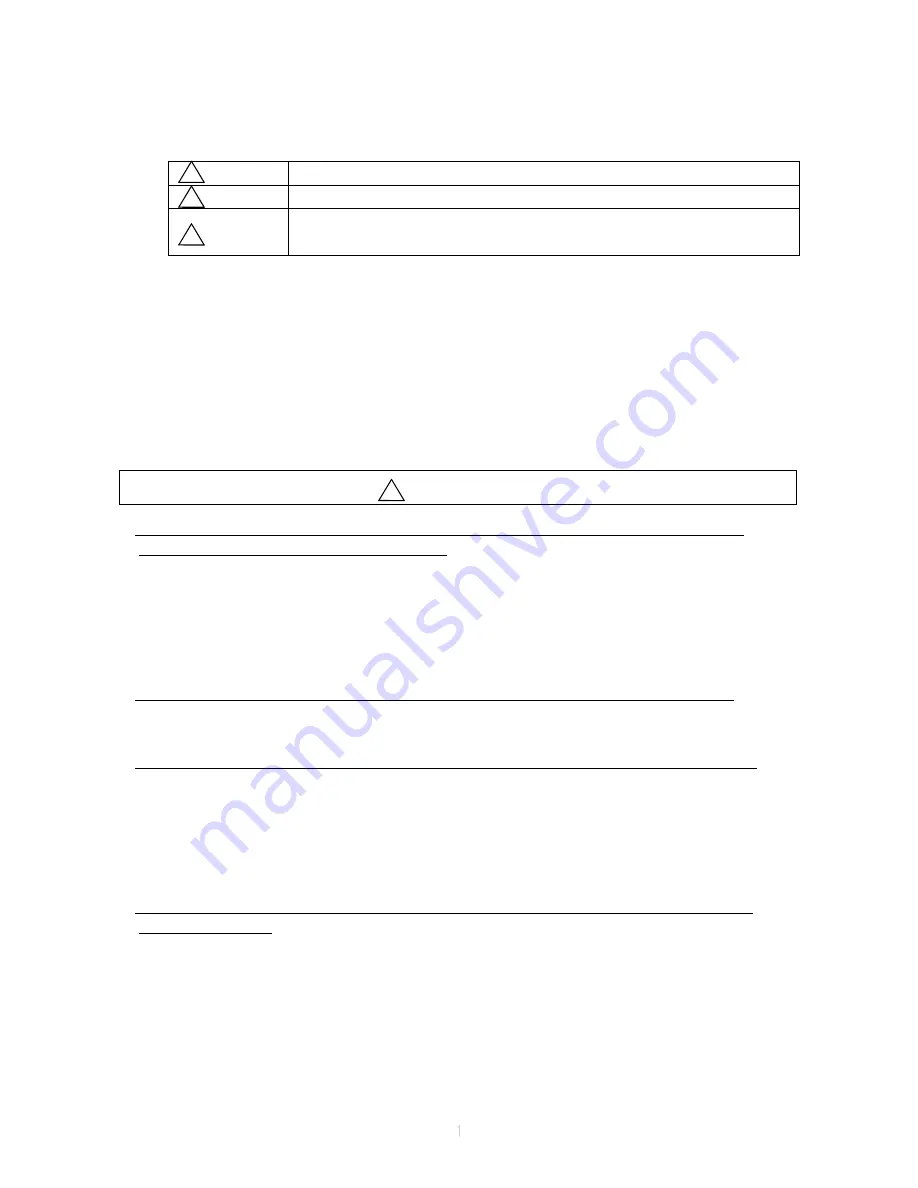
Read before Use
These safety instructions are intended to prevent a hazardous situation and/or equipment damage.
These instructions indicate the level of potential hazard by label of
“Caution”, ”Warning”, or ”Danger”.
To ensure safety, follow the instructions below as well as ISO/IEC, JIS
*1)
and other safety laws
*2)
.
Caution
Operator error could result in injury or equipment damage.
Warning
Operator error could result in serious injury or loss of life.
Danger
In extreme conditions, there is a possible result of serious injury or
loss of life.
*
1) ISO 4414: Pneumatic fluid power - General rules relating to systems
ISO 10218-1: 2006:
Robots for industrial environments - Safety requirements - Part 1: Robot
IEC 60204-1:
Safety of machinery - Electrical equipment of machines - Part 1:General
requirements
JIS B 8370: General Rules for Pneumatic systems
JIS B 9960-1: Safety of machinery - Electrical equipment of machines - Part 1: General
requirements
JIS B 8433-1:2007: Robots for industrial environments - Safety requirements - Part 1: Robot
*
2) Labor Safety and Sanitation Law etc.
Warning
1. The compatibility of pneumatic equipment is the responsibility of the person who designs the
pneumatic system or decides its specifications.
Since the products specified here are used in various operating conditions, their compatibility for
the specific pneumatic system must be based on specifications or after analysis and/or tests to
meet your specific requirements. Ensuring the initial performance and safety are the responsibility
of the person who decides the compatibility of the pneumatic system. Pneumatic systems should
be constructed after full review of the details of the products other than specifications and
possibilities of failures by checking the latest product information.
2. Only trained personnel should operate poneumaticallly operated machinery and equipment.
Assembly, handling, or repair of pneumatic systems should be performed by trained and
experienced operators.
3. Do not service machinery/equipment or attempt to remove component until safety is confirmed.
a. Inspection and maintenance of machinery/equipment should only be performed after
confirmation of safe locked-out control positions.
b. When equipment is to be removed, confirm the safety process as mentioned above. Cut the
supply pressure for this equipment and exhaust all residual compressed air in the system.
c. Before machinery/equipment is re-started, take measure to prevent shooting-out of cylinder
piston rod etc.
4. Contact SMC and take necessary safety measures if the products are to be used in any of the
following conditions:
a. Conditions and environments beyond the given specifications, or if products are used outdoors.
b. Installation on equipment in conjunction with atomic energy, railway, air navigation, vehicles,
medical equipment, food and beverages, recreation equipment, emergency stop circuits, press
applications, or safety equipment.
c. An application which has the possibility of having negative effects on people, property, or animals,
requiring special safety analysis.
d. When used in an interlock circuit, dual interlock such as mechanical protection is necessary in
case of accident. Periodical inspection is also necessary to confirm proper operation.
!
!
!
!
Summary of Contents for CE2
Page 14: ...2 2 System Configuration...
Page 20: ...5 External Dimension Drawing 5 1 Monosashi kun with Brake...
Page 21: ......
Page 22: ...5 2 Controller...
Page 23: ...5 3 Extension Cable...
Page 27: ...7 3 Input Signal Wiring 7 3 1 Input Signal Wiring Diagram...