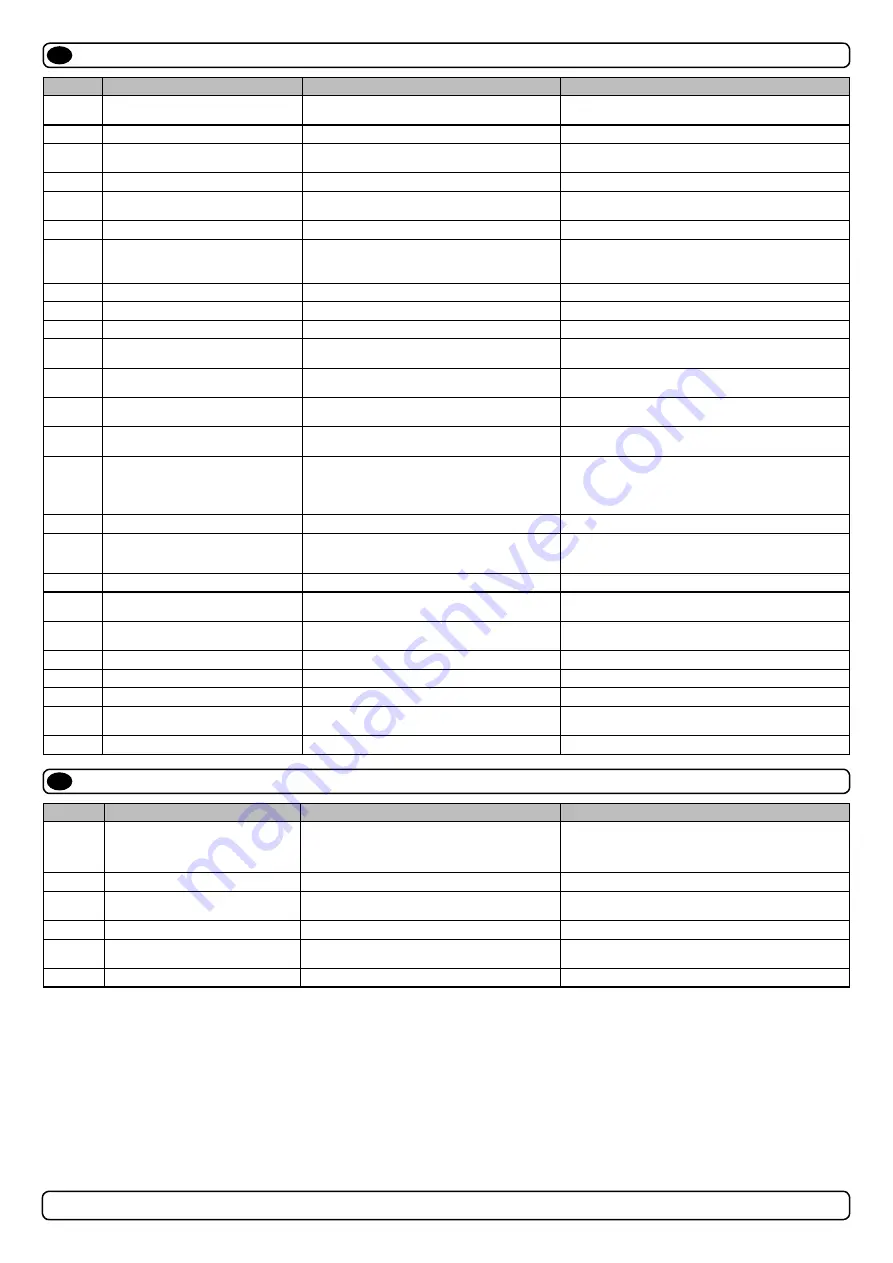
25
3059
10
2019
-
PJC 221 & 222
PHC-3 Alarm Descriptions
EN
MC_0117
Fault Code
Description
Cause
Action
10500.0.10
PHC Oil Level - Level Low
Hydraulic oil level is low
-Limit the use of thruster
-Inspect hydraulic oil level
-Check system for leaks and refi ll hydraulic oil
10500.0.13
PHC Oil Level - Open Circuit
Analog oil level sensor open circuit
-Sensor not connected or wire break.
