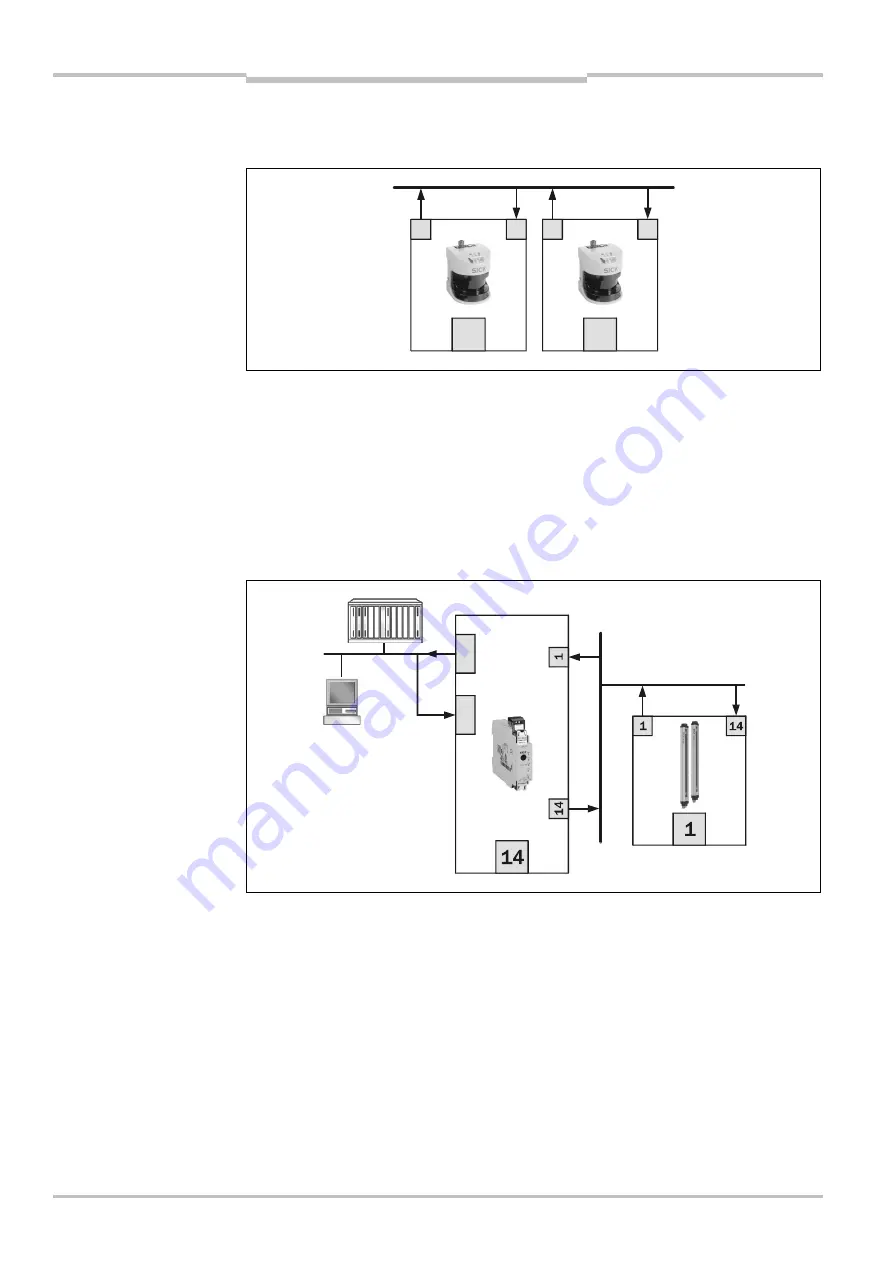
Chapter
4
Technical information
EFI
14
© SICK AG • Industrial Safety Systems • Germany • All rights reserved
8012622/Z098/2016-11-07
Subject to change without notice
Technical realization
4.1
Data exchange via EFI
To enable data to be exchanged via EFI, each device connected has a unique address.
7
8
7
8
8
7
In the example the S3000 Host has the address 7, the S3000 Guest the address 8. The
host receives via address 8 the status information on the OSSDs and the diagnostics
messages from the guest on contamination. The guest however receives the incremental
encoder values from the host over the address 7.
The safety controllers receive via these addresses status information on the
electrosensitive protective devices (C4000, S3000 etc.) or they control functions on the
ESPE via these addresses (muting, operating mode switching etc.).
If an EFI system is connected via an EFI gateway to a PROFINET IO, these data can be
forwarded to an (F)PLC or control tasks performed by the (F)PLC.
In the example the (F)PLC can write data to the M4000 via the routing in the EFI gateway
(address 14). I.e. muting signals can be simulated by the control system. Conversely,
status information including the output information from the M4000 (address 1) can be
transferred to the (F)PLC via the routing in the EFI gateway.
Fig. 11: Example data
exchange between two
S3000
Fig. 12: Example data
exchange between an (F)PLC
and an M4000 via an EFI
gateway