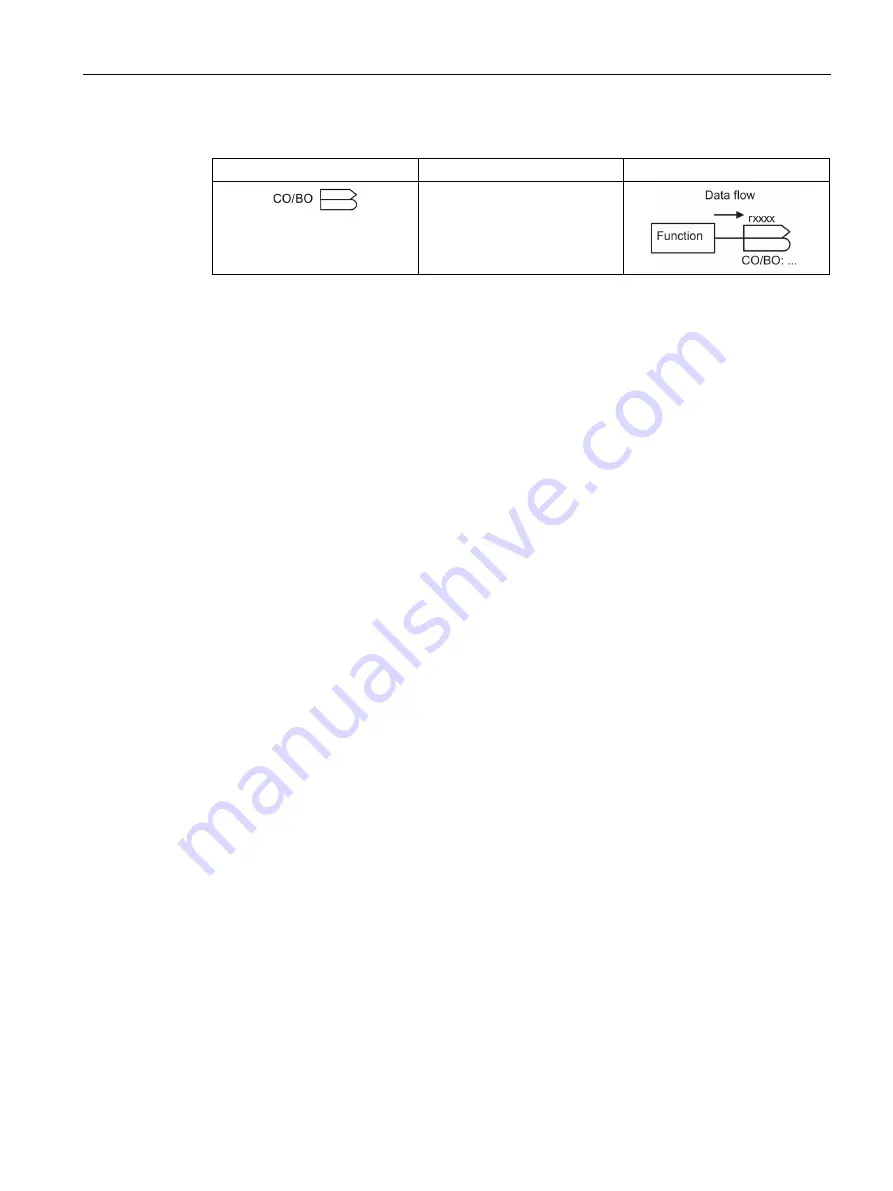
Introduction
2.3 Extended adaptation of parameters
SINAMICS G110D
Operating Instructions, 07/2016, FW V3.63, A5E36768472B AB
25
Table 2- 11 Connector and binector output symbols
Abbreviation and symbol
Description
Function
Binector/connector output
When do you need to use BICO technology?
BICO technology allows you to adapt the inverter to a wide range of different requirements.
This does not necessarily have to involve highly complex functions.
Example 1: Assign a different function to a digital input.
Example 2: Switch over the speed setpoint from the fixed frequency to the analog input.
What precautions should you take when using BICO technology?
Always apply caution when handling internal interconnections. Note which changes you
make as you go along since the process of analyzing them later can be quite difficult.
The STARTER commissioning tool offers various screens that make it much easier for you
to use BICO technology. The signals that you can interconnect are displayed in plain text,
which means that you do not need any prior knowledge of BICO technology.
What sources of information do you need to help you set parameters using BICO
technology?
●
This manual is sufficient for simple signal interconnections, e.g. assigning a different
significance to the to digital inputs.
●
The parameter list in the List Manual is sufficient for signal interconnections that go
beyond just simple ones.
●
You can also refer to the function diagrams in the List Manual for complex signal
interconnections.
Summary of Contents for SINAMICS G110D
Page 1: ......
Page 2: ......
Page 8: ...Table of contents SINAMICS G110D 8 Operating Instructions 07 2016 FW V3 63 A5E36768472B AB ...
Page 223: ......
Page 224: ......