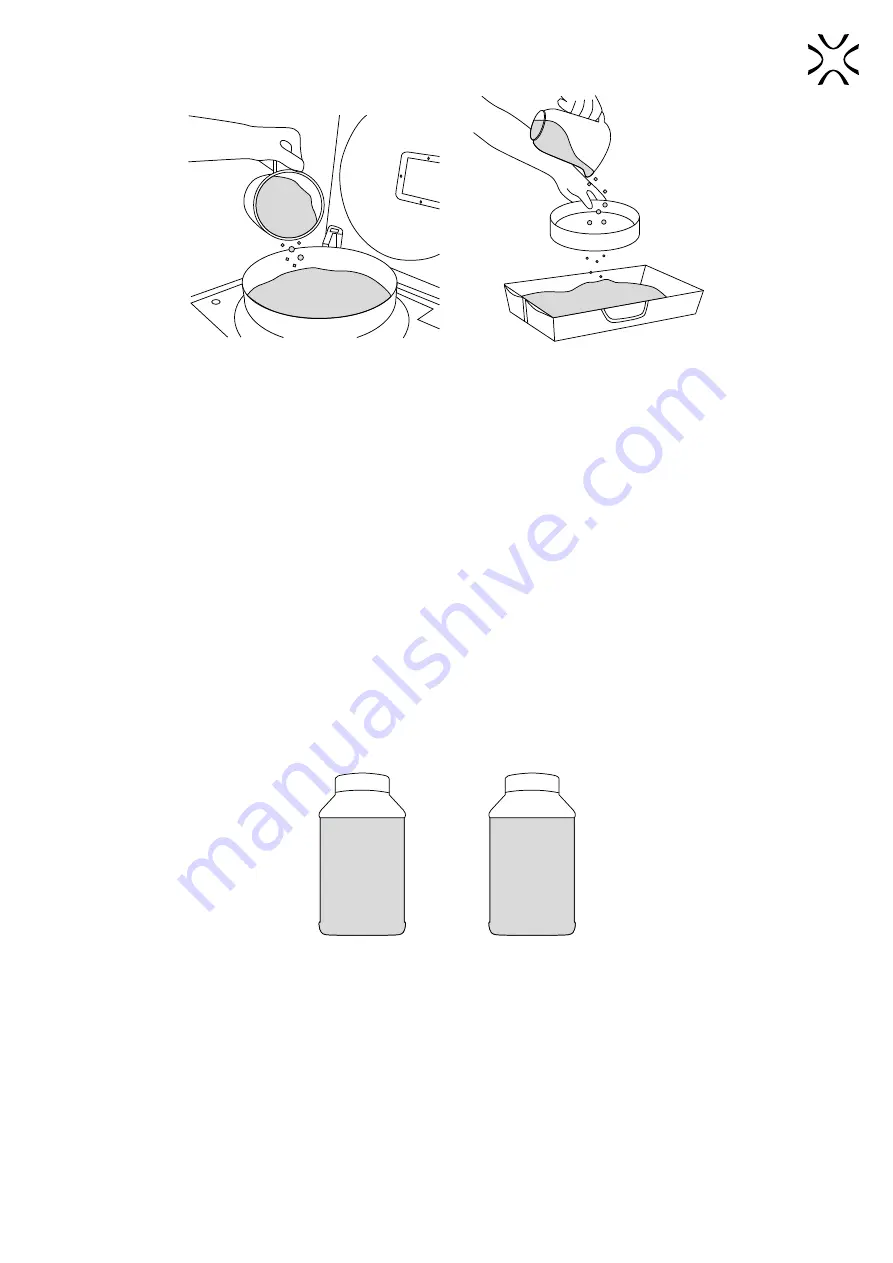
Sinterit LISA PRO User Manual | 47
Two ways of manually sifting the powder (Sinterit Powder Sieve or Metal sieve).
9.
Printouts are cleaned and ready to use. They may also undergo further processing (e.g. polishing, sealing, painting).
C. POSTPROCESSING: PAINTING AND LACQUERING
SLS parts can be spray painted and/or coated with lacquer (varnish or clear coat). Via lacquering it is possible to obtain
various finishes, such as high gloss or metallic sheen. Lacquer coatings can also improve wear resistance, surface
hardness, water-tightness and limit marks and smudges on the surface of the part. Due to the porous nature of SLS, it
is recommended that 4- 5 very thin coats are applied to achieve a final finish rather than one thick coat. This results in
faster drying time and reduces the likelihood of the point or lacquer running.
13. Powder refreshment process
1. This chapter will explain the process of refreshing powders that need it.
2.
Full information about refresh ratio and recommendations can be found in specifications of each material that can
be found at www.sinterit.com
3.
Some powders (i.e. Flexa Grey) do not need to be mixed with fresh powder. It is sufficient to sift them after use in
the printer (e.g. using Sinterit Powder Sieve or Sinterit PHS). After this process, the powder is ready for the next use.
100%
USED
READY
=
For FLEXA Grey powders, there is no need to add fresh powder.
4.
Powders need to be sifted (powder from the printer), a fresh powder added (appropriate amount - see further) and
mixed (homogenisation).
5.
The exact amount of Fresh Powder that should be added to that used powder (from the printer) can be found in
the Sinterit Studio report (generated together with the xxx.scode file) and on the printer screen, during the cleaning
process (see chapter 11, subchapter B or C).