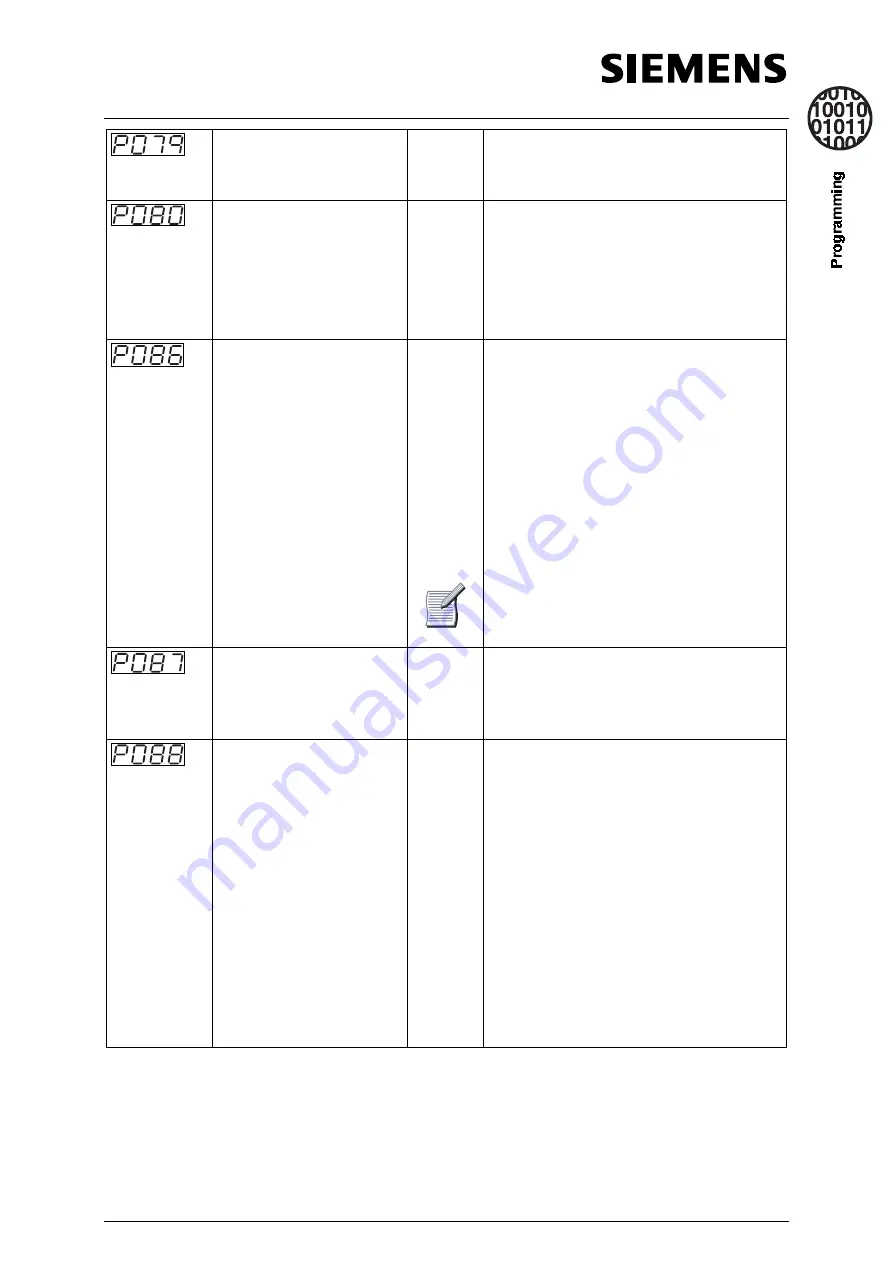
ECO REFERENCE MANUAL
13-15
Starting boost
0 -250
[50]
Sets additional current during ramping to
ensure consistent starting and to overcome
stiction effects
Nominal rating plate motor
power factor (cos
ϕ
)
0.00-1.00
[
¶¶¶
]
If efficiency is shown on the motor rating
plate, calculate the power factor as follows:
pf =
If neither power factor nor efficiency are
shown on the motor rating plate - set P080 =
0.
•
Motor current limit (%)
0 - 200
[100]
Defines the motor overload current as a %
of the Nominal motor current (P083)
allowed for up to one minute.
With this parameter and P186, the motor
current can be limited and overheating of
the motor prevented. If this set value is
exceeded for one minute, the output
frequency is reduced until the current falls to
that set in P083.The inverter can be made to
trip by using the relay in conjunction with
P074.
The maximum value that P086 can be set to
is automatically limited by the rating of the
inverter.
Motor PTC enable
0 -1
0]
0 = disabled
1 = enabled (inverter will trip F004 if
external PTC input goes high
impedance)
Automatic calibration
0 - 1
[1]
The motor stator resistance is used in the
inverter's internal current monitoring
calculations. When P088 is set to ‘1’ and the
RUN button is pressed, the inverter
performs an automatic measurement of
motor stator resistance; stores it in P089
and then resets P088 to ‘0’.
If the measured resistance is too high for
the size of inverter (e.g. motor not
connected or unusually small motor
connected), the inverter will trip (fault code
F188) and will leave P088 set to ‘1’. If this
happens, set P089 manually and then set
P088 to ‘0’.