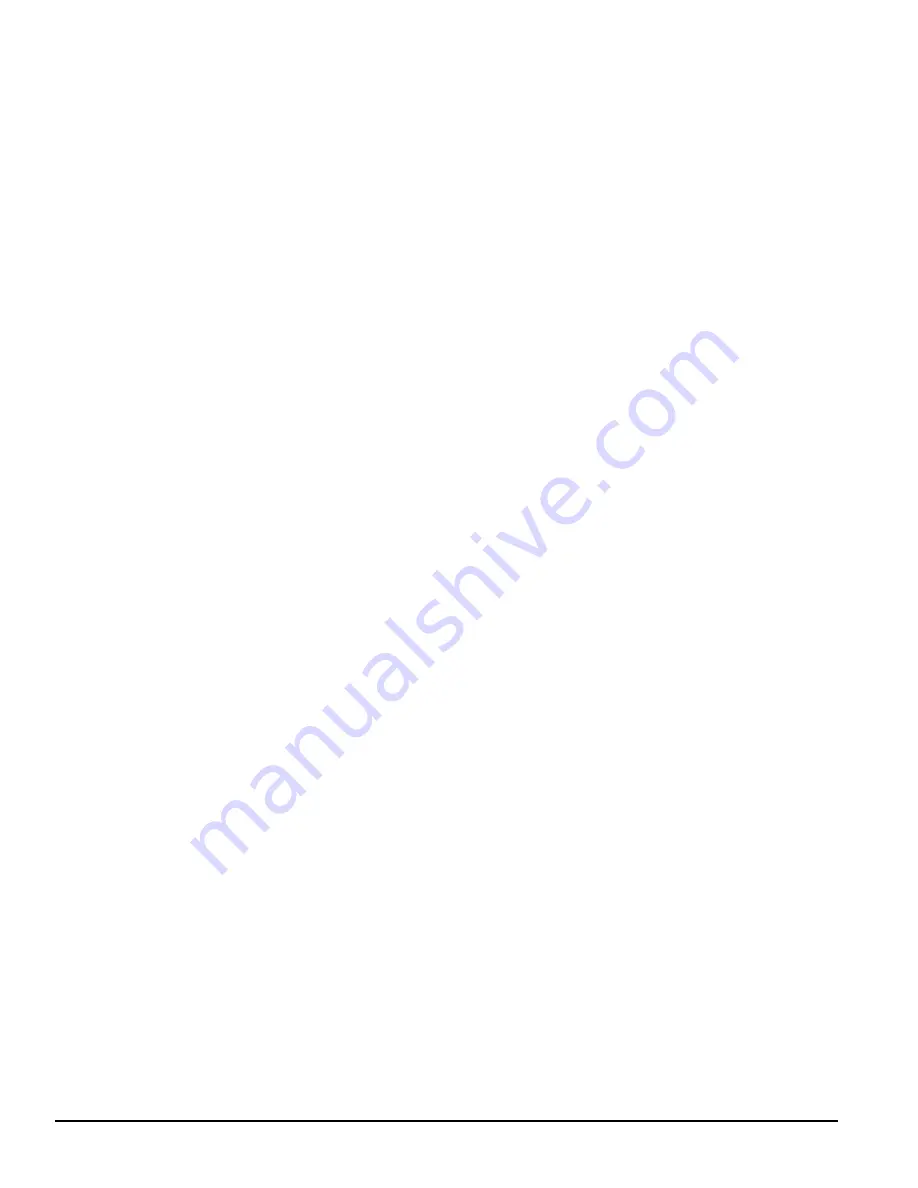
5 Maintenance
5.1 Maintenance Quick Check List
Failure to properly maintain the equipment can result in death,
serious injury, or product failure. The instructions contained
herein should be carefully reviewed, understood, and fol-
lowed. The following maintenance procedures must be per-
formed regularly.
Scheduling
Schedule maintenance appropriate to the severity of
service.
