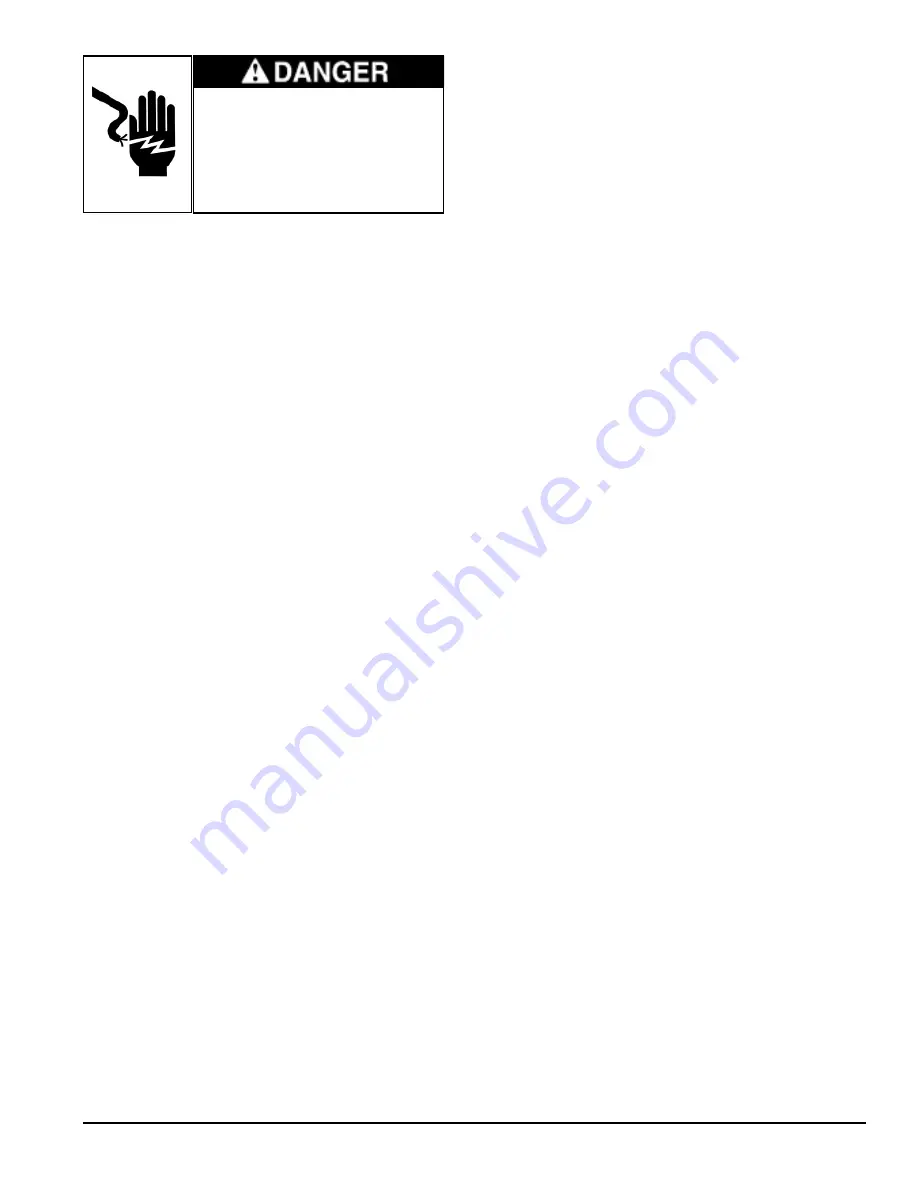
Hazardous voltage.
Will cause death or serious
personal injury.
Turn off power before working on this
equipment.
3.10 Pull Box Installation
Refer to Figure 15 for the following procedure.
1. Remove top front conduit plate from motor control center
structure by removing two screws (B).
There are two front plates on .back-to-back. motor control
centers.
2. Remove two rear screws (C).
3. Remove the top two screws holding on the bus insulator
cover (E).
Do this to both sides of a .back-to-back.motor control center.
4. Install barrier (F) and replace the screws from step 3.
5. Remove top plate of pull box (G).
6. Place pull box on MCC and screw down using four 1/4-20 x
3/4.Taptite screws. The rear mounting holes may have to be
drilled on .Front Only. motor control center.s. Use the Pull
Box/Top Hat as a drilling template.
7. Replace top plate that was removed in step five.
3.11 Incoming Power Connections
Note:
Remove top covers before cutting holes for conduit to
prevent metal chips from falling into the motor control center.
Conduits should be carefully installed to prevent moisture or
water from entering and accumulating within the enclosure.
All conduits (including stubs) should be bonded to the motor
control center. After all shipping sections are in place, leveled,
and joined together into a single motor control center, cables
may be pulled and top entry conduit may be installed. Bottom
entry conduit will have been stubbed through the floor at the
proper locations prior to placement of the motor control cen-
ter. The incoming source cables may be connected at this time,
however, the power source disconnecting means must remain
open and locked out until all wiring is completed and the
entire system has been checked out.
Care must be exercised to make sure that the lugs which have
been provided are suitable for use with the type of cables
being installed in the motor control center. If crimp lugs are
supplied, use only the crimping tool recommended by the lug
manufacturer.
Care should be exercised in stripping insulation from the con-
ductors to prevent nicking the conductor. For aluminum, clean
all oxide from the stripped portion and apply inhibiting com-
pound at once. Tighten all screw lugs and bolted electrical
connections to the specified torque listed in the table in the
maintenance section of this instruction manual.
To minimize the length of unsupported cable, the shortest,
most direct routing should be chosen. However, the largest
practical bending radii should be maintained to avoid damag-
ing the insulation and to avoid causing terminals to loosen. All
cables entering the motor control center must be adequately
supported and restrained to withstand the maximum fault cur-
rent capable of being delivered by the source. The recom-
mended distances between straps for 80 pound rated strap is
6 inches for 25 KA bracing, 4 inches for 42 KA bracing and 3
inches for 65 KA bracing. Using a strap rated less than 80
pounds will require the spacing distances to be reduced. For
100 KA bracing, cables must be supported in accordance with
the special instructions provided with the motor control center.
Siemens Energy & Automation, Inc.
16