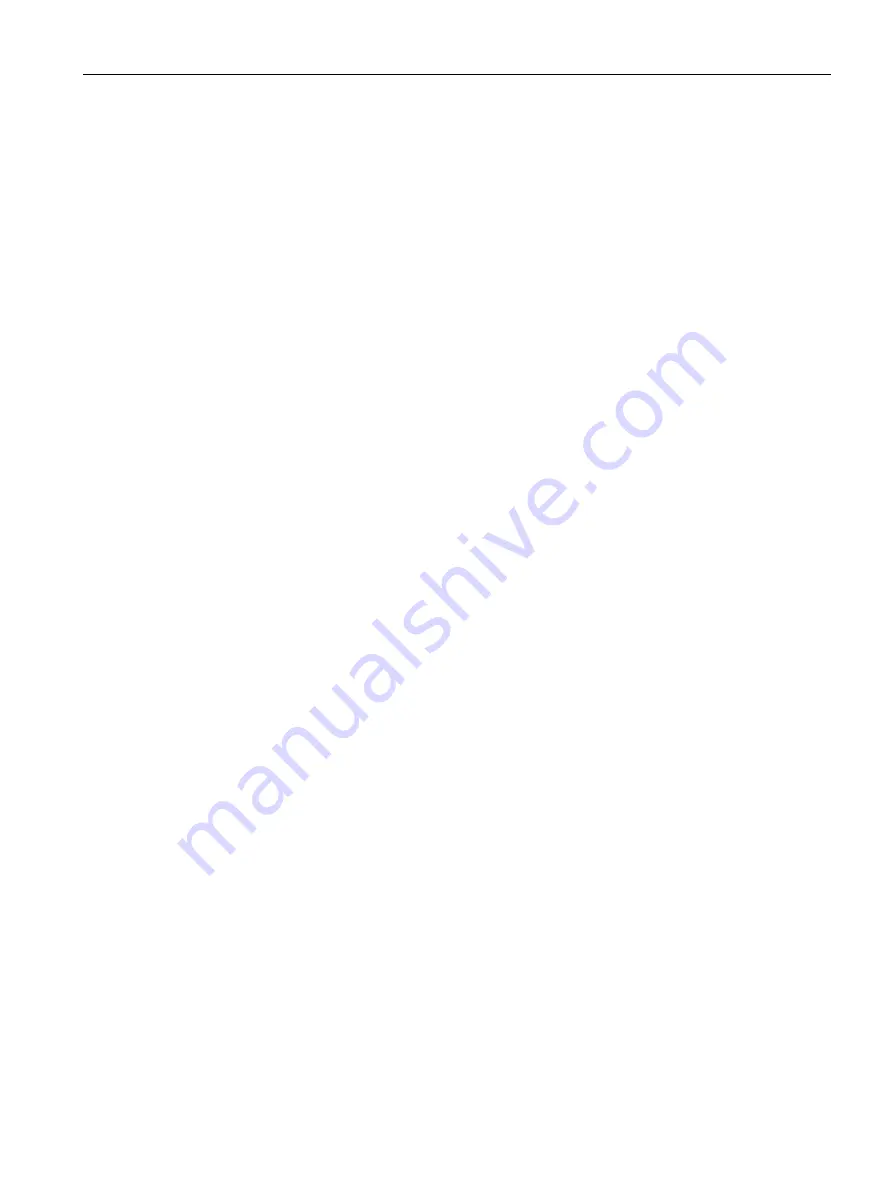
Connecting up, switching on
4.6 EMC compliant connection
Power Module PM330
Hardware Installation Manual, 10/2016, A5E32844552B AD
51
The most favorable design is to mount these devices and supplementary components on
a bare metal mounting plate with good conducting characteristics; this in turn is
connected to the control cabinet frame through a good electrical connection and the
largest possible surface area. It is especially important that they are connected to the PE
and EMC shield bars.
●
All of the connections must be implemented so that they are durable. Screw connections
to painted or anodized metal components must either be established using special
contact (serrated) washers that cut through the insulating surface - and therefore
establish a metallic conducting contact - or the insulating surface must be removed at the
contact locations.
●
Coils of contactors, relays, solenoid valves and motor holding brakes must be equipped
with interference suppression elements in order to dampen high-frequency radiation
when switching-off (RC elements or varistors with AC coils and free-wheeling diodes or
varistors for DC coils). The protective circuit must be directly connected at the coil.
4.6.4
Cabling
Routing cables inside the cabinet
●
All power cables for the drive (line cables, DC link cables, connecting cables between the
Braking Module and the associated braking resistor as well as motor cables) must be
routed separately from signal and data cables. The minimum distance should be
approximately 25 cm. Alternatively, the decoupling can be realized in the control cabinet
using metal partitions (separating elements) connected to the mounting plate through a
good electrical connection.
●
Filtered line cables with a low noise level, i.e. line cables from the line supply to the line
filter, must be separately routed away from non-filtered power cables with high noise
levels (line cables between the line filter and rectifier, DC link cables, connecting cables
between the Braking Module and the associated braking resistor as well as motor
cables).
●
Signal and data cables, as well as filtered line supply cables, may only cross non-filtered
power cables at right angles to minimize coupled-in interference.
●
Cables should be kept as short as possible, unnecessary cable lengths must be avoided.
●
All cables must be routed as closely as possible to grounded housing components, such
as mounting plates or the cabinet frame. This reduces interference radiation as well as
coupled-in interference.
●
Signal and data cables, as well as their associated equipotential bonding cables, must
always be routed in parallel and with the shortest distance possible between them.
●
When unshielded single-conductor cables are used within a zone, the feed and return
lines must be either routed in parallel with the minimum possible distance between them,
or twisted with one another.
●
Spare conductors for signal and data cables must be grounded at both ends to create an
additional shielding effect.
●
Signal and data cables should enter the cabinet only at one point (e.g. from below).
Summary of Contents for SINAMICS G120P PM330
Page 1: ......
Page 2: ......
Page 18: ...Introduction Power Module PM330 18 Hardware Installation Manual 10 2016 A5E32844552B AD ...
Page 97: ......
Page 98: ......