Consider environment (dampness, heat, and dust), severity
of operations, and the importance of the machinery being
controlled.
Control unit maintenance should coincide with inspection
of the motor being controlled.
Buswork inspection entails shutting down the entire control
center.
Cleaning (page 33)
Use a vacuum cleaner, not compressed air.
Excess deposits of foreign materials signify faulty gasketing.
Pay particular attention to conductive deposits.
Loose Connections (page 33)
Periodic checking of tightness of connections promotes
reliability and reduces heating.
Overheating and discolorations signify loose connections.
Torque horizontal bus bolts to 20 ft.-lbs.
Torque incoming line connections to main lugs only to
85 ft.-lbs.
Torque all incoming connections to main circuit breakers
and fusible disconnects as per the breaker or disconnect
manufacturer’s recommendations. The torque requirements
will be found on a label located on the disconnecting
device.
Test Position Plug-in Units (page 24)
Unscrew the locking latch in the lower front left-hand
corner and disengage latch from separator angle.
Release the racking lever in the top barrier plate.
Slide unit out to the positive stop on the shelf brackets.
As many as two padlocks may be used to lock unit in “test”
position to prevent accidental stab engagement.
Contacts
Make sure that all contacts are free from extraneous
materials, excess pitting or burning.
Check for spring pressure.
Lubricate stab connections with approved lubricant.
Locking in Engaged Position (page 34)
To lock in ON, drill out the indentations on the disconnect
operating handle and insert a padlock (see pg. 14).
To lock in OFF, as many as three padlocks may be inserted
in the disconnect operating handle.
Field Additions of Sections (page 24)
For field additions of sections, follow the same procedure as
for the field assembly of shipping splits (pg. 2 and 5).
Addition and Replacement of Control Units (page
24-26)
De-energize motor control center
Adding to a Blank Unit Space (page 25)
Open blank door.
Remove hinge pins with door open.
Close door halfway and remove door.
If necessary, install unit support assembly and blank covers
or doors.
Insert shelf brackets at a slight angle into vertical bus
support angle and snap into place.
Secure brackets by fastening the right-hand bracket to bus
support angle and the separator angle to the left side of
structure with the two screws provided.
Mount unit door. (Opposite procedure of removing blank
door.)
Remove (if required) unit stab hole covers.
Verify that stab is lubricated with approved lubricant.
Slide control unit into place with disconnect handle in .OFF..
Complete engagement by closing racking lever. Engage
locking latch to separator angle and screw down.
Connect outgoing power and control wiring.
Close door and perform pre-operation checks (see page 29).
Replacing with Unit of the Same Size (page 25)
If possible, de-engenergize motor control center.
Move disconnect operating handle to OFF.
Open door, loosen and disengage locking latch.
Open vertical wireway door.
Move unit to .test. position.
Disconnect control and load wiring
Remove unit by tilting and sliding out.
Reverse procedure for replacement unit.
Perform pre-operation checks (see page 29).
Rearranging Control Units of Different Sizes (page 25)
Remove all necessary units, doors and unit support
assemblies.
Realign support assemblies where appropriate.
Remove stab hole covers where appropriate (and cover the
stab hole covers that will not be used).
Mount unit doors.
Install rearranged units.
Insulation Test (Megger) (page 27)
This checklist does not represent an exhaustive survey of
maintenance steps necessary to ensure safe operation of the
equipment. Particular applications may require further proce-
dures. Should further information be desired or should particu-
lar problems arise which are not covered sufficiently for the
purchaser.s purposes, the matter should be referred to the
local Siemens sales office.
Dangerous voltages are present in the equipment which can
cause death, serious injury, or property damage. Always de-
energize and ground the equipment before maintenance.
Maintenance should be performed only by qualified personnel.
The use of unauthorized parts in the repair of the equipment,
tampering by unqualified personnel, will result in dangerous
conditions which can cause death, serious injury, or equip-
ment damage. Follow all safety instructions contained herein.
Siemens Energy & Automation, Inc.
31