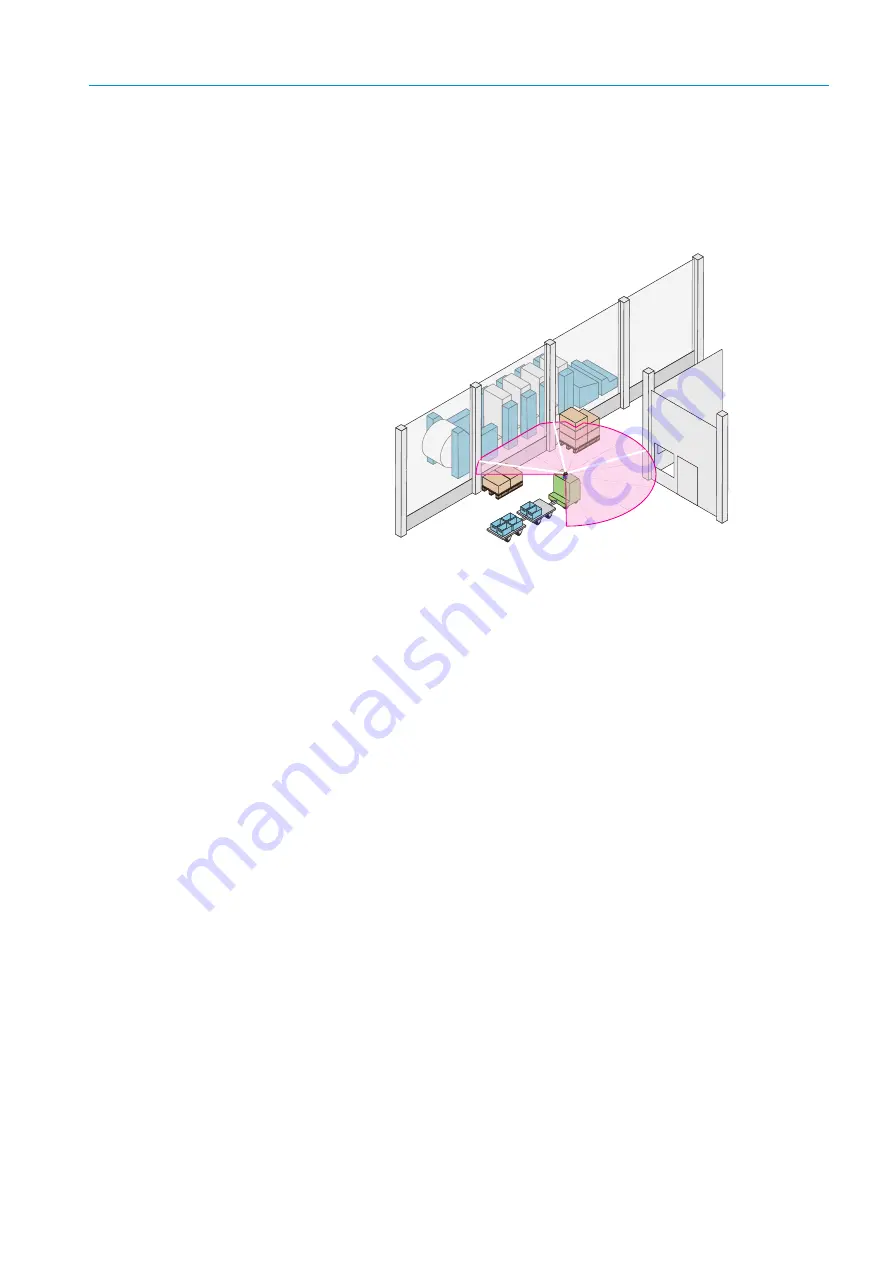
17
8024592/2019-08| SICK
O P E R A T I N G I N S T R U C T I O N S | NAV210
Subject to change without notice
PRODUCT DESCRIPTION
3
3.4
Operating principle of the NAV210
The NAV210 has an opto-electronic laser scanner that uses laser beams to scan the
outline of its surroundings on a plane without contact. The NAV210 measures its
surroundings in two-dimensional polar coordinates. If a measuring beam strikes an object,
the position of that object is determined in terms of distance, direction, and remission.
Fig. 4: Measurement principle of the NAV210
The NAV210 calculates the distance from the object using the elapsed time that the light
requires between sending and receiving the reflection in the sensor.
The scanning sector is 270°. The scanner head rotates with a frequency of 25 Hz.
A laser pulse and thus a distance measurement is triggered continuously after each angle
increment of 0.25°.