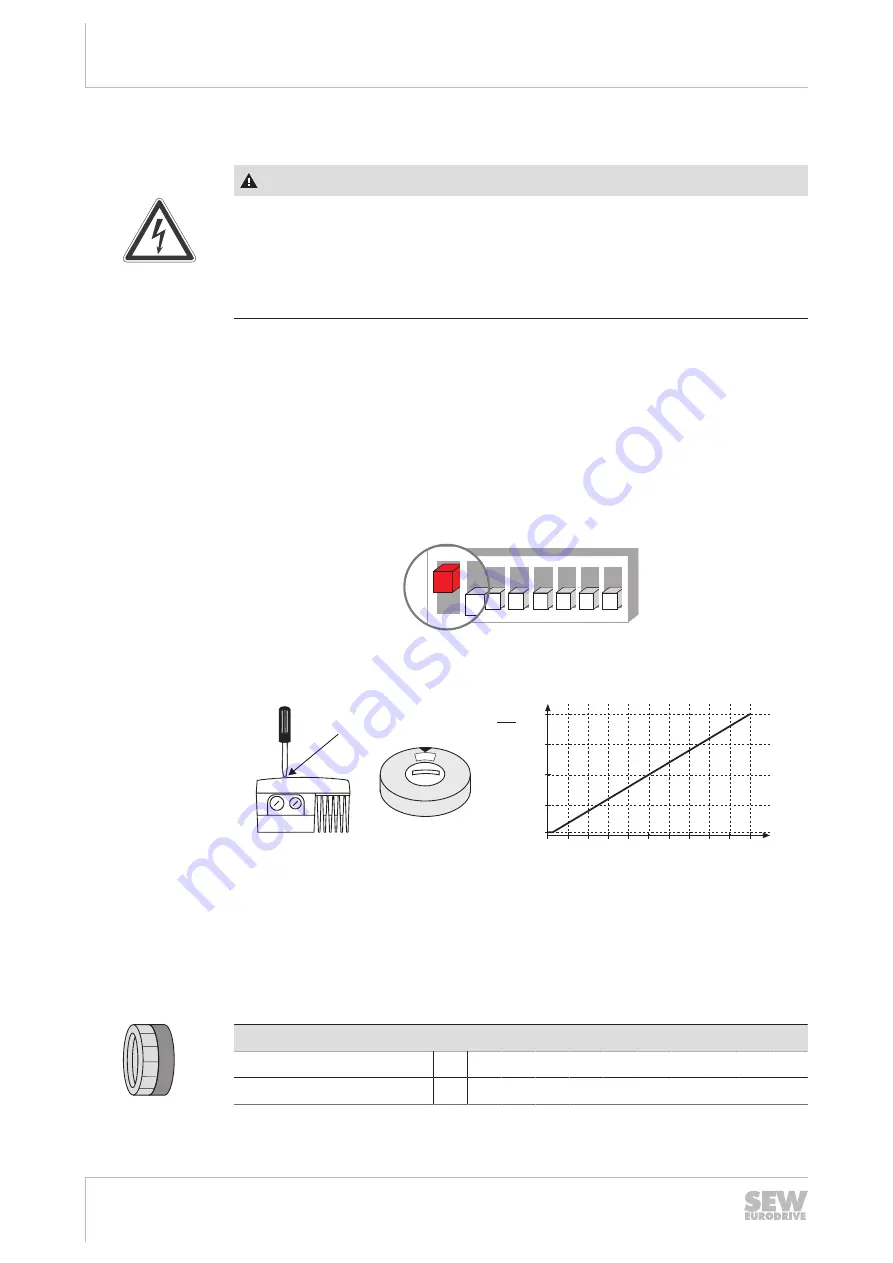
6
Startup of MOVIMOT
®
with MLK.. in Easy mode
Startup procedure
Compact Operating Instructions – MOVIMOT
®
MM..D with AS-Interface
56
6.7
Startup procedure
WARNING
Electric shock from capacitors that have not been fully discharged.
Severe or fatal injuries.
•
Disconnect the inverter from the power. Observe the minimum switch-off time
after disconnection from the supply system:
–
1 minute
1. Remove the MOVIMOT
®
inverter from the connection box.
2. Set the required AS-Interface address:
ð
with a hand-held programming device (→
ð
or with a master (see description of the AS-Interface master)
3. Check the connection of the MOVIMOT
®
inverter.
ð
See chapter "Electrical Installation".
4. Set the type of 24 V supply via the switch S5 (→
5. Set DIP switches S1/1 – S1/4 as follows:
1
ON
6
7
8
5
4
3
2
1
ON
2
9007199592524939
6. Set the first speed at the setpoint potentiometer f1 (active when the AS-Interface
bit DO2 = "0"). Factory setting: approx. 50 Hz (1500 min
-1
)
100
[1]
2
1
0
2 3 4 5 6 7 8 9 10
75
25
50
6
5
f1
f1
Hz
27021598093635979
[1]
Potentiometer setting
7.
NOTICE!
Loss of warranted degree of protection if the screw plugs of the f1 set-
point potentiometer or the X50 diagnostic interface are installed incorrectly or not
at all. Damage to the MOVIMOT
®
inverter.
Make sure the screw plug of the setpoint potentiometer has a seal and screw it in.
8. Set the second speed at switch f2 (active if AS-Interface bit DO2 = "1" ).
3
4
5
6
7
8
Switch f2
Detent setting
0
1
2
3
4
5
6
7
8
9
10
Setpoint f2 [Hz]
5
7
10
15
20
25
35
50
60
70 100
27792307/EN – 07/2022