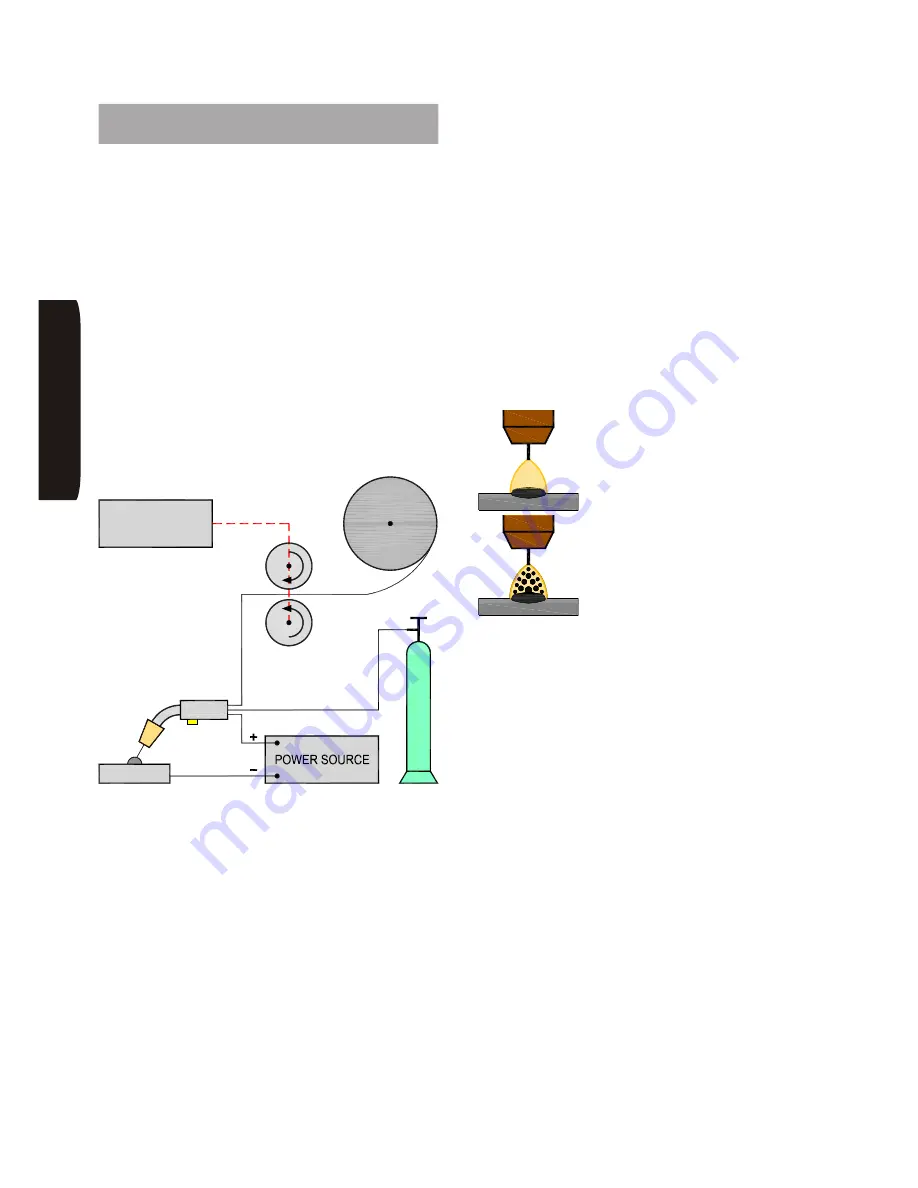
Page 30
INE S.p.A.
Via Facca, 10 - 35013 Cittadella - PADOVA - ITALIA Tel. 049/9481111 - Fax 049/9400249 - [email protected] - www.ine.it
11 MIG/MAG welding: procedures and
technical data
MIG/MAG welding is a method used to weld carbon and
low-alloy steels in an inert environment (CO
2
or
Argon/CO
2
) with the help of a solid or cored steel wire.
To weld stainless steel, the wire should match the
characteristics of the material being welded, and the
gas should be a mixture of Argon/CO
2
/O
2
.
To weld aluminium, the wire should be a type
compatible with the material and the gas should be pure
Argon; moreover, the use of a Teflon torch liner is
suggested.
A MIG/MAG welding machine is essentially made up
by:
•
a dc power source (welding machine)
•
a wire feeder
•
a torch and a cable
•
a gas cylinder with a flow meter and regulator
When welding, the torch is manoeuvred by the operator
along the joint while the wire is fed into the weld pool by
the wire feeder and forms the weld bead.
It is suggested that instruction should be sought as to
how the machine operates in the case of first use. As a
matter of fact, a basic knowledge of the welding
procedure is necessary to be able to adjust welding
parameters and to avoid spattering.
The adjustment of welding parameters consists in
finding out the correct balance between voltage and
wire speed to achieve a good-looking weld bead.
In order to avoid spattering, the correct torch position
from the workpiece should be maintained. In this
regard, special attention should be paid to a
phenomenon that generally takes places as an arc
deviation due to the electromagnetic forces at issue: the
magnetic blow. Such phenomenon mainly occurs when
welding angles or the inner corners of box-type pieces.
In order to reduce it, it is suggested to maintain the torch
in the opposite direction to the arc deviation, and to
choose an adequate point where the work return lead
should be connected.
Special attention is also to be paid to the welding of thin
materials or in the first pass of bevelled joints, as the
material might be pierced. In such cases welding with
low current values is suggested (short arc).
Two weld metal transfer methods are available in
MIG/MAG welding:
SHORT ARC
SPRAY ARC
SHORT ARC is used with arc voltage values lower than
24V and relatively low welding current values (lower
than 200 A/mm
2
). With this method the wire melts as it
is short-circuited by its own contact with the weld pool,
which causes the transfer of the molten drops. The arc
length is short, so the contact tip should protrude by 2-3
mm from the nozzle.
This method can be used in all positions (butt, fillet and
vertical welding) and generally in those cases such as
thin materials, first passes, etc., where low current
values are requested to prevent deformation and
piercing.
SPRAY ARC is on the contrary a welding method which
requires higher voltage and current values and in which
the weld metal when melting is sprayed into the weld
pool. The arc length is more evident and its intensity is
greater. The contact tip should be set back from the
nozzle (between 5 and 10 mm, as the welding current is
increased).
H
SI
L
G
N
E
WIRE SPOOL
PIECE
WIRE FEEDER
G
A
S
Summary of Contents for KMP3200
Page 63: ......