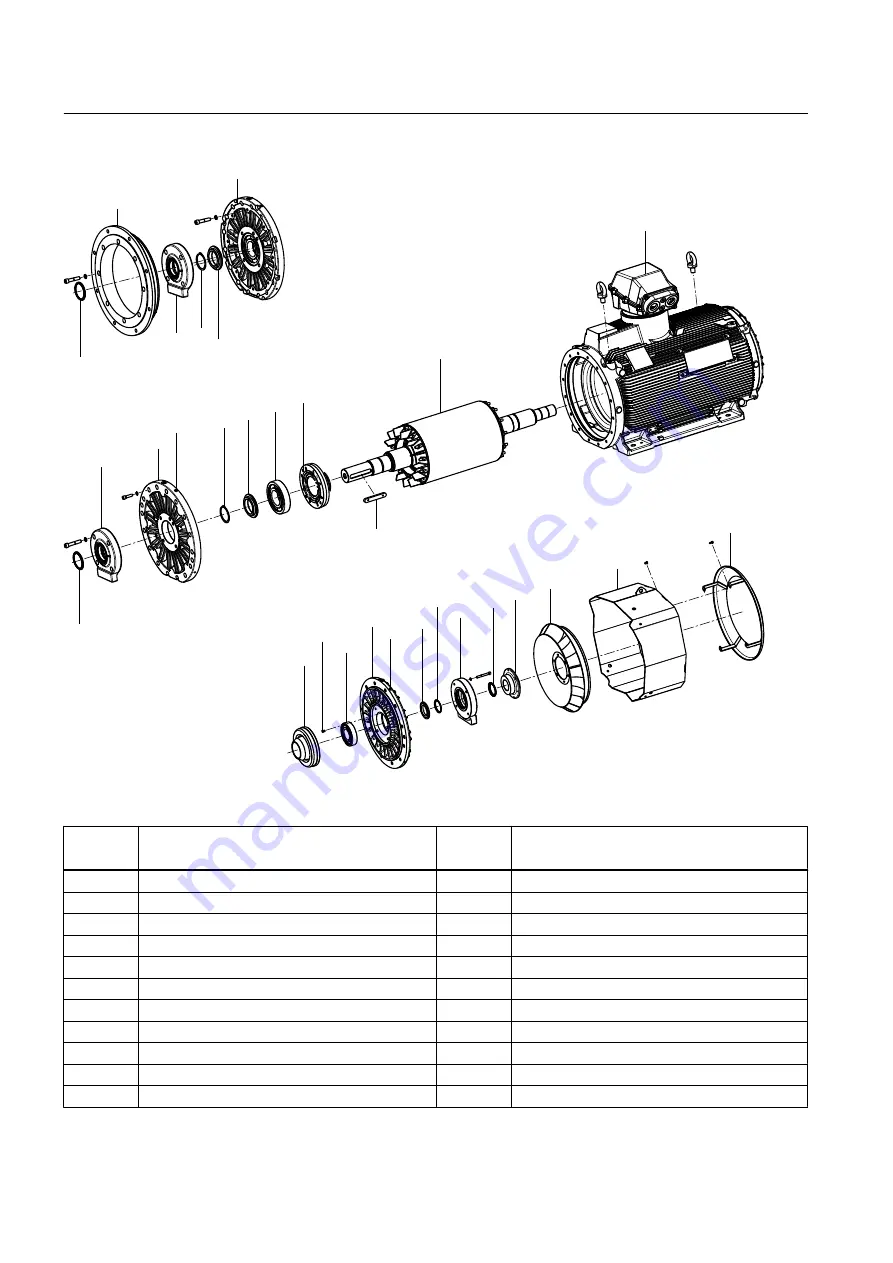
,09%
,0%
Figure 10-4 E-DN000-0010
Parts
Number
Designation
Parts
Number
Designation
2.00
Rotor, complete (balanced)
4.25
Compression spring
2.01
Keyway
4.30
Grease chamber cover NDE, outer
3.01
Bearing shield DE
4.32
Grease chamber cover NDE, inner
3.02
Flange bearing shield DE
4.35
Snap ring
3.08
Flange plate DE
4.38
Grease slinger NDE
3.21
Bearing shield NDE
4.44
Sealing ring NDE, outer
4.00
Grease nipple
5.01
Fan cowl, complete
4.01
Bearing DE
5.04
Fan hub NDE
4.05
Bearing NDE
5.11
Protective cover
4.10
Grease chamber cover DE, outer
5.56
Fan, complete
4.12
Grease chamber cover DE, inner
6.00
Terminal box, complete
Spare parts
10.8 Spare parts list, frame size 355
LOHER CHEMSTAR 1PS5
106
Operating Instructions 03/2014
Summary of Contents for SIMATIC S5 1P 243
Page 2: ...11 03 2014 02 49 V4 00 ...
Page 12: ...Introduction LOHER CHEMSTAR 1PS5 12 Operating Instructions 03 2014 ...
Page 20: ...Safety notes 2 11 Ventilation LOHER CHEMSTAR 1PS5 20 Operating Instructions 03 2014 ...
Page 66: ...Electrical connection 6 2 Connecting LOHER CHEMSTAR 1PS5 66 Operating Instructions 03 2014 ...
Page 124: ...Disposal 11 4 Disposal of components LOHER CHEMSTAR 1PS5 124 Operating Instructions 03 2014 ...
Page 136: ...Quality documents C 4 Data LOHER CHEMSTAR 1PS5 136 Operating Instructions 03 2014 ...
Page 140: ...Index LOHER CHEMSTAR 1PS5 140 Operating Instructions 03 2014 ...
Page 141: ...AC EC Declaration of Conformity U161 AB EC Declaration of Conformity U163 AA R No 20000h U165 ...