-Verify sensor type in parameter 0201
-Disconnect sensor and measure that sensor resistance value is in
range 0-180ohm.
10501.0.11
PHC Oil Temp - Level High
Oil temperature higher than 75°C (167°F)
-Limit the use of thruster to prevent temperature to rise.
-Check if the cooling pump is running and there is cooling water fl ow.
-Inspect seawater fi lter
-Verify that cooling pump is enabled in parameter 0301
10501.0.13
PHC Oil Temp - Open Circuit
Analog oil temp sensor open circuit
-Sensor not connected or wire break.
- Disconnect sensor and measure that sensor resistance value is in
range 104ohm-147Kohm
-The wrong sensor is defi ned in parameter 0201
10501.0.16
PHC Oil Temp - Short Circuit
Analog oil temp input short circuit
-Input shorted to GND, check wiring/sensor
-Disconnect sensor and measure that sensor resistance value is in
range 104ohm-147Kohm
10502.0.13
PHC Stablizier Pressure - Open Circuit
Stabilizer pressure sensor open circuit
-Sensor not connected or wire break.
-System incorrectly confi gured with stabilizer, parameter 1001
-Replace sensor
10502.0.16
PHC Stablizier Pressure - Short Circuit
Stabilizer pressure sensor short circuit
-Wires shorted or sensor defective, check wiring/sensor
-Replace sensor
10502.0.19
PHC Stablizier Pressure - Under Limit
Stabilizer pressure has dropped below 20bar.
-Check accumulator charge pressure
-Check PTO pressure (if PTO powered)
-Check system for oil leaks
10502.0.20
PHC Stablizier Pressure - Over Limit
Stabilizer pressure is higher than:
set point + 30bar running from PTO
or set point + 15bar running from AC motor
-Check PTO pressure setting
-Check accumulator charge pressure
10502.0.26
PHC Stablizier Pressure - VALUE MAX
Stabilizer pressure reached sensor max value.
-Check that the correct sensor is fi tted
-Check that sensor range parameter 1010 match the sensor
-Check PTO pressure setting
10502.0.200 PHC Stablizier Pressure - Timeout
Stabilizer pressure has not reached 50% of setpoint parame-
ter 1003 after 30sec.
-Check the pump feed shutoff valve.
-Check PTO pressure (if PTO powered)
-Check system for oil leaks
10503.0.13
PHC System Pressure - Open Circuit
System pressure sensor open circuit
-Sensor not connected or wire break.
-Verify system pressure, parameter 0104
10503.0.16
PHC System Pressure - Short Circuit
System pressure sensor short circuit
-Wires shorted or sensor defective, check wiring/sensor
-Replace sensor
10504.0.13
PHC AI 1 - Open Circuit
Analog Input 1 (4-20mA) sensor open circuit
-Sensor not connected or wire break.
10504.0.16
PHC AI 1 - Short Circuit
Analog Input 1 (4-20mA) sensor short circuit
-Wires shorted or sensor defective, check wiring/sensor
-Replace sensor
10505.0.13
PHC AI 2 - Open Circuit
Analog Input 2 (4-20mA) sensor open circuit
-Sensor not connected or wire break.
