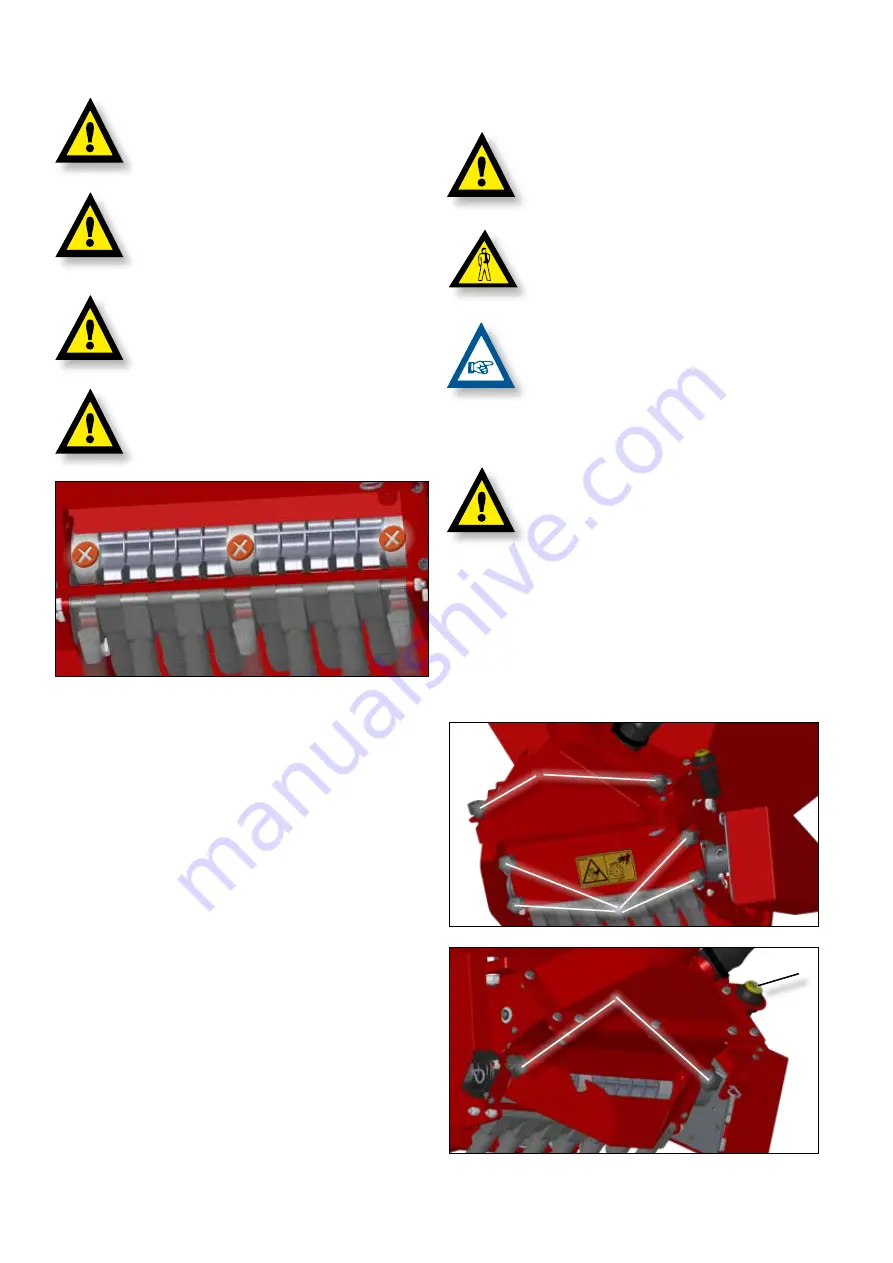
- 70 -
IMPORTANT
: PUT THE CAPS ON THE EXITS THAT
ARE NOT USED (example: *1, *7 and *13, Fig. 8.34).
IMPORTANT
: PUT BLOCKING SECTORS IN THE
EXITS THAT ARE NOT USED. MACHINE COULD
BE DAMAGED IF THIS IS NOT DONE (example
of machine with 10 working parts, Fig. 8.34).
THE EXITS THAT ARE NOT USED MUST LINE UP WITH
THE BLICKING SECTORS AND CAPS.
IMPORTANT
: THE ROLLER MUST BE CHANGED
ONLY WHEN THE HOPPER IS EMPTY.
Fig. 8.34
Fig. 8.34
*1
*1
55
99
22 33 44
66 *7
*7 88
10
10 11
11 12
12 *13
*13
8.2.2 CALIBRATION TEST
A PRIOR CALIBRATION TEST MUST BE CARRIED OUT
BEFORE BEGINNING WORK AS WELL AS FREQUENT
CHECKS.
CARRY OUT THE CALIBRATION TEST WITH THE FAN
TURNED OFF COMPLTELY.
IMPORANT:
CHOOSE THE MOST APPROPRIATE
ROLLER SETTING FOR THE JOB, TO DO THIS, THE
FOLLOWING MUST BE TAKEN INTO ACCOUNT:
DISTANCE BETWEEN ROWS, OPERATING
SPEED AND THE DOSAGE OR RATE IN KG/HA
DESIRED (SEE SECTION 8.2 CENTRALISED
MICROGRANULAR OR INSECTICIDE.
IN THE EVENT THAT THE ROLLER MUST
BE CHANGED, SEE SECTION 8.2.1 CHANGING
THE ROLLER.
For product calibration, follow these steps:
1-
Fill
the hopper with the product. To do this the cap must
be turned to extract it and then fill it and close the cap.
2-
Remove the CALIBRATOR GATE, to do this the two knobs must
be removed (C, Fig. 8.35).
3-
Remove the CALIBRATOR CONE knobs (D, Fig. 8.35) and put the
cone in position for calibration, fixing the cone with the knobs
(E, Fig. 8.36).
Fig. 8.35
Fig. 8.35
C
C
DD
Fig. 8.36
Fig. 8.36
E
E
FF