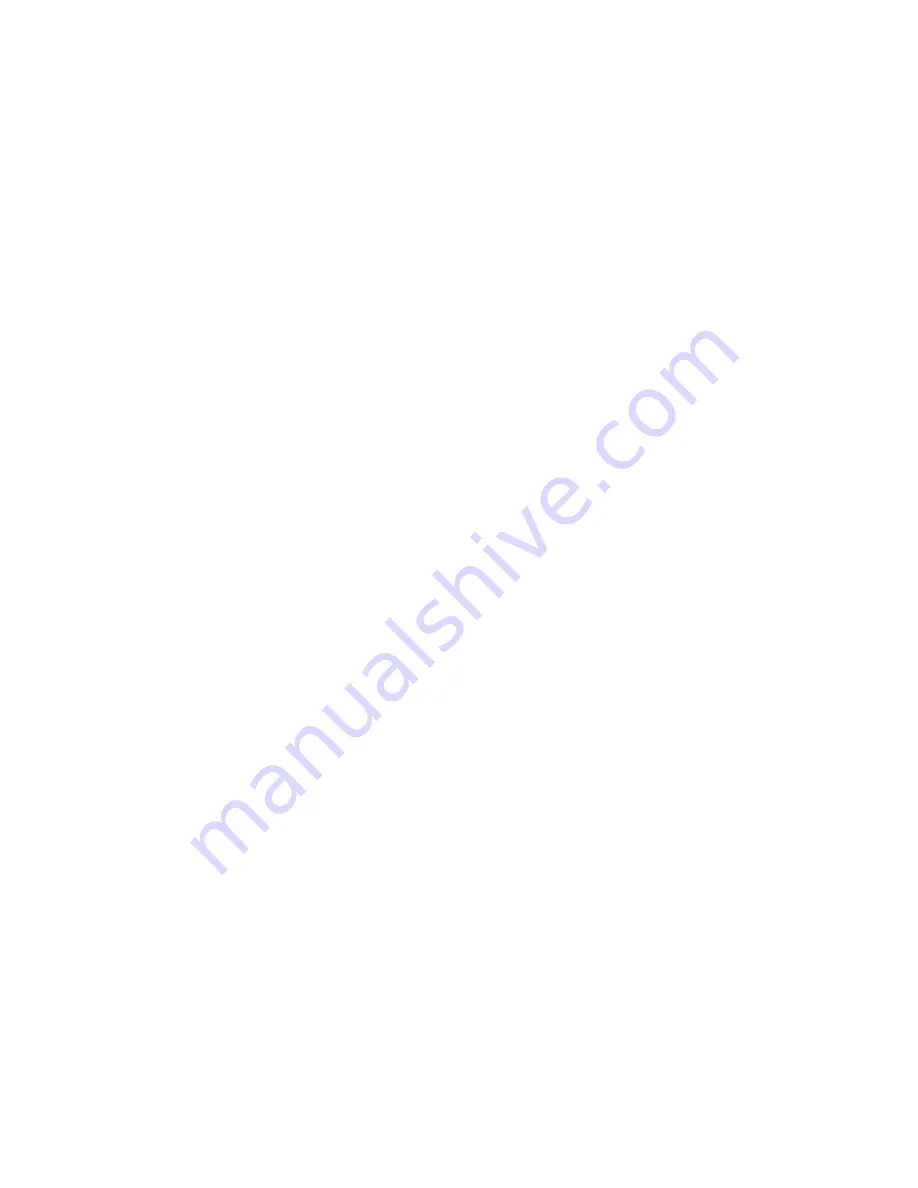
8
3. Error Detector
When System is found faulty, error detector will take action, detect and analyze error. Finally, error
messages will be displayed. Thus, ease of debugging time.
4. DIN Rail installation is possible.
1-2 Position Control
1. With controller, valve outputs to achieve precise positioning.
2. For the situation whereby cylinder stopping position does not fall into the tolerance range, retries will
be performed. First, it will retract (30mm), and then extend to achieve setting position.
3. With learning ability, brake point will be recognized and thus lead to precise positioning with taking
into the consideration of factors like loading & pressure condition, momentum & impact when
stopping.
4. Stopping method applied is through air balance and brake to lock the movement. While brake applies
the combination of spring and pneumatic locking method.
5. Position is determined when positioning falls on the setting tolerance range.
6. Position determination will follow the sequence of selected program
’s steps.
7. Only programs are available for selection. Program steps are not selectable.
1-3 Positioning at Cylinder Rod End
Do not use cylinder with cushion, if determined position falls at cylinder rod
’s end (front or back). This is
due to drastical change of speed occurring at the stroke end will lead to imprecision and easy occuring
of learning error (Err 6).
2. System Configuration
2-1 System Checking Flow Chart
《
CE2 (Monosashi - kun with brake) + CEU2 (Controller)
》
Refer to check Flow, showing at next page, to determine brake position, so as to reduce the
possibility of occurring errors, which are mostly due to the stopping precision, caused by brake
position.
Summary of Contents for CE2
Page 14: ...2 2 System Configuration...
Page 20: ...5 External Dimension Drawing 5 1 Monosashi kun with Brake...
Page 21: ......
Page 22: ...5 2 Controller...
Page 23: ...5 3 Extension Cable...
Page 27: ...7 3 Input Signal Wiring 7 3 1 Input Signal Wiring Diagram...