10505.0.16
PHC AI 2 - Short Circuit
Analog Input 2 (4-20mA) sensor short circuit
-Wires shorted or sensor defective, check wiring/sensor
-Replace sensor
10508.0.13
PHC DOUT AC PUMP UNLOAD - Open Circuit AC Pump Unload valve open circuit
-Check for open circuit, power consumption < 5.0 Watt
-System incorrectly confi gured with stabilizer, parameter 1001
10508.0.51
PHC DOUT AC PUMP UNLOAD - Current High AC Pump Unload valve current higher than 4.0A
-Check wires and connections for short circuit
10509.0.13
PHC DOUT ACCUMULATOR DUMP - Open
Circuit
Accumulator Dump valve open circuit
-Check for open circuit, power < 5.0 Watt
-System incorrectly confi gured with stabilizer, parameter 1001
10509.0.51
PHC DOUT ACCUMULATOR DUMP - Current
High
Accumulator Dump valve current higher than 4.0A
-Check wires and connections for short circuit
10510.0.13
PHC DOUT STABILIZER - Open Circuit
Stabilizer valve open circuit
-Check for open circuit, power consumption < 5.0 Watt
-System incorrectly confi gured with stabilizer, parameter 1001
10510.0.51
PHC DOUT STABILIZER - Current High
Stabilizer valve current higher than 4.0A
-Check wires and connections for short circuit
10511.0.13
PHC DOUT COOLING PUMP HYDRAULIC -
Open Circuit
Hydraulic Cooling Pump valve open circuit
-Check for open circuit, power consumption < 5.0 Watt
-Wrong cooling pump confi gured, parameter 0301
10511.0.51
PHC DOUT COOLING PUMP HYDRAULIC -
Current High
Hydraulic Cooling Pump valve current higher than 4.0A
-Check wires and connections for short circuit
10512.0.13
PHC DOUT LS DUMP - Open Circuit
LS-Dump valve open circuit
-Check for open circuit, power consumption < 5.0 Watt
-System wrong confi gured with thrusters, parameter 2001 or 2101
10512.0.51
PHC DOUT LS DUMP - Current High
LS-Dump valve current higher than 4.0A
-Check wires and connections for short circuit
10513.0.51
PHC DOUT PUMP #2 - Current High
Pump #2 valve current higher than 4.0A
-Check wires and connections for short circuit
10514.0.13
PHC DOUT 5 - Open Circuit
Digital Output 5 is confi gured as crossover and output is open
circuit
-Check for open circuit, power consumption < 5.0 Watt
-Output confi gured wrong, parameter 0505
10514.0.51
PHC DOUT 5 - Current High
Digital Output 5 current higher than 4.0A
-Check wires and connections for short circuit
10515.0.13
PHC DOUT 6 - Open Circuit
Digital Output 6 is confi gured as crossover and output is open
circuit
-Check for open circuit, power consumption < 5.0 Watt
-Output confi gured wrong, parameter 0506
10515.0.51
PHC DOUT 6 - Current High
Digital Output 6 current higher than 4.0A
-Check wires and connections for short circuit
10516.0.13
PHC DOUT 3 - Open Circuit
Digital Output 3 is confi gured as crossover and output is open
circuit
-Check for open circuit, power consumption < 5.0 Watt
-Output confi gured wrong, parameter 0503
10516.0.51
PHC DOUT 3 - Current High
Digital Output 3 current higher than 4.0A
-Check wires and connections for short circuit
PHC-3 Alarm Descriptions
EN
MC_0117
Fault Code
Description
Cause
Action
10517.0.13
PHC DOUT 2 - Open Circuit
Digital Output 2 is confi gured as crossover and output is open
circuit
-Check for open circuit, power consumption < 5.0 Watt
-Output confi gured wrong, parameter 0502
10517.0.51
PHC DOUT 2 - Current High
Digital Output 2 current higher than 4.0A
-Check wires and connections for short circuit
10518.0.13
PHC DOUT 1 - Open Circuit
Digital Output 1 is confi gured as crossover and output is open
circuit
-Check for open circuit, power consumption < 5.0 Watt
-Output confi gured wrong, parameter 0501
10518.0.51
PHC DOUT 1 - Current High
Digital Output 1 current higher than 4.0A
-Check wires and connections for short circuit
10519.0.13
PHC DOUT 4 - Open Circuit
Digital Output 4 is confi gured as crossover and output is open
circuit
-Check for open circuit, power consumption < 5.0 Watt
-Output confi gured wrong, parameter 0504
10519.0.51
PHC DOUT 4 - Current High
Digital Output 4 current higher than 4.0A
-Check wires and connections for short circuit
10520.0.51
PHC ECI PUMP POWER FEED - Current High
ECI cooling pump power current higher than 8.0A
-Check pump cable for damage and short circuits
-Make sure the connector on the cooling pump is correctly inserted.
