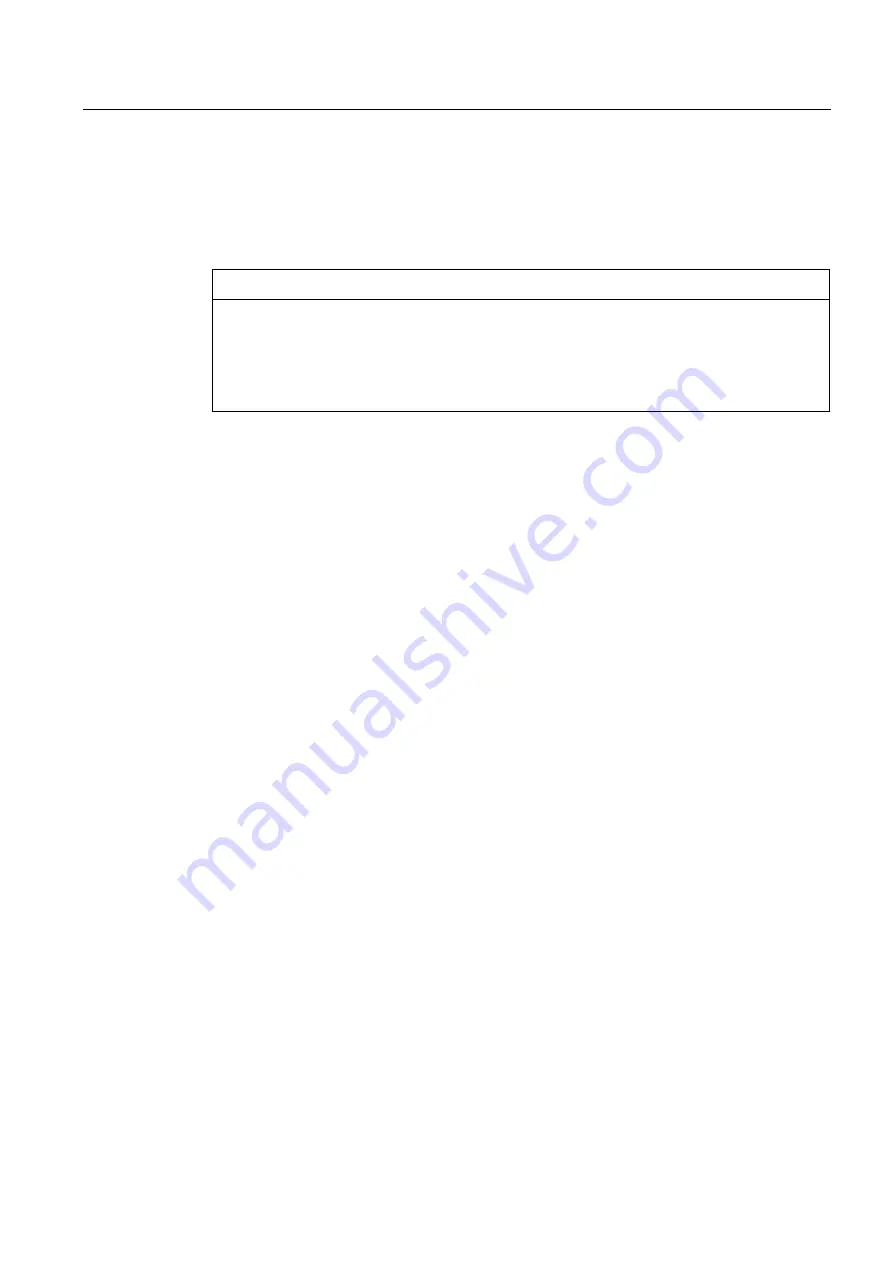
Installing and connecting
3.3 Gas connections and internal gas routing
OXYMAT 64
Operating Instructions, 06/2008, A5E00880383-03
25
3.3.2
Sample gas quality
NOTICE
Danger of defects resulting from insufficiently prepared sample gas
The sample gas connected to the device must be free of oil and dust, and must not contain
any corrosive components. Moisture must never penetrate the sample gas path, the sensor
would otherwise be damaged!
Therefore make sure that the sample gas is prepared appropriately!
No flammable gases above the lower explosive limit may be connected either, since these
could be released and produce an explosive atmosphere within the analyzer.
3.3.3
Pressure sensors
The OXYMAT 64 has an internal pressure sensor for correcting the influence of pressure on
the measured value. The pressure sensor is present on the sensor electronics, and
measures the sample gas pressure via the sample gas outlet pipe. The pressure sensor
need not be considered further in the device installation.
3.3.4
Gas flow
High-pressure version
The sample gas pressure (3000 to 6000 hPA) is regulated by the pressure regulator (4) at
approx. 2000 hPA, or is offered in the version without a pressure regulator by the operator at
2000 hPA. This pressure is applied at the restrictor (5). The restrictor (5) reduces the
pressure such that a sample gas flow of 15 to 30 l/h is created. This flow is divided via the
sample gas restrictor (6) and the adjustable bypass restrictor (10) such that there is a
sample gas flow of 7.5 l/h through the sensor. If the sample gas can flow off into the
atmosphere unhampered, the sample gas pressure corresponds to the ambient pressure. If
the sample gas flows off via an exhaust gas line, it works like a flow resistance.