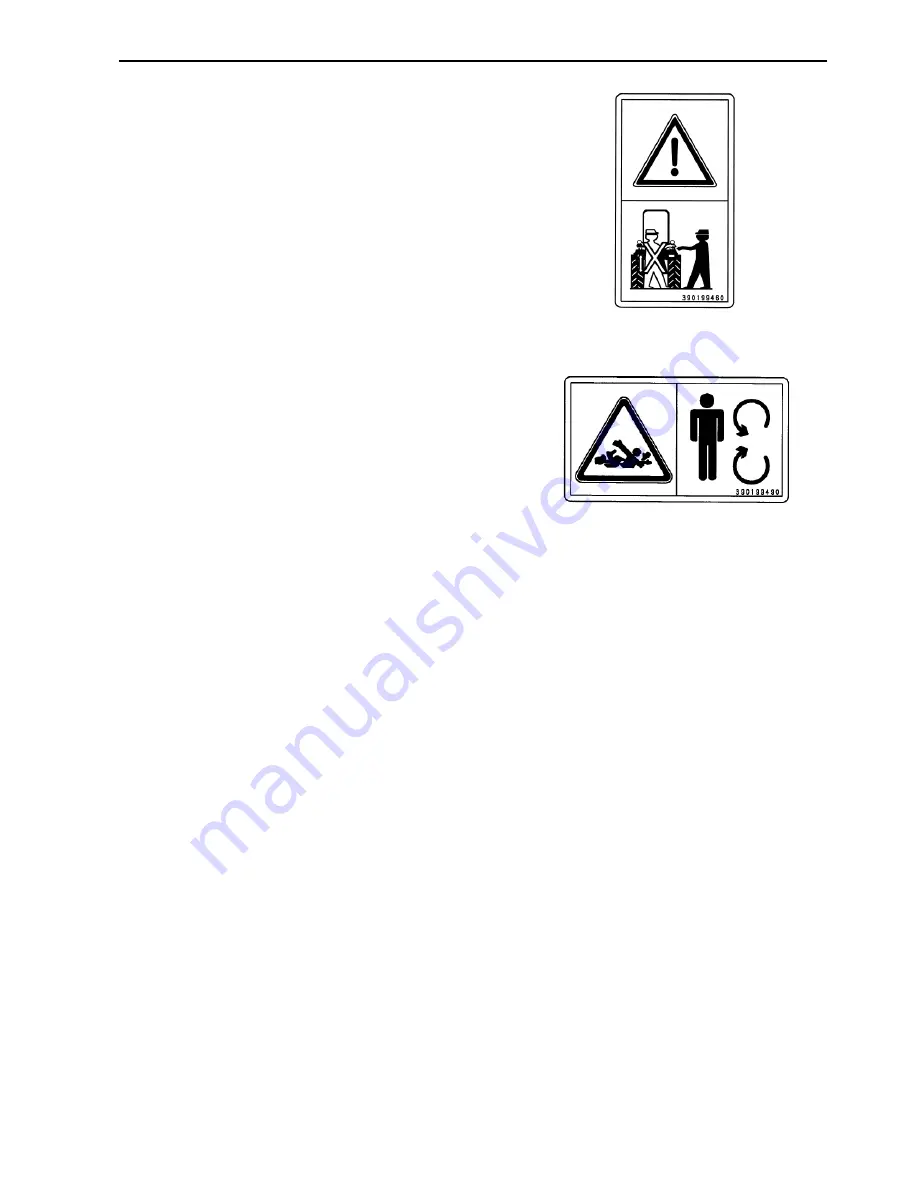
1-17
16. Location: Right hand side ROPS
.
WARNIMG:
To avoid injury, do not stand on
the implement or between the implement and
tractor while operating the HPL lift or PTO
controls. Always operate the HPL lift or PTO
controls from operator seat.
Part No. 390199460
17. Location: PTO Guard
.
WARNIMG:
To avoid injury, DO NOT clean,
adjust, unclog, or service the PTO driven
equipment when the tractor engine is running
or all movement components have not
completely stopped. Ensure that the PTO is
switched off.
Part No. 390199490
Summary of Contents for ST460
Page 1: ...ST460 OPERATOR S MANUAL MODEL...
Page 67: ...SECTION 2 OPERATION 2 42...
Page 103: ...SECTION 3 LUBRICATION AND MAINTENANCE 3 36...
Page 104: ...SECTION 3 LUBRICATION AND MAINTENANCE 3 37...
Page 112: ...SECTION 4 SPECIFICATIONS 4 7...
Page 114: ...SECTION 4 SPECIFICATIONS 4 9 3 5 4 4 7 1 2 6...
Page 119: ...SECTION 4 SPECIFICATIONS 4 14...
Page 121: ...SECTION 4 SPECIFICATIONS 4 16...
Page 123: ...SECTION 4 SPECIFICATIONS 4 18...
Page 124: ...SECTION 4 SPECIFICATIONS 4 19 NOTES...
Page 125: ...SECTION 4 SPECIFICATIONS 4 20...