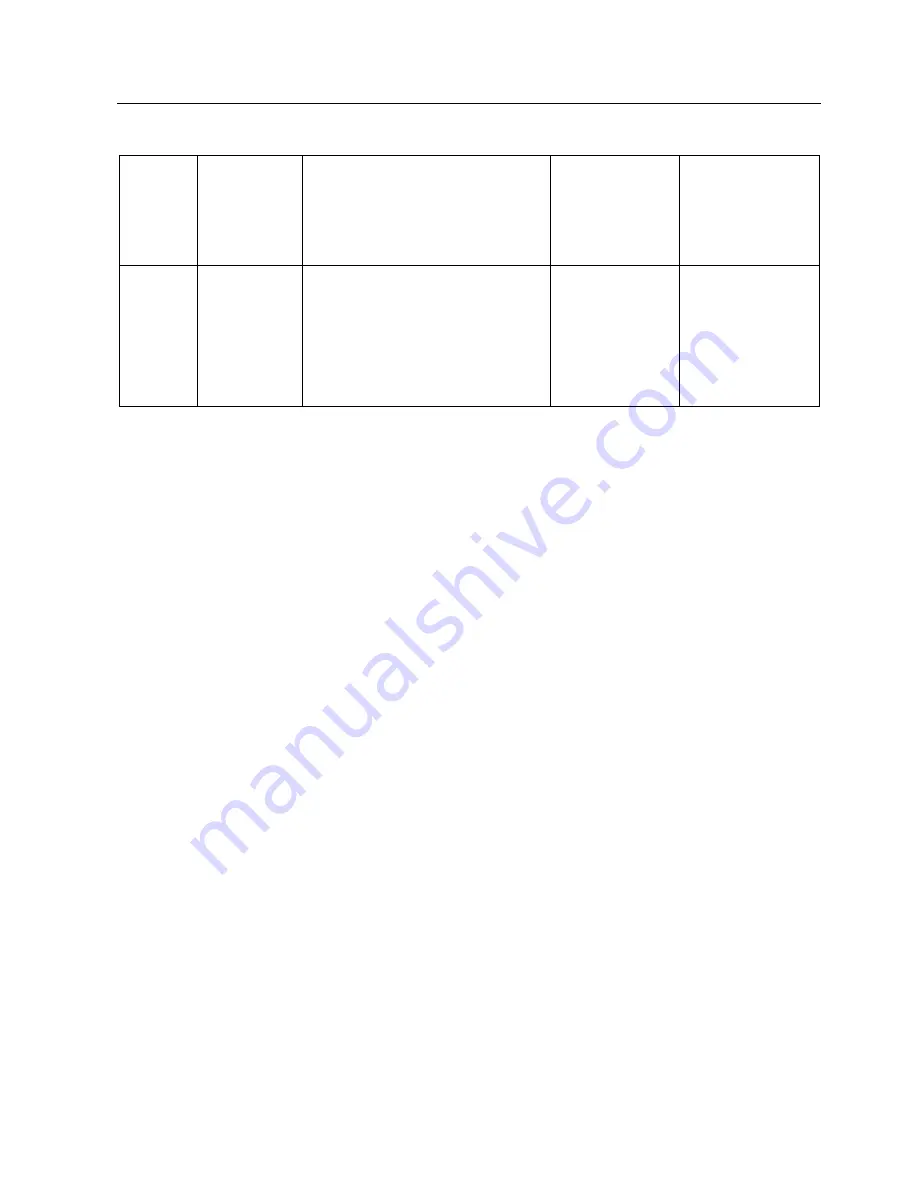
Parameters
SITRANS F M TRANSMAG 2
Operating Instructions, 11/2009, A5E00102775-07
89
6.7.4
Excitat.Freq.
5
Magnetic current curve:
•
Bipolar PP f/5: Standard applications
•
Bipolar f/3: rapid applications
•
Unipolar f/6: Measuring sensors
≦DN150 up to year of construction
1995
Bipolar PP
•
PP f/5
•
Bipolar f/3,
•
Unipolar f/6
6.7.5
EmptyTube Det.
Act.Value El
1
Act.Value El
2
Threshold
Adjustment of electrode immersion check
Display of actual control value of
electrode El1 in % of end value
Display of actual control value of
electrode El12 in % of end value
Threshold of diagnostic function
"Immersion check" for "Tube empty"
message (see menu 2.3)
33 %
5 to 95 %
1)
Parameters apply only to devices with 20 mA/Hart communication and digital output 2 (7ME5034-0xxxx)
2)
Parameters apply only to devices with 20 mA/Hart communication and digital input (7ME5034-2xxxx)
5)
Parameters apply only to devices with 20 mA/Hart communication and digital input (7ME504x-2xxxx)