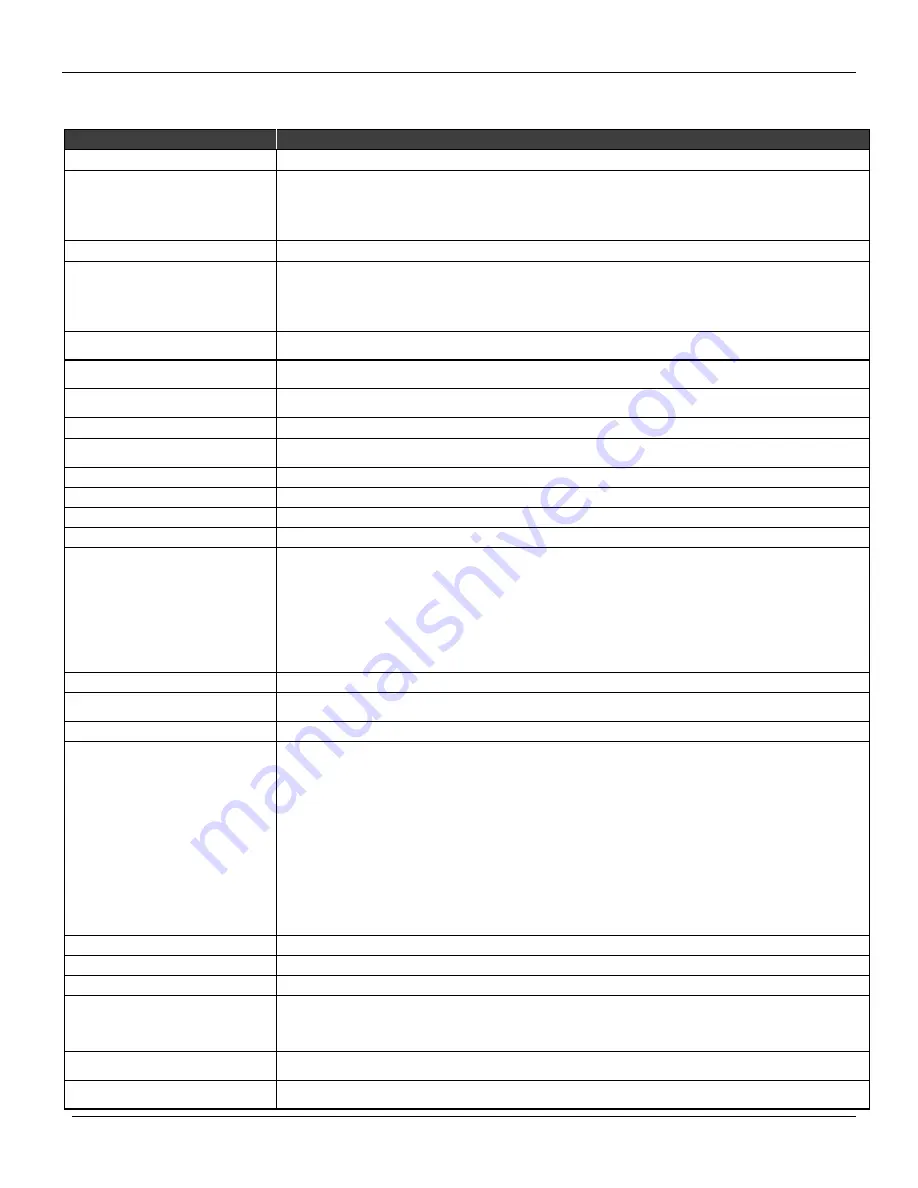
Configuration
3.3
Transducer Block Standard Parameter Descriptions
Parameter
Transducer Block Description
ACTUATOR_ SER_NUM
Serial-number of the actuator belonging to the positioner or the electronic device.
ACTUATOR_ACTION
Fail-Safe position for power-loss of the actuator, the valve:
0
= not initialized
1
= opening (100%)
2
= closing (0%)
3
= none / remains in actual position
ACTUATOR_MAN
Name of Actuator-Manufacturer.
ACTUATOR_TYPE
Type of actuator:
0
= electro-pneumatic
1
= electric
2
= electro-hydraulic
3
= others
ACT_STROKE_TIME_DEC
Minimum of time to move from OPEN to CLOSE position (in sec.) for total system (positioner, actuator and
valve). Measured while commissioning.
ACT_STROKE_TIME_INC
Minimum of time to move from CLOSE to OPEN position (in sec.) for total system (positioner, actuator and
valve). Measured while commissioning.
