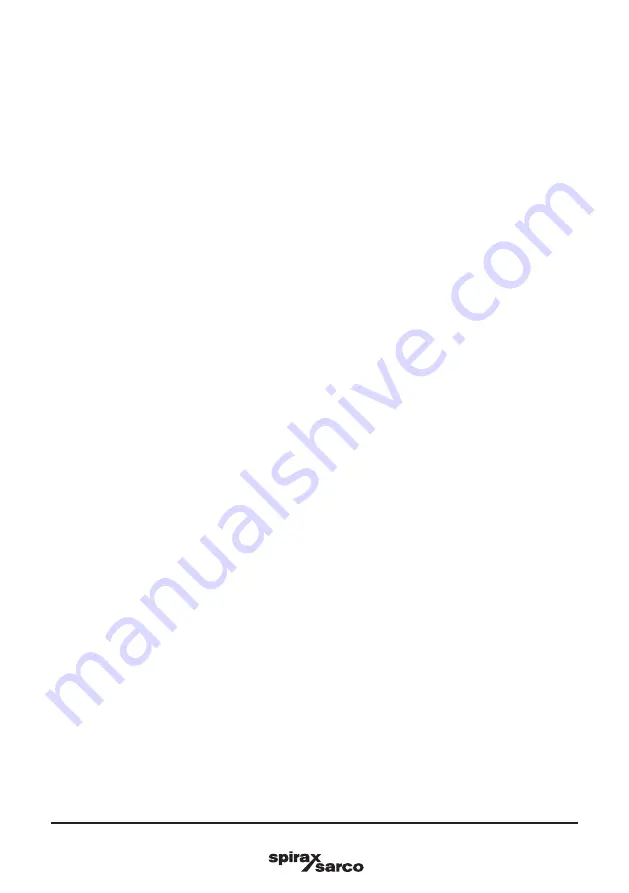
IM-P707-01
CTLS Issue 1
30
SP8-10 Smart positioner
3.3.6 Cable specification
To connect the SP8-10 Remote Sensor, a cable with the following specifications needs to be used:
-
3-wire, cross-section 0.5 to 1.0 mm²
-
Shielded, with at least 85 % coverage
-
Temperature range up to at least 100 °C (212 °F)
The cable glands used must also be approved for a temperature range up to at least 100 °C (212 °F). The
cable glands require a mounting for the shielding and strain relief for the cable in addition.
Spirax-Sarco offers suited cables and cable glands with DNV_GL certification for the SP8-10 Remote Version.
3.3.7 Electrical connection
Connect the positioner (SP8-10 Control Unit) and remote position sensor while observing the following
instructions:
-
A shielded 3-wire cable with a maximum length of 10 m (33 ft) must be used for the connection.
-
Route the cable into the terminal compartment through the EMC cable glands. Ensure that the shielding
is secured correctly in the EMC cable glands.
-
Connect the cables in accordance with the electrical connections and tighten the screws of the terminals
so that they are hand-tight.
-
The electrical connections of the SP8-10 Control Unit and the optional modules are carried out as
described in chapter Connection on the device on page 36.
-
Use wire end ferrules when connecting.
-
If the SP8-10 Control Unit is fastened so that it is it non-conductive, the housing must be grounded
(SP8-10 Control Unit and remote position sensor with the same electric potential); otherwise control
deviations could occur with regard to Analogue position feedback.
-
If the device is being operated on a cylinder, for reasons associated with linearity you should run automatic
adjustment for the rotary actuator.
-
The pneumatic outputs to the actuator must be connected using pneumatic lines with a minimum
diameter of 6 mm.
3.3.8 Installing the option modules
Installing the mechanical position feedback
1.
Loosen the screws for the housing cover and remove it.
2.
If one has been installed, remove the optical position indication and unscrew the shaft extension.
3.
Move the printed circuit board for position feedback to the right underneath the two plastic clips and
secure it using the screw provided.
4.
If applicable, install the optical position indication.
5.
Attach the housing cover and screw it on to the housing. Tighten the screws so that they are hand-tight.
Summary of Contents for SP8-10
Page 8: ...IM P707 01 CTLS Issue 1 8 SP8 10 Smart positioner Label example ...
Page 51: ...IM P707 01 CTLS Issue 1 51 SP8 10 Smart positioner Fig 28 Continued on next page ...
Page 52: ...IM P707 01 CTLS Issue 1 52 SP8 10 Smart positioner Fig 29 Continued on next page ...
Page 53: ...IM P707 01 CTLS Issue 1 53 SP8 10 Smart positioner Fig 30 ...
Page 86: ...IM P707 01 CTLS Issue 1 86 SP8 10 Smart positioner ...
Page 87: ...IM P707 01 CTLS Issue 1 87 SP8 10 Smart positioner ...
Page 88: ...IM P707 01 CTLS Issue 1 88 SP8 10 Smart positioner ...