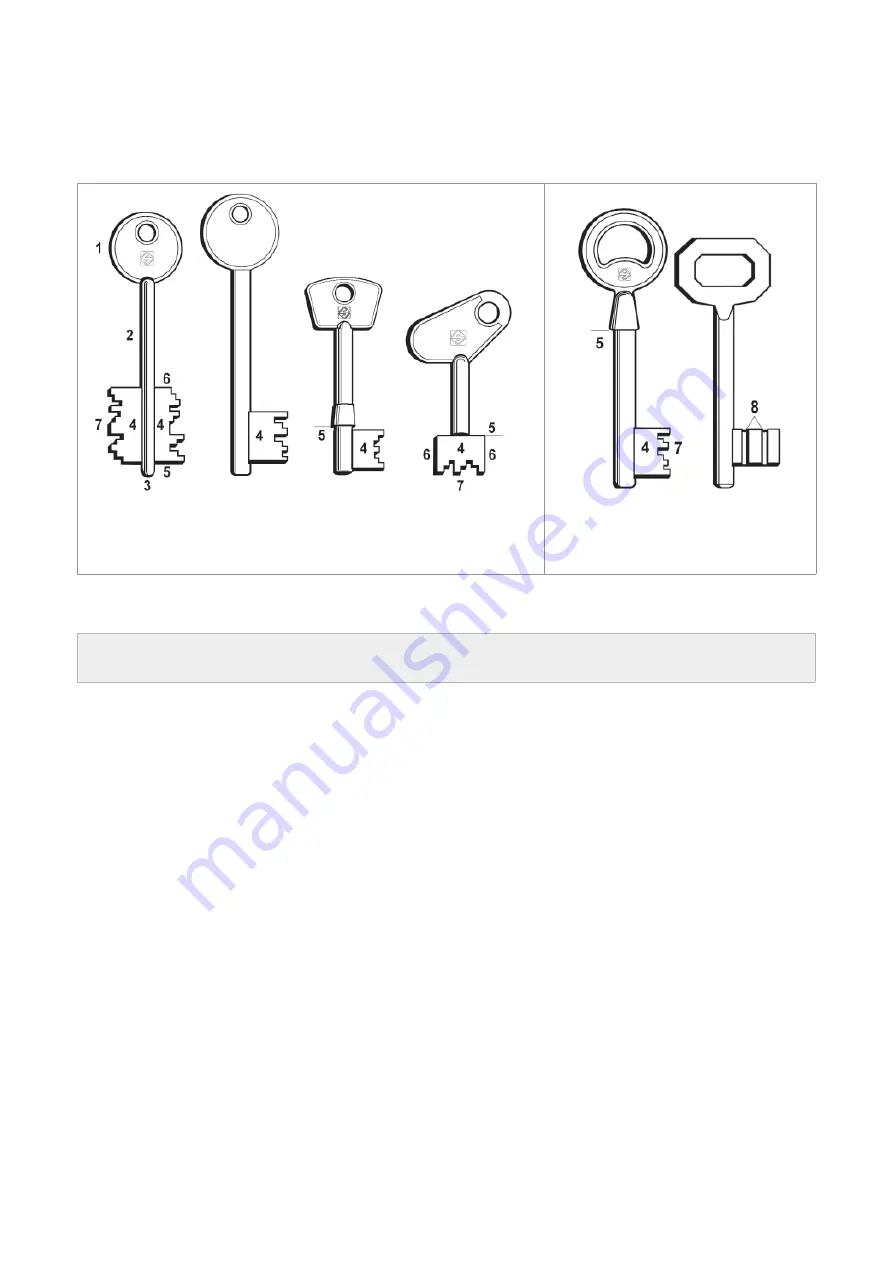
TERMINOLOGY
For those inexperienced in the subject of keys and key cutting, below is an illustration of the most frequently used
terms:
Keys with rear stops
and keys with vertical cuts:
STANDARD with
OMNIA MAX and OMNIA W MAX
Fig.2
1) Head
2) Stem
3) Tip
4) Bit
5) Stop
6) Side
7) Cuts
8) Vertical
cuts
Operating Manual
OMNIA / OMNIA 650rpm / OMNIA MAX / OMNIA W MAX
Copyright Silca 2014
2