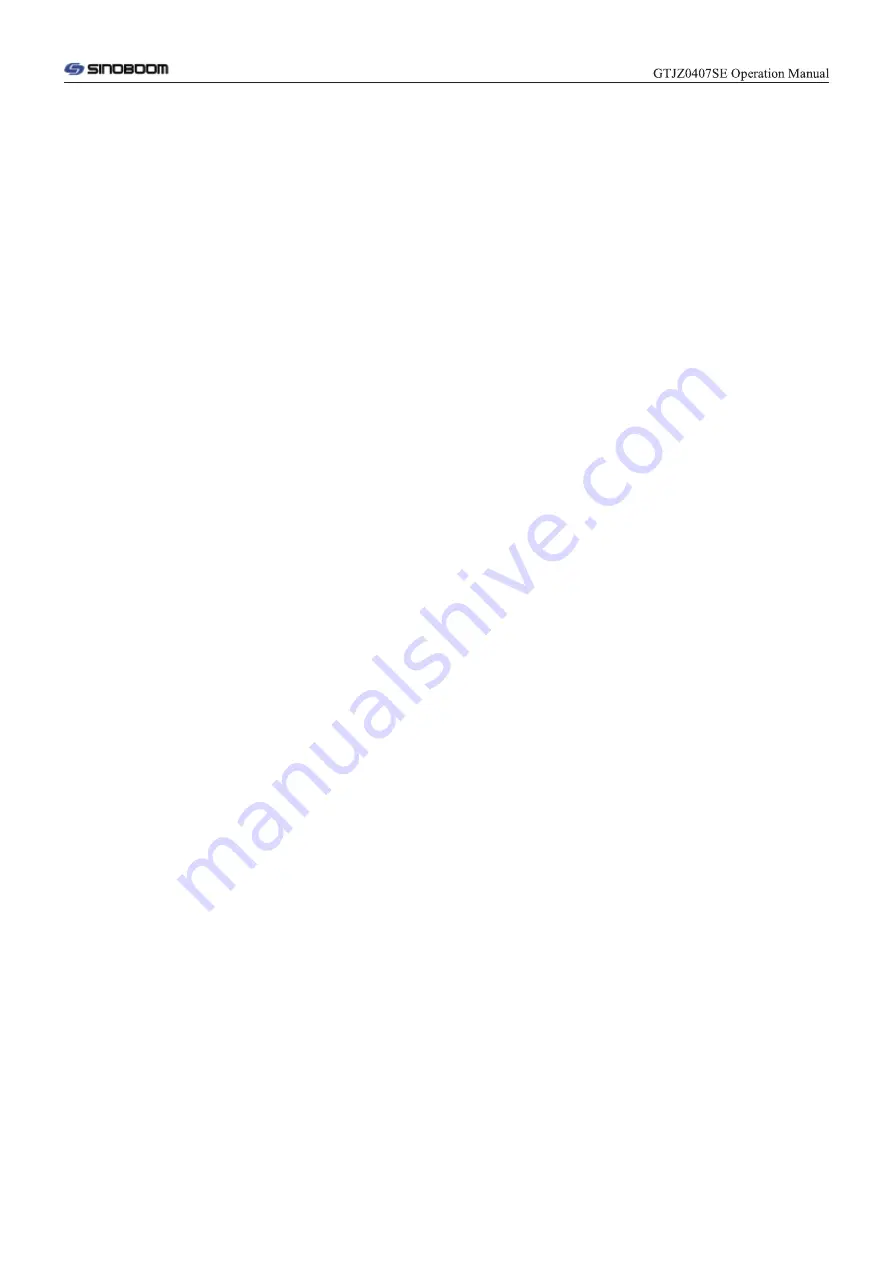
Extend and retract platform
1
、
Press the pedal
2
、
Hold and push the extension platform guardrail.
Caution: Don’t stand on the extension platform while it moving or not fixed. There are three
fixing position for extension platform.
3
、
Press the pedal ,extract the platform to the end, lose the pedal and make sure it is fixed.
Support and folding platform guardrail
The platform guardrail can be folded to facilitate transportation .when used ,the platform guardrail
is supported .The platform guardrail system includes a folding guardrail part of a secondary
platform and a folding guardrail part of a fixed platform .All sections are secured by four wire
rope safety pins in place.
1
、
Completely reducing platform and retracting the platform.
2
、
Take down the platform controller.
3
、
From inside the platform , two steel wire rope safety pins on the front part of the platform are
extended to extend the front guardrail of the platform. Don’t put your hands where you can
hurt your hands.
4
、
Fold the guardrail on both sides . Do not place your hands where can hurt your hands.
5
、
Remove two wire rope safety pins at the back of the stationary platform.
6
、
Be careful to open the door and move to the ladder or the ground.
7
、
Fold the door guardrail and the entry guardrail into one device.
8
、
Fold the guardrail on both sides . Do not place your hands where can hurt your hands.
When used, the platform guardrail is supported in the opposite order . Support each side guardrail
with safety wire pin to ensure accurate installation.
Platform guardrail position relation reference vehicle description part.
Use controller on ground
Keep safe distance between operator, machine and fixed object.
Pay attention to the driving direction when using controller.
Battery level indicator
Check the battery level by the indicator in platform.
24