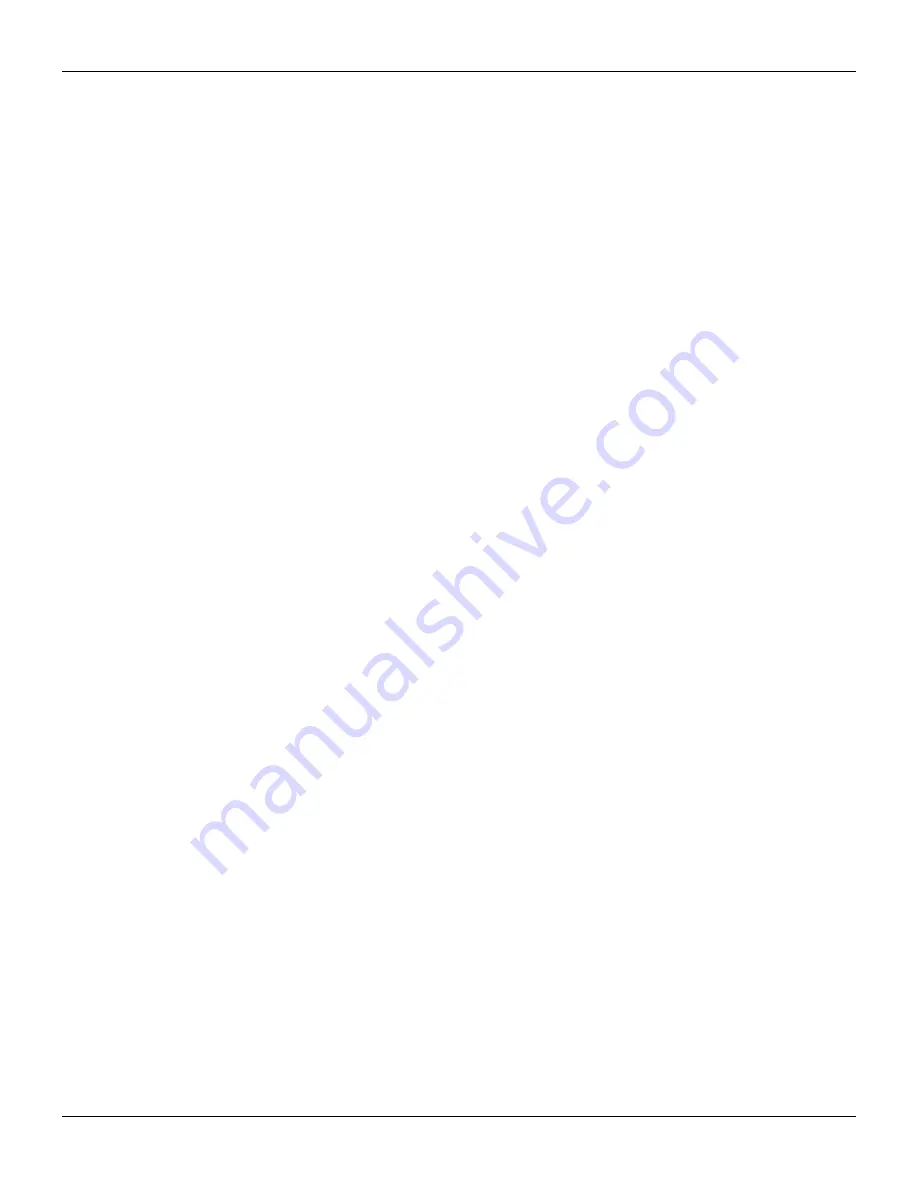
FY303 – Operation, Maintenance and Instructions Manual
3.12
FY303 Cyclical Configuration
Through the GSD file the master executes all initialization process with the device and this file
presents details of hardware revision and software, bus timing of the device and information on
cyclical data exchange.
FY303
has one AO function block. It is with this block that the class 1 master will execute the
cyclical services and the user should choose the configuration, according to the application.
If the AO block is in AUTO, then the device will receive the value and status of the setpoint of the
class 1 master and the user will also be able to write in this value via class 2 master.
In this case, the setpoint status should always be equal to 0x80 (“good") and the following
configurations can be chosen:
§
SP
§
SP/CKECKBACK
§
SP/READBACK/POSD
§
SP/READBACK/POSD/CKECKBACK
If the AO block is in RCAS, then the device will receive the value and status of the setpoint only via
class 1 master. In this case, the setpoint status should always be equal to 0xc4 (“IA"). The following
configurations can be chosen:
§
SP
§
SP/CKECKBACK
§
SP/READBACK/POSD
§
SP/READBACK/POSD/ CKECKBACK
§
RCASIN/RCASOUT
§
RCASIN/RCASOUT/ CKECKBACK
§
SP/READBACK/RCASIN/RCASOUT/POSD/CHECKBACK
See below a typical example with the necessary steps to the integration of a
FY303
device in a PA
system:
- Copy the GSD file of the
FY303
for the search directory of the PROFIBUS configurator, usually
named GSD.
- Copy the bitmap file of the
FY303
for the search directory of the PROFIBUS configurator, usually
named BMP.
- Once the master is chosen, the communication rate must be chosen, remembering that when we
had the couplers, we can have the following rates: 45.45 kbits/s (Siemens), 93.75 kbits/s (P+F) and
12 Mbits/s (P+F, SK2) .If we had the link device, it can be up to 12 Mbits/s.
- Add the
FY303
, specifying the address in the bus.
- Choose the cyclical configuration via parameterization with the GSD file, dependent of the
application, as indicated previously. Remember that this choice must be in agreement with the
operation mode of the AO block. In these conditions attempt to the status of the setpoint value that
should be 0x80 (“good”), when in AUTO mode and 0xc4 (IA) for RCAS mode.
- The watchdog condition can also be activate, where after the communication loss detection for the
slave device with the master, the equipment can change to a fail safe condition. As
FY303
will be as
final element is recommended the configuration of a fail safe value.
Summary of Contents for fy303
Page 1: ...OPERATION MAINTENANCE AND INSTRUCTION MANUAL Profibus PA Valve Positioner JUL 16 F Y 3 0 3 M E...
Page 7: ...Kpuvcnncvkqp Hnqyejctv XKK Kpuvcnncvkqp Hnqyejctv...
Page 8: ...H 525 Qrgtcvkqp Ockpvgpcpeg cpf Kpuvtwevkqpu Ocpwcn XKKK...
Page 20: ...FY303 Operation Maintenance and Instructions Manual 1 12...
Page 26: ...FY303 Operation Maintenance and Instructions Manual 2 6...
Page 69: ...Configuration 3 43 Figure 10 Sensor Pressure Configuration Data...
Page 70: ...FY303 Operation Maintenance and Instructions Manual 3 44...
Page 88: ...FY303 Operation Maintenance and Instructions Manual 5 6...
Page 94: ...H 525 Qrgtcvkqp Ockpvgpcpeg cpf Kpuvtwevkqpu Ocpwcn C08...
Page 95: ...Egtvkhkecvkqpu Kphqtocvkqp C09 Eqpvtqn Ftcykpi FM Approvals Factory Mutual...
Page 96: ...H 525 Qrgtcvkqp Ockpvgpcpeg cpf Kpuvtwevkqpu Ocpwcn C0 CSA Canadian Standards Association...
Page 97: ...Egtvkhkecvkqpu Kphqtocvkqp C0...
Page 98: ...H 525 Qrgtcvkqp Ockpvgpcpeg cpf Kpuvtwevkqpu Ocpwcn C032...
Page 114: ...6 Mounting Instructions...