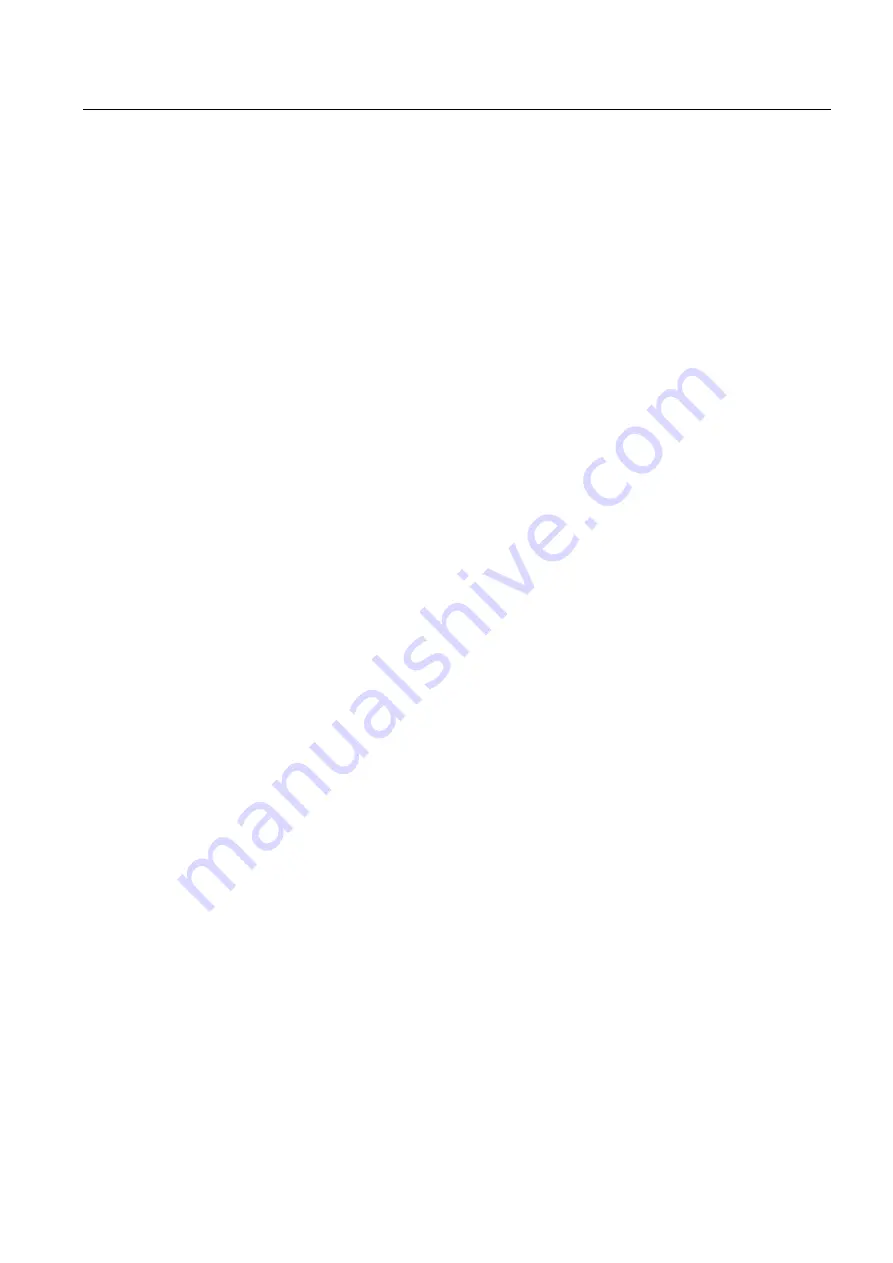
Commissioning
4.2 Commissioning preparations
OXYMAT 64
Operating Instructions, 06/2008, A5E00880383-03
37
4.2
Commissioning preparations
4.2.1
General information for commissioning
Operation
Before connecting and switching on the device, the operator must have made himself
familiar with the device operation.
Interfaces
Before use, the interfaces must be correctly allocated and parameterized.
Sample gas requirements
The sample gas must be free of dust, oil and condensation. Corrosive gases (e.g. HCl, Cl
2
,
SO
2
, …) or catalyzer poisons (e.g. H
2
S, HCN, CS
2
, ...) must not be connected, not even in
low concentrations.
Noise suppression
Noise in the measured signal can be reduced using function 50.
Pressure correction
The influence of the sample gas pressure is already corrected by the sensor electronics. A
special adjustment is not necessary. The pressure can be read using function 2.
Influence of interfering gases
Flammable gases influence the O
2
measurement in that they reduce the O
2
content of the
sample gas. The sensor temperature, the concentration of flammable components, as well
as the O
2
concentration and sample gas flow all have an effect.
The relationship between interfering gas concentration and O
2
offset is frequently non-linear.
Correction of cross-interference is only meaningful if the effect of the interfering gas is lower
than the expected O
2
concentration.
For examples of interfering gas offsets, refer to the chapter "Influence of interfering gas".
See also
Sample gas quality (Page 25)
Influence of interfering gas (Page 15)