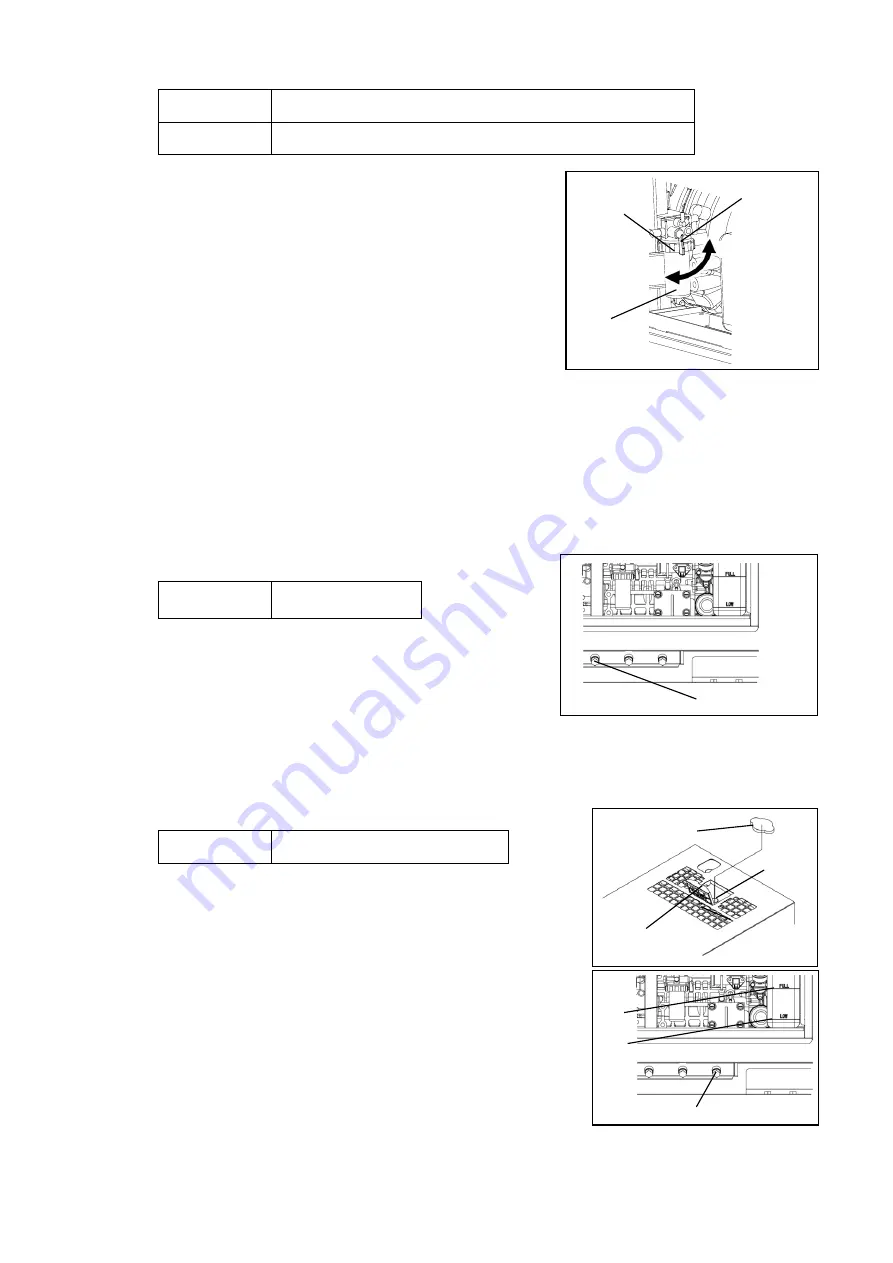
38
(4) Fuel Strainer Cleaning/Replacement
Cleaning
1st time: 50 hours
2nd time and after: Every 100 hours
Replacement
Every 400 hours
1)
Place a container under Fuel Filter to catch fuel spilling
out of the filter.
2)
Turn the fuel valve to "CLOSE".
3)
Turn the retainer ring counter clockwise and remove
the cup and element.
4)
Remove any water or foreign material from the cup
and clean the element using compressed air.
(
Or replace the element.
)
5)
Install in the reverse order of removal.
<Note>
Check that no foreign material is adhering to the packing then install the cup.
After installation, turn the fuel valve to "OPEN" and check that there is no fuel leakage.
After checking, turn the fuel valve to "CLOSE".
Element part no.: 16271-43561 (Kubota part no.)
Always be sure to wipe away any spilled fuel.
If water gather
s in the cup, drain water from the fuel tank. (Refer to section “10,
Inspection/Maintenance (5) Draining Water from the Fuel Tank”)
(5) Draining Water from the Fuel Tank
Draining
Water
Every 200 hours
1)
Set a container to catch spilled water.
2)
Remove the fuel drain plug and packing.
3)
Drain the water and tighten the fuel drain plug.
<Note>
Replace the packing with a new part each time you drain the water.
Packing part no.: 6C090-58961 (Kubota part no.)
Always be sure to check that there is no fuel leakage after tightening the fuel drain plug.
(6) Coolant Replacement
Change
Every 2,000 hours or 2 years
Coolant Total Capacity: Approximately 4 L
(Including the sub tank capacity of approx. 0.6 L)
1)
Set a container to catch spilled coolant.
2)
Open the top plate.
3)
Remove the radiator cap.
4)
Remove the water drain plug and packing.
5)
After the coolant has been drained, reinsert the coolant drain
plug with new packing.
6)
Remove the sub-tank and empty the coolant from the
sub tank.
7)
Reattach the sub-tank to its original position and fill with
coolant until it reaches the FULL level.
8)
Fill the radiator with coolant until it reaches the filler neck.
9)
Re-attach and tighten the radiator cap.
10)
Close the top plate.
Retainer
Ring
Element
Close
Open
Fuel
Valve
Radiator Cap
Water
Inlet
Top Plate
Fuel Drain Plug
Water Drain Plug
Full
Low
Summary of Contents for DG15BMK
Page 2: ......
Page 11: ...6 LABEL REPRODUCTION X564 000640 X564 000620 X505 000240 X505 006420 X505 006410...
Page 12: ...7 M707 000260 X564 000630 X564 000610 X505 004890 X505 006430 X564 000650...
Page 48: ...43 13 Engine Wiring Diagram...
Page 49: ...44 14 Generator Wiring Diagram...
Page 50: ......
Page 51: ......