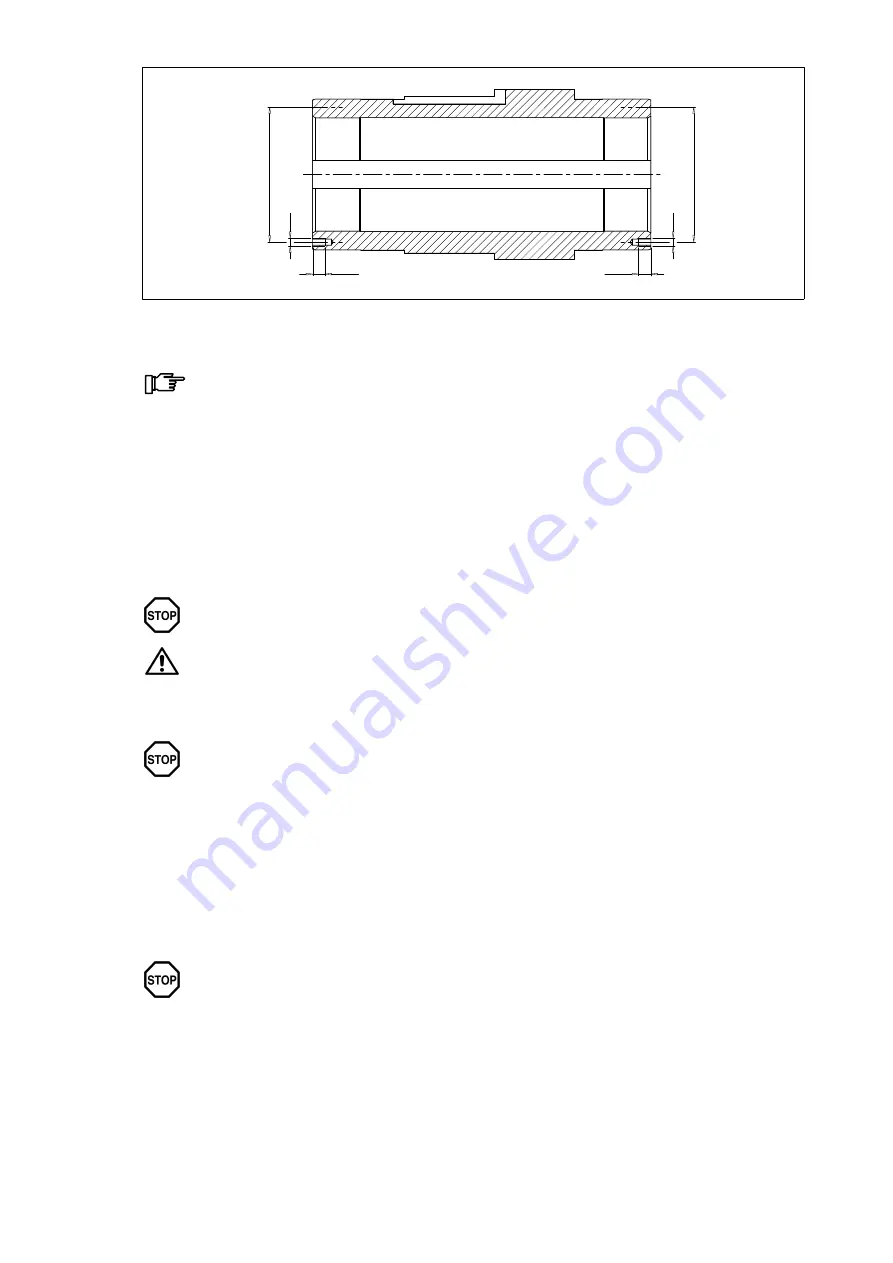
BA 5230 en 04/2011
t
t
*
)
*
)
m
s
m
s
s
Fig. 18:
Hollow shaft with parallel keyway
For exact dimensions, refer to the drawings in the gearunit documentation.
When using forcingoff screws or threaded spindles, the head of the thread pressing against
the driven machine should be rounded and well greased to reduce the risk of seizing at this
point.
6.5
Shaftmounted gear unit with hollow shaft and shrink disk
The end of the drivenmachine shaft (material C60+N or higher strength) must have a centring means to
DIN 332 Form DS (with thread) in its end face (for connecting dimensions of the drivenmachine shaft,
see dimensioned drawing in the gearunit documentation).
6.5.1
Fitting
•
Remove the corrosion protection from the hollow shaft and machine shaft with a suitable cleaning
agent.
The cleaner must not be allowed to come into contact with the shaftsealing rings.
Ensure adequate ventilation. Do not smoke.
Danger of explosion.
•
Check the hollow and machine shafts to ensure that seats and edges are not damaged. If necessary,
rework the parts with a suitable tool and clean them again.
The bore of the hollow shaft and the machine shaft must be absolutely free of grease
in the area of the shrinkdisk seat.
This is essential for safe and reliable torque transmission.
Do not use contaminated solvents or dirty cloths for removing grease.
6.6
Shrink disk
The shrink disk realizes a pressfit connection between a hollow shaft and a stub or machine shaft (in the
following called "stub shaft"). The interference fit can transfer torques, bending moments and forces. The
jointing pressure between the hollow and stub shafts generated by the shrink disk is essential for the torque
and/or force transmission.
The shrink disk is delivered ready for installation.
The shrink disk must not be disassembled before fitting for the first time.
Fitting and startup must be carried out by properly trained specialist personnel. Prior
to startup these instructions must be read, understood and adhered to. We accept no
liability for personal injury or damage due to nonobservance.