ADD_GEAR_ID
Manufacturer specific type identification of the additional component (e.g. a gearbox, booster) mounted
between the actuator and valve.
ADD_GEAR_INST_DATE
Installation date of the additional component (e.g. gearbox, booster) mounted between the actuator and valve
ADD_GEAR_MAN
Manufacturer name of the additional component (e.g. gearbox, booster) mounted between the actuator and
valve.
ADD_GEAR_SER_NUM
Serial number of the additional component (e.g. gearbox, booster) mounted between the actuator and valve.
DEADBAND
Dead band in percent of travel span. Travel span correspondents to OUT_SCALE.
DEVICE_CALIB_DATE
Date of last calibration of the device.
DEVICE_CONFIG_DATE
Date of last configuration of the device.
LIN_TYPE
Type of linearization.
0 = no linearization (mandatory)
1 = linearization table (optional)
240 Manufacturer specific
249 Manufacturer specific
250 Not used
251 None
252 Unknown
253 Special
FEEDBACK_VALUE
The actual position of the final control element in units of OUT_SCALE.
POSITIONING_VALUE
The actual command variable for the final control element in units of OUT_SCALE. Status BAD will drive the
actuator to the fail-safe position defined by ACTUATOR_ACTION.
RATED_TRAVEL
Nominal stroke of the valve in units of OUT_SCALE.
SELF_CALIB_CMD
Initiation of a device-specific (manufacturer specific) calibration-procedure.
0 = default value; no reaction of the field device (mandatory)
1 = start zero point adjustment (optional)
2 = start self calibration / initialization (optional)
7 = reset total valve travel limit exceeded“ CB_TOT_VALVE_TRAV (optional)
and reset Accumulated valve travel“ TOTAL_VALVE_TRAVEL (optional)
10 = reset internal control loop disturbed“ CB_CONTR_ERR (optional)
255 = abort current calibration-procedure (optional)
Smar:
0 = default value; no reaction of the field device
2 = start self calibration / initialization
7 = reset total valve travel
255 = abort current calibration-procedure
SERVO_GAIN_1
Proportional-action coefficient for both moving directions.
SERVO_RATE_1
Derivative-action coefficient for both moving directions.
SERVO_RESET_1
Integral-action coefficient for both moving directions.
SETP_CUTOFF_DEC
When the servo setpoint goes below the defined percent of span, the position goes to the limit position
CLOSE.
With electro-pneumatic actuator, this is done by totally ventilate/filling of the actuator (ref. to fail-safe position.)
With electric actuator, the actuator goes motor-driven to the limit position CLOSE.
SETP_CUTOFF_INC
When the servo setpoint goes above the defined percent of span, the position goes to the limit position OPEN.
With electro-pneumatic actuator, this is done by totally ventilate/filling of the actuator (ref. to fail-safe position.)
TAB_ENTRY
The index parameter identifies which element of the table is in the X_VALUE and Y_VALUE parameter
currently
Summary of Contents for fy303
Page 1: ...OPERATION MAINTENANCE AND INSTRUCTION MANUAL Profibus PA Valve Positioner JUL 16 F Y 3 0 3 M E...
Page 7: ...Kpuvcnncvkqp Hnqyejctv XKK Kpuvcnncvkqp Hnqyejctv...
Page 8: ...H 525 Qrgtcvkqp Ockpvgpcpeg cpf Kpuvtwevkqpu Ocpwcn XKKK...
Page 20: ...FY303 Operation Maintenance and Instructions Manual 1 12...
Page 26: ...FY303 Operation Maintenance and Instructions Manual 2 6...
Page 69: ...Configuration 3 43 Figure 10 Sensor Pressure Configuration Data...
Page 70: ...FY303 Operation Maintenance and Instructions Manual 3 44...
Page 88: ...FY303 Operation Maintenance and Instructions Manual 5 6...
Page 94: ...H 525 Qrgtcvkqp Ockpvgpcpeg cpf Kpuvtwevkqpu Ocpwcn C08...
Page 95: ...Egtvkhkecvkqpu Kphqtocvkqp C09 Eqpvtqn Ftcykpi FM Approvals Factory Mutual...
Page 96: ...H 525 Qrgtcvkqp Ockpvgpcpeg cpf Kpuvtwevkqpu Ocpwcn C0 CSA Canadian Standards Association...
Page 97: ...Egtvkhkecvkqpu Kphqtocvkqp C0...
Page 98: ...H 525 Qrgtcvkqp Ockpvgpcpeg cpf Kpuvtwevkqpu Ocpwcn C032...
Page 114: ...6 Mounting Instructions...