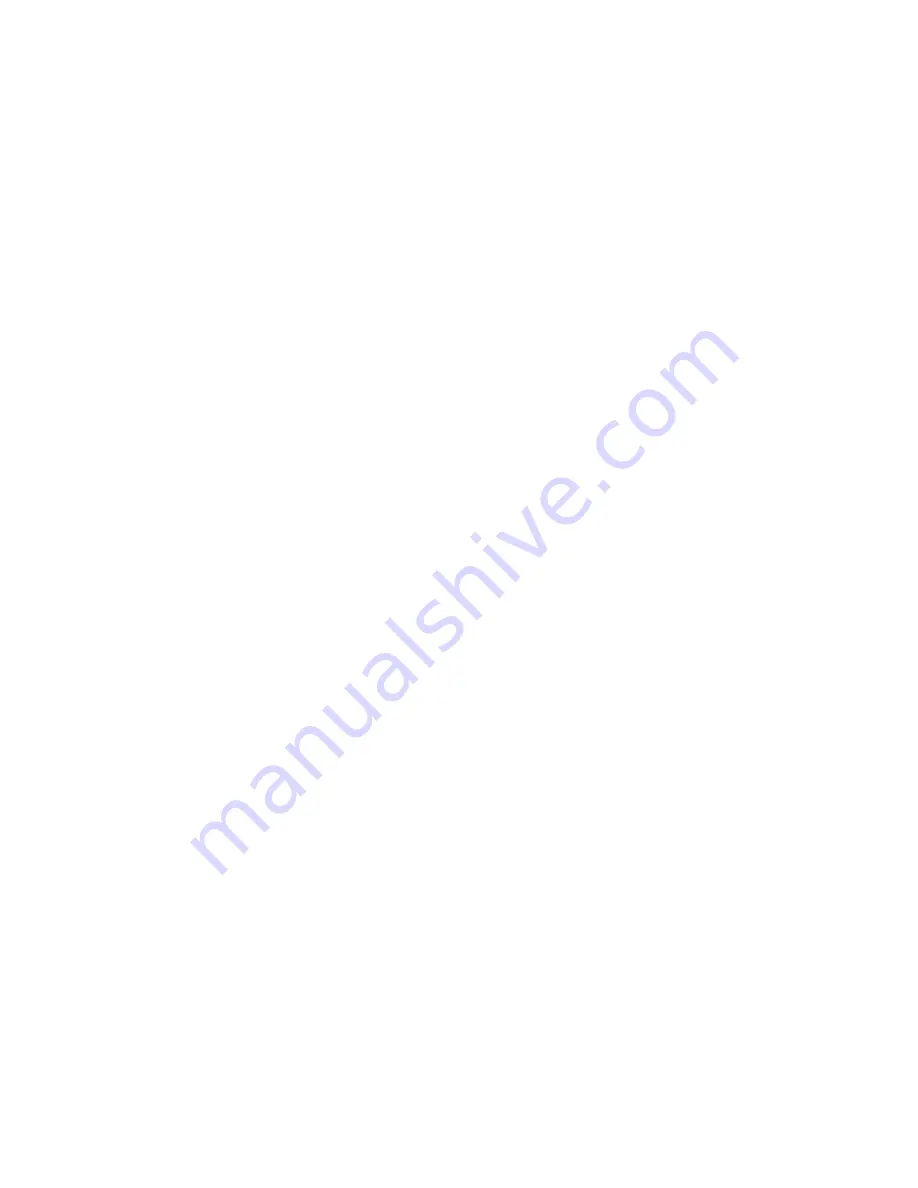
Troubleshooting
NOTE
: Refer to the Service Parts section of
this manual for a photo and description of all
the parts.
Problem:
Drive ram (A1) will not move or
slide freely on main carriage
channel (B1).
Possible Cause/Solution(s):
1
.
Guide blocks (A2) lack lubricant. Lubricate
with clean engine oil.
2
.
Guide blocks (A2) are installed incorrectly.
Refer to Service Information section
assembly procedures for correct
orientation.
3
.
Incorrect clearance between main carriage
channel (B1) and drive ram (A1) I-beam.
Refer to Service Information section for
clearance specifications.
4
.
Hydraulic drive cylinder assembly (C1) is
not parallel to main carriage channel (B1).
Refer to Service Information section,
hydraulic drive cylinder installation, and
parallelism adjustment.
5
.
Main carriage channel (B1) or drive ram
(A1) is bent or damaged. Discontinue use
and order replacement parts.
Problem:
Poor performance, low or no
impact, hydraulic drive cylinder will
not extend.
Possible Cause/Solution(s):
1
.
Weak or broken drive ram springs (C14).
2
2
.
.
Broken upper spring bracket (A11).
3
.
Bent or damaged hydraulic drive cylinder
assembly (C1).
4
.
Main carriage channel (B1) is binding.
5
.
Restricted or plugged hydraulic hose(s)
(G15, G17, G20).
6
.
Low or no hydraulic pressure or flow from
the machine or power source.
Problem:
Rubber bumpers (B3) have
premature or excessive damage.
Possible Cause/Solution(s):
1
.
Post Driver is not properly adjusted prior to
operation and drive ram guide blocks (A2)
are contacting rubber bumpers (B3).
Storage
For the best results, always store equipment in
a dry, protected location. Leaving equipment
unprotected will shorten the service life of the
Post Driver.
1
.
Before storing, remove debris and clean
the entire unit using compressed air or a
pressure washer.
2
.
Inspect the Shaver Post Driver. Replace
any worn or damaged parts before using
the Post Driver again.
• Check all bolted connections. Ensure
that fasteners are tight, and all pins are
secured in place.
• Inspect the frame for structural fractures.
• Make sure all warning decals are in place
and legible.
• Make sure the rubber debris guard is in
place and in good condition.
• Check the hydraulic cylinder(s) for signs
of seal damage or excessive wear.
• Inspect all hydraulic hoses and fittings for
leaks or signs of wear.
3
.
After cleaning, lightly lubricate the guide
blocks with clean engine oil. Do not apply
grease, as this will retain grit and cause
excessive wear.
4
.
Clean and lubricate the hydraulic control
valve safety stop linkage. Make sure the
return spring and cotter pins are in good
condition.
5
.
Apply a light coating of clean grease to all
exposed hydraulic cylinder shafts to help
prevent rust.
29
Summary of Contents for HD-12-H
Page 44: ...44 Service Parts 44 Driver Assembly ...
Page 46: ...46 Hydraulic Base Plate Assembly ...
Page 55: ...Notes 55 ...