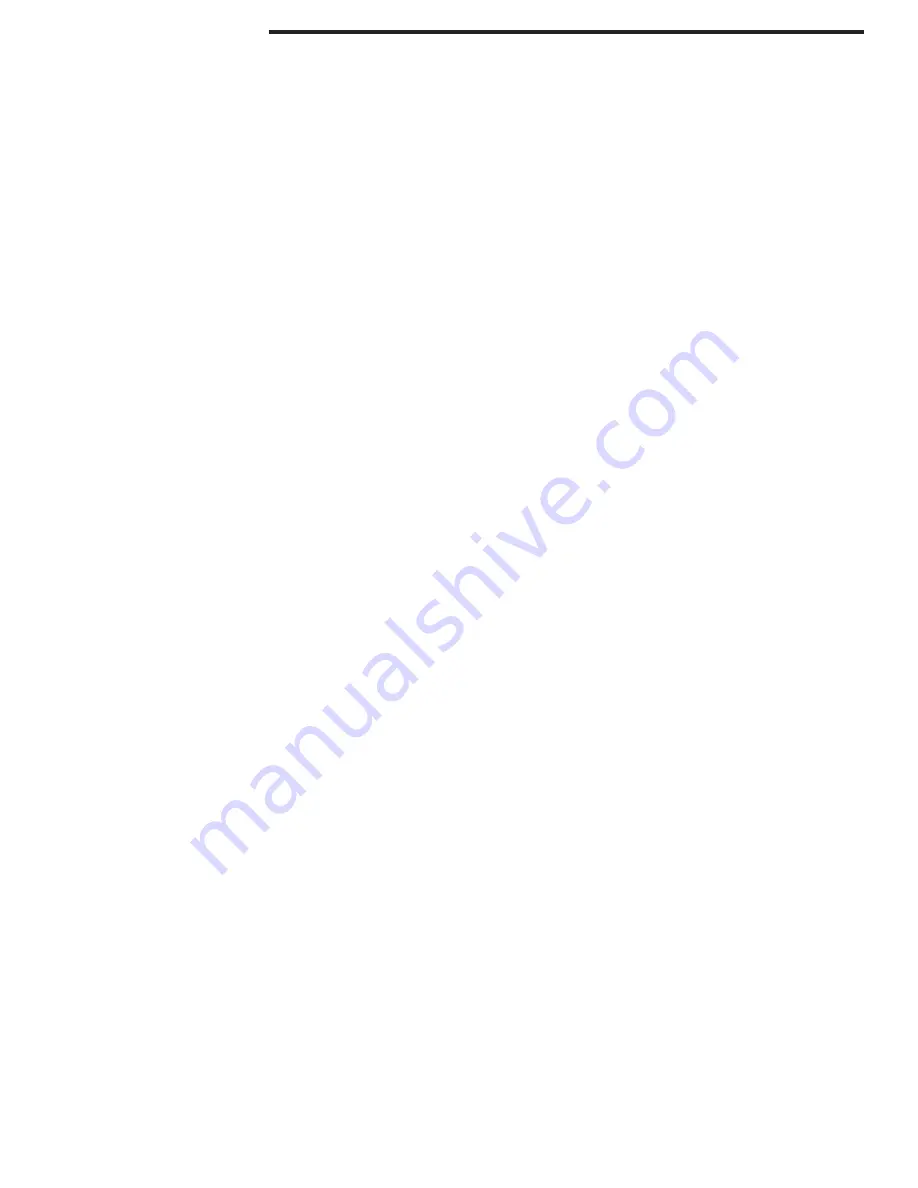
Parts Replacement
84
40-5648-51B
Clutch assembly
Tools needed
For this disassembly procedure you will need:
• Torque screwdriver with a Phillips head & ¼”
nut drive
• ¼” wrench
• .002” (.051mm) shim
Always work at an electrostatic-controlled work sta-
tion
when disassembling the pump.
