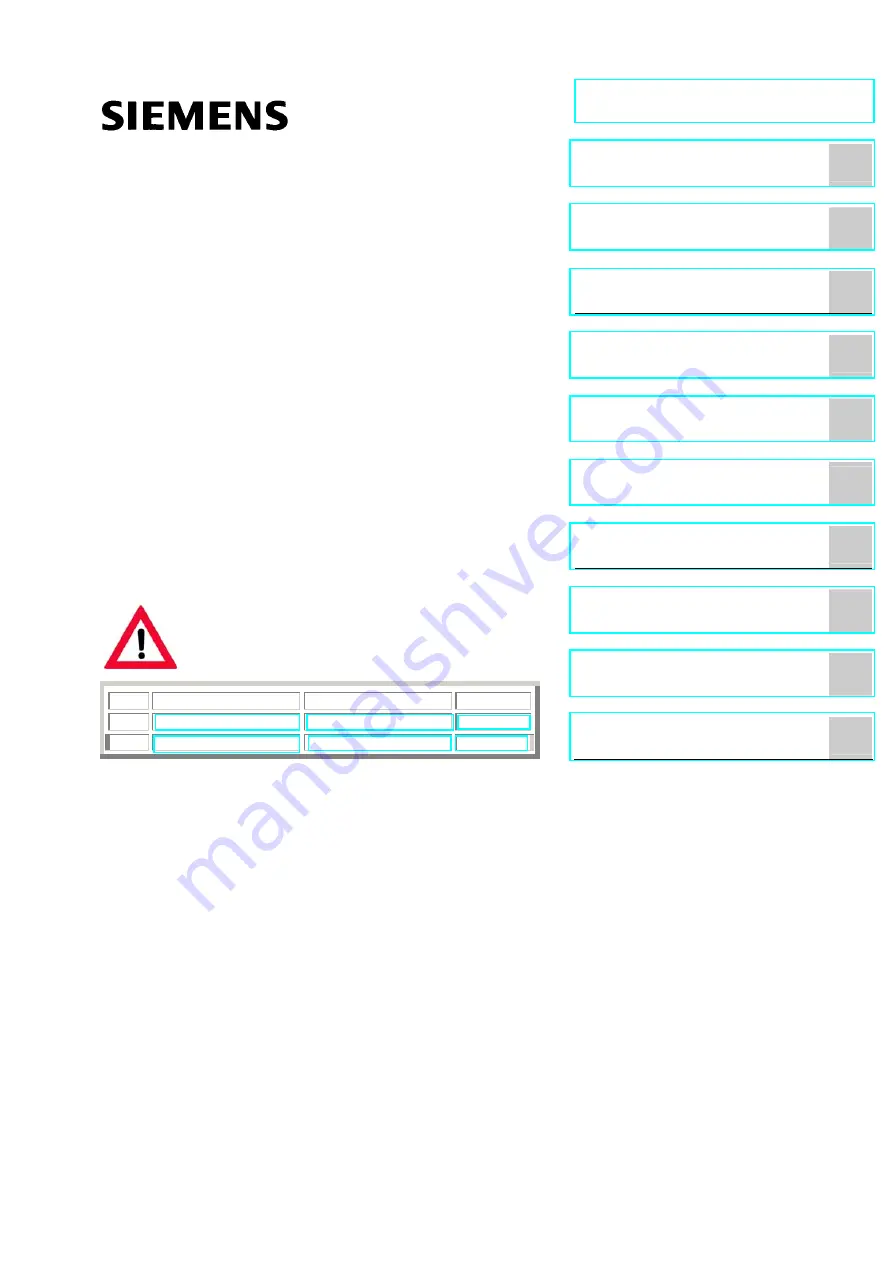
SIMATIC HMI Fail-safe operation of the Mobile Panel 277F IWLAN
______________
______________
______________
______________
______________
______________
______________
______________
______________
______________
SIMATIC HMI
Fail-safe operation of the
Mobile Panel 277F IWLAN
Function Manual
08/2008
A5E01003779-01
Version 1.04
Order No. 6AV6691-1FQ01-2AB0
The following supplement is part of this documentation:
No. Designation
Drawing
number
Edition
Information A5E01005059-01 09/2008
Information A5E01004934-02 10/2008