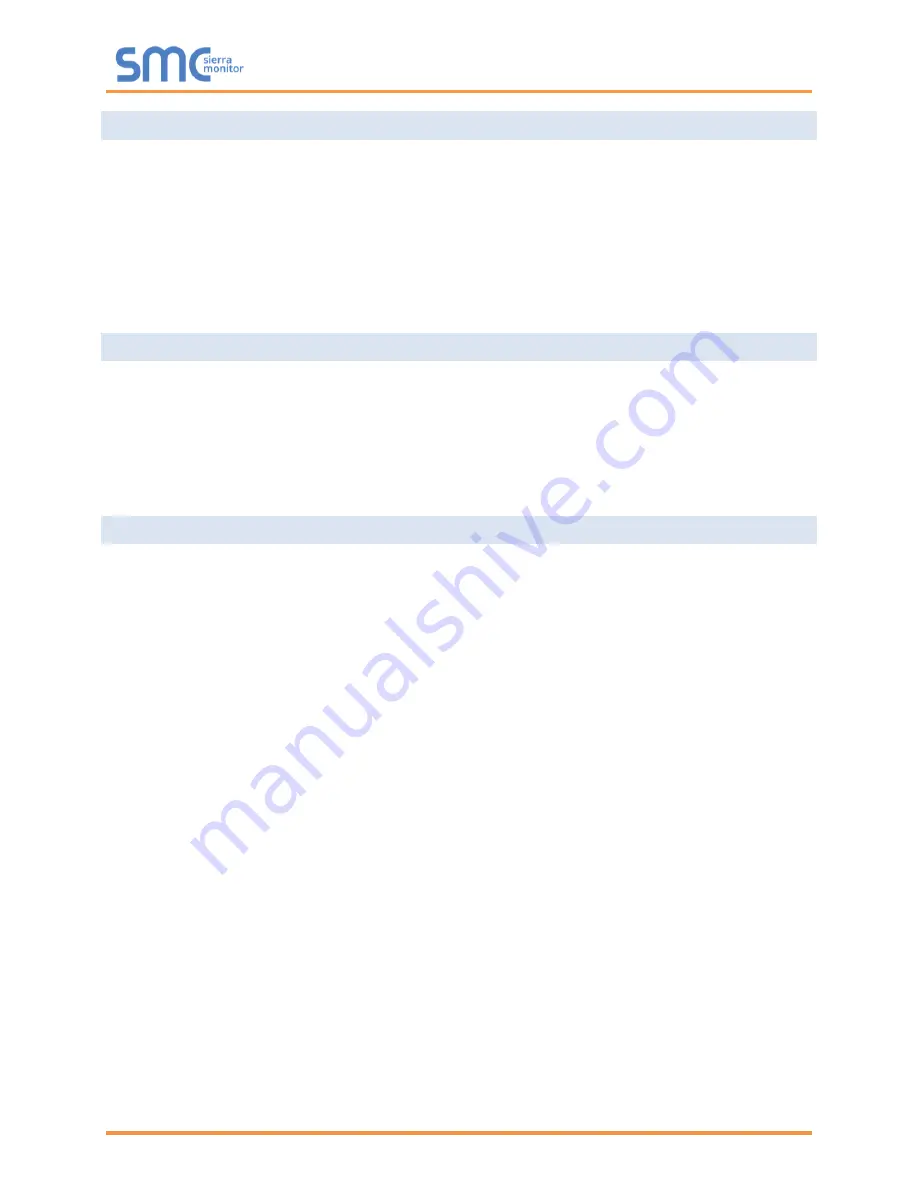
Sentry 5000-32-IT Controller
Page 7 of 82
1.4
Programmable Features
Controllers are supplied with the following programmable features:
•
Auto Discovery of connected sensor modules
•
User configurable module tags, alarm levels and calibration settings
•
Commander Logic used to enable control algorithms combining input values and states and
managing relay output states
•
Modbus RTU output for interface
•
Sentry InSite Webserver
1.5
Gas Detection System
The Controller is always used in conjunction with gas detection sensor modules and is generally
connected to alarm annunciation devices and environment control devices such as exhaust fans. The
Controller may also be connected to facility control systems or control rooms. These external connections
are not covered by this manual except as necessary to define the Controller connection or functionality.
In large facilities it is possible that gas detection systems include multiple Controllers that may not be
identical to each other. For purposes of this manual each Controller should be considered unique.
1.6
Power Requirements
The Controller requires 24 VDC at 12 Amps for a fully loaded (maximum 32 modules connected) gas
detection system. The following considerations should be noted:
•
The Controller has an integral AC/DC power supply that allows primary 120/240 VAC power
•
The Controller allows direct 24 VDC connection from a plant supply or battery backed UPS
•
The VDC source will provide power for the connected sensor modules
•
Power for ancillary connected devices such as alarm indicators must be supplied separately
Summary of Contents for Sentry 5000-32-IT
Page 28: ...Sentry 5000 32 IT Controller Page 28 of 82 Figure 15 Analog Input Wiring ...
Page 29: ...Sentry 5000 32 IT Controller Page 29 of 82 Figure 16 PSG Sentry Classic Wiring ...
Page 30: ...Sentry 5000 32 IT Controller Page 30 of 82 Figure 17 Modbus Wiring ...
Page 31: ...Sentry 5000 32 IT Controller Page 31 of 82 Figure 18 Top Board Relay Digital Output Wiring ...
Page 32: ...Sentry 5000 32 IT Controller Page 32 of 82 Figure 19 Analog Output Wiring ...
Page 33: ...Sentry 5000 32 IT Controller Page 33 of 82 Figure 20 Digital Input Wiring ...
Page 34: ...Sentry 5000 32 IT Controller Page 34 of 82 Figure 21 Bottom Board Relay Wiring ...