-Replace cooling pump
10521.0.51
PHC Bow Thruster Power - Current High
Bow thruster PVG feed current higher than 3.0A
-Check PVG wires and connections for short circuit
10522.0.51
PHC Stern Thruster Power - Current High
Stern thruster PVG feed current higher than 3.0A
-Check PVG wires and connections for short circuit
10523.0.51
PHC Thruster Power - Current High
Bow or Stern PVG feed current higher than 3.3A
Check all bow and stern PVG signal wires for short circuits
10524.0.51
PHC ECI Cooling Pump - Current High
ECI cooling pump current higher than 13.0A
-Check ECI cooling pump cable for damage and short circuits
-Replace ECI cooling pump
10524.0.53
PHC ECI Cooling Pump - Overvoltage
ECI cooling pump overvoltage, voltage higher than 33.0V
-Check PHC-3 input voltage is below 33.0V
-Replace ECI cooling pump
10524.0.54
PHC ECI Cooling Pump - Undervoltage
ECI cooling pump under voltage, voltage is lower than 18.0V
-Check PHC-3 input voltage is higher than 18.0V
-Replace ECI cooling pump
10524.0.55
PHC ECI Cooling Pump - Overtemp
ECI cooling pump temperature higher than 100°C (212°F)
-Check ECI cooling pump for damages
-Replace ECI cooling pump
10524.0.100 PHC ECI Cooling Pump - No Communication
No communication with ECI cooling pump
-Check if ECI pump is connected
-Check wires to ECI pump for open circuits
-Check power supply cooling pump
-Wrong cooling pump confi gured, parameter 0301
10524.0.205 PHC ECI Cooling Pump - HW FAULT
ECI cooling pump hardware fault
-Replace ECI cooling pump
10526.0.0
PHC ECI Cooling Pump Blocked - -
ECI cooling pump is blocked
-Reset fault and if fault reappears, cooling pump need service or
replacement.
-Check pump inlet for obstacles
10527.1.0
PHC VFD Not Ready Instance 1 -
VFD not ready
-VFD external run enable/power available signal is lost.
10528.1.10
PHC VFD ABB Parameter Instance 1 Level Low ABB ACS550 parameter values 2001 or 2002 cannot be a
negative value.
-Check ABB ACS550 parameter 2001 and 2002.
10529.0.19
PHC ECI Cooling Pump Speed - Under Limit
ECI pump motor speed under limit, below 100rpm
-Check hose for dirt
-Check pump inlet for obstacles
10530.0.201 PHC PTO ENGINE INSTANCE - INIT FAIL
Parameter 1011-PTO ENGINE INSTANCE is not defi ned
-Set parameter 1011-PTO ENGINE INSTANCE
36000.1.24
ABB ACS550 Instance 1 Fault
ABB ACS550 fault
See ABB ACS550 drive for more details
36002.1.24
VACON Instance 1 Fault
VACON VFD Fault
See VACON drive for more details
36100.1.100 VFD Instance 1 No Communication
Lost communication with VFD
-VFD not powered up
-VFD communication cable not connected or incorrectly wired
36103.1.0
VFD IN LOCAL Instance 1 -
VFD in local mode
-Switch VFD to remote mode
PDC-301 Alarm Descriptions
EN
MC_0119
Fault Code
Description
Cause
Action
10600.0.208
SR150000 Fault - INTERLOCK
Retract Interlock
-Check if retract is depoyed.
-No communication with Retract Controller, check Retract Controller
has power.
-Check PDC-301 and Restract Controller setup.
36100.1.24
VFD Instance 1 Fault
VFD faulted
-See VFD for more information
36100.1.100 VFD Instance 1 No Communication
PDC-301 has no MODBUS communication with VFD.
-Check communication cable with VFD
-Check if VFD has power
36101.1.200 VFD PMS Instance 1 Timeout
VFD is not ready within 60 after power reqest.
-Check if VFD has power
36101.1.204 VFD PMS Instance 1 SIGNAL LOST
Lost Power Management signal from VFD, VFD not avilable
anymore.
-Check VFD for more information.
36103.1.0
VFD IN LOCAL Instance 1 -
VFD in Local or Hand Mode
-Change mode in VFD panel.