Leadscrew
Removal
1. Open pump housing per pump housing section
above, and setup the case top section with the
handle down and main board facing up.
2. Remove the main board per section above.
3. Squeeze the plunger lever and fully extend the
plunger head away from the case.
4. Remove pan head screws and standoffs holding
the extrusion (drive train assembly). Remove pan
head screws and Nylock nuts holding barrel clamp
assembly to extrusion.
5. Partially slide extrusion out of case until Nylock
nut holding leadscrew on right end plate is acces-
sible.
6. Pull the plastic worm gear off the end of leadscrew
near motor.
7. Remove three flat head screws holding motor as
-
sembly on extrusion, and pull off motor assembly.
8. Slide carriage rod out of the carriage.
9. Move the plunger head/carriage in about 1”
(2.5cm) from the right end plate. Hold onto the
“D” side of the leadscrew and use ¼” wrench to
remove Nylock nut holding leadscrew and the flat
brass washer.
10. Slide extrusion in slightly until leadscrew clears
right end plate, then pull off the thrust bearings.
11. Squeeze the plunger lever to open clutch and pull
leadscrew out of carriage.
Replacement
1. Apply light coating of STP poly-plus (lithium)
grease to leadscrew. Squeeze plunger lever to open
clutch and insert leadscrew until it sticks slightly
through the carriage.
2. Install thrust bearing assembly (flat washer, bear
-
ings, flat washer) onto end of leadscrew and pull
on plunger head to feed leadscrew through the
right end plate. Ensure nylon shoulder washer is
still in place on right end plate.
3. Place brass washer over the leadscrew and start
Nylock nut. Insert .002” shim between the brass
washer and shoulder washer and tighten the nut.
Do not over-tighten nut. Remove shim and check
if brass washer can move (spin) freely, if not
loosen nut slightly.
4. Slide carriage rod through carriage and seat into
hole in right end plate.
5. Slide motor assembly over leadscrew and align
carriage rod with motor assembly bracket. Secure
motor assembly on extrusion with three flat head
screws. Torque to 100 in oz (1.2 Nm).
6. Align “D” of worm gear with leadscrew shaft and
press onto leadscrew until gear is centered over the
motor worm.
7. Carefully slide the extrusion (drive train assembly)
back into case.
8. Ensure right end plate on extrusion does not dam
-
age ear clip sensor.
9. Ensure plunger cable comes out between middle
boss and boss by the motor.
10. Slide keypad ground tab (black side toward extru
-
sion) between boss by the motor and extrusion.
11. Secure extrusion with 3 standoffs and 3 pan head
screws. Torque to 100 in oz (1.2 Nm).
12. Secure the
barrel clamp assembly to the extrusion
with 2 pan head screws and Nylock nuts. Torque
to 100 in oz (1.2 Nm).
13. Reinstall main board per main board section
above.
14. Close pump housing per housing section above.
Clutch or clutch cam
Tools needed
For this disassembly procedure you will need:
• Safety glasses
Summary of Contents for Medfusion 3000 Series
Page 1: ...s Medfusion 3000 Series Technical Service Manual ...
Page 2: ...Table of Contents ii 40 5648 51B ...
Page 20: ...Introduction 14 40 5648 51B ...
Page 32: ...Scheduled Maintenance 26 40 5648 51B ...
Page 80: ...Troubleshooting 74 40 5648 51B ...
Page 116: ...Calibration Adjustment 110 40 5648 51B ...
Page 160: ...Assembly Drawings Parts Lists 154 40 5648 51B Case bottom assembly Medfusion 3500BC ...
Page 162: ...Assembly Drawings Parts Lists 156 40 5648 51B Case top assembly w plunger ...
Page 164: ...Assembly Drawings Parts Lists 158 40 5648 51B Case top assembly without plunger ...
Page 172: ...Assembly Drawings Parts Lists 166 40 5648 51B Accessories parts list Poleclamp assembly ...
Page 182: ...Index 176 40 5648 51B ...
Page 183: ......