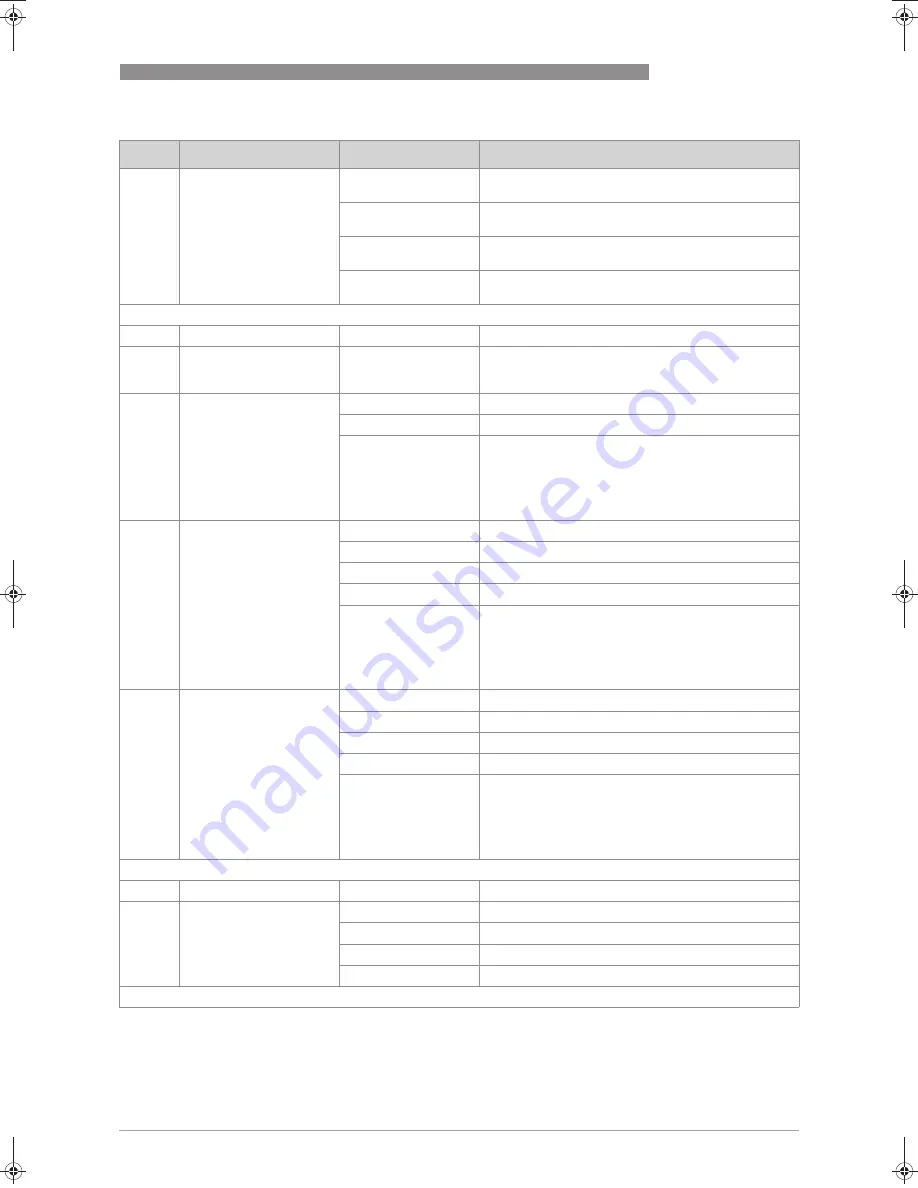
OPERATION
6
59
SITRANS FX300
www.siemens.com/flow
06/2009 - SFIDK.PS.050.F2.02 A5E02100423
(available if Maes.Inst =
Mass, see menu item
1.1.3)
kg
Unit
↑
...
^
Select totalizer unit for mass flow measurement
0000000000
kg
↑
…
↑
...
↑
...
^
Enter preset totalizer value
Reset Yes /
Reset No
↑
...
^
Reset totalizer
Do not reset totalizer/
Disp. off /
Disp. on
↑
...
^
Do not display totalizer
Display totalizer /
3.3
HART settings
3.3.1
Poll. Addr..
→
000
0
–
15
↑
…
→↑
...
→↑
...
^
Enter HART polling address for "Multidrop mode"
3.3.2
HART SV
→
HART secondary variable
Total Flow
↑
...
FAD
↑
...
^
#available if Meter
Type = FAD meter (see
menu item 5.3.1,
service personnel
only)
3.3.3
HART TV
→
HART tertiary variable
Temp.
↑
...
Pressure
↑
...
Density
↑
...
FAD
↑
...
^
#available if Meter
Type = FAD meter (see
menu item 5.3.1,
service personnel
only)
3.3.4
HART 4V
→
HART quaternary variable
Temp.
↑
..
Pressure
↑
...
Density
↑
...
FAD
↑
...
^
#available if Meter
Type = FAD meter (see
menu item 5.3.1,
service personnel
only)
3.4
Set fluid and medium
3.4.1
Fluid
1
→
Set fluid type
Gas
↑
...
Gas
Gas Mix.
↑
...
Gas mixture
Wet Gas
↑
...
^
Wet gas
1
When changing fluid: check density
Level
Designation
Selection / entry
Explanation
MA_Siemens_Sitrans_FX300_R02_en_PRT.book Page 59 Monday, June 22, 2009 8:17 AM
Summary of Contents for SITRANS FX300
Page 1: ......
Page 79: ...NOTES 9 79 SITRANS FX300 www siemens com flow 06 2009 SFIDK PS 050 F2 02 A5E02100423 ...
Page 80: ......