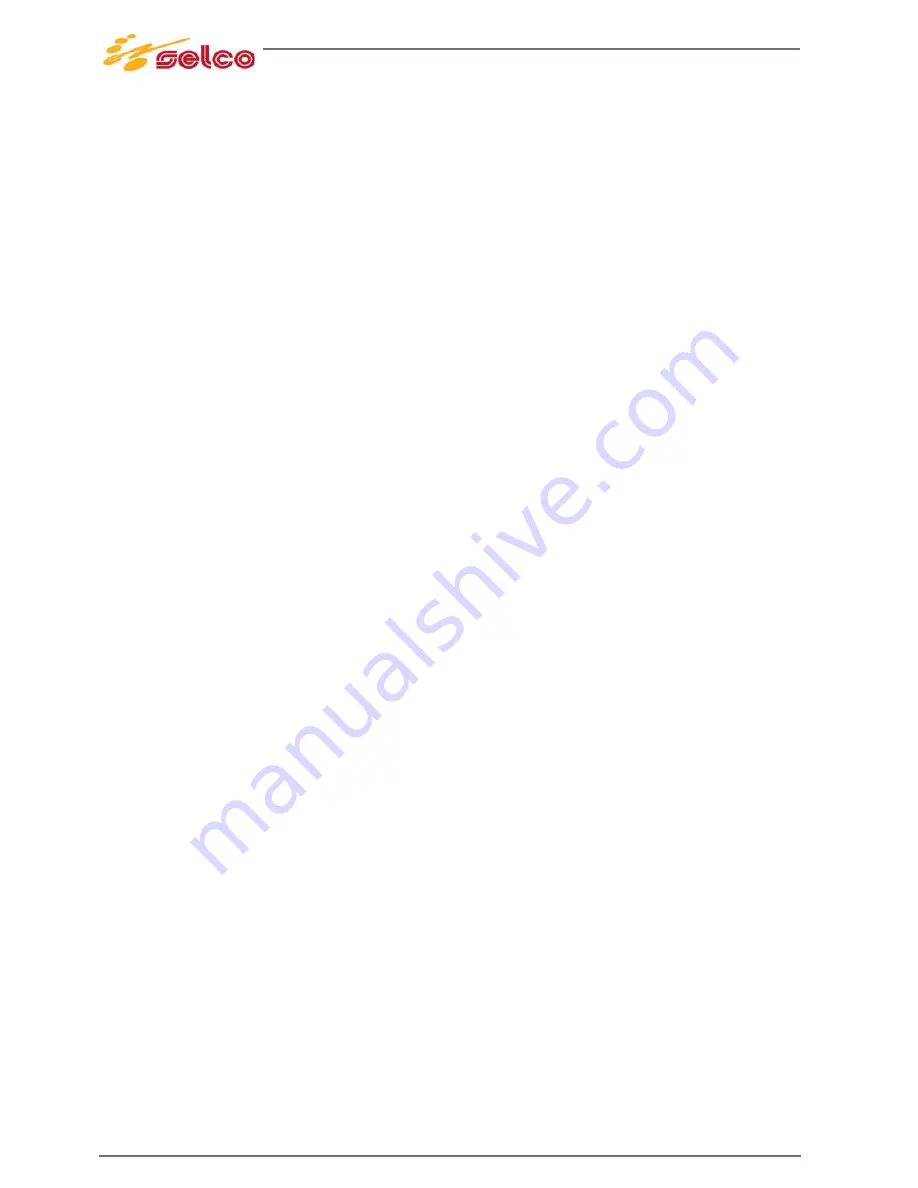
60
Cause
Incorrect welding/cutting mode.
Solution Decrease the distance between the electrode and
the piece.
Move regularly during all the welding/cutting oper-
ations.
Tungsten inclusions
Cause
Incorrect welding parameters.
Solution
Decrease the welding voltage.
Use a bigger diameter electrode.
Cause Incorrect
electrode.
Solution
Always use quality materials and products.
Sharpen the electrode carefully.
Cause
Incorrect welding mode.
Solution
Avoid contact between the electrode and the weld
pool.
Blowholes
Cause
Insufficient shielding gas.
Solution
Adjust the gas flow.
Check that the diffuser and the gas nozzle of the
torch are in good condition.
Sticking
Cause
Incorrect arc length.
Solution Increase the distance between the electrode and
the piece.
Increase the welding voltage.
Cause
Incorrect welding/cutting parameters.
Solution
Increase the welding/cutting current.
Cause
Incorrect welding mode.
Solution
Angle the torch more.
Cause
Pieces to be welded/cut too big.
Solution
Increase the welding/cutting current.
Increase the welding voltage.
Cause
Incorrect arc regulation.
Solution
Increase the equivalent circuit inductive value setting.
Undercuts
Cause
Incorrect welding parameters.
Solution
Decrease the welding voltage.
Use a smaller diameter electrode.
Cause
Incorrect arc length.
Solution Increase the distance between the electrode and
the piece.
Increase the welding voltage.
Cause
Incorrect welding mode.
Solution
Decrease the side oscillation speed while filling.
Decrease the travel speed while welding.
Cause
Insufficient shielding gas.
Solution
Use gases suitable for the materials to be welded.
Oxidations
Cause
Insufficient gas protection.
Solution
Adjust the gas flow.
Check that the diffuser and the gas nozzle of the
torch are in good condition.
Porosity
Cause
Grease, varnish, rust or dirt on the workpieces to be
welded/cut.
Solution
Clean the workpieces carefully before welding.
Cause
Grease, varnish, rust or dirt on the filler material.
Solution
Always use quality materials and products.
Keep the filler metal always in perfect condition.
Cause
Humidity in the filler metal.
Solution
Always use quality materials and products.
Keep the filler metal always in perfect condition.
Cause
Incorrect arc length.
Solution Decrease the distance between the electrode and
the piece.
Decrease the welding voltage.
Cause
Humidity in the welding/cutting gas.
Solution
Always use quality materials and products.
Ensure the gas supply system is always in perfect
condition.
Cause
Insufficient shielding gas.
Solution
Adjust the gas flow.
Check that the diffuser and the gas nozzle of the
torch are in good condition.
Cause
The weld pool solidifies too quickly.
Solution
Decrease the travel speed while welding/cutting.
Pre-heat the workpieces to be welded/cut.
Increase the welding/cutting current.
Hot cracks
Cause
Incorrect welding/cutting parameters.
Solution
Decrease the welding/cutting voltage.
Use a smaller diameter electrode.
Cause
Grease, varnish, rust or dirt on the workpieces to be
welded/cut.
Solution
Clean the workpieces carefully before welding/cut-
ting.
Cause
Grease, varnish, rust or dirt on the filler metal.
Solution
Always use quality materials and products.
Keep the filler metal always in perfect condition.
Cause
Incorrect welding/cutting mode.
Solution
Carry out the correct sequence of operations for
the type of joint to be welded/cut.
Cause
Pieces to be welded have different characteristics.
Solution
Carry out buttering before welding.
Cold cracks
Cause
Humidity in the filler metal.
Solution
Always use quality materials and products.
Keep the filler metal always in perfect condition.
Cause
Particular geometry of the joint to be welded/cut.
Solution
Pre-heat the pieces to be welded/cut.
Carry out post-heating.
Carry out the correct sequence of operations for
the type of joint to be welded/cut.
For any doubts and/or problems do not hesitate to contact
your nearest customer service centre.
Summary of Contents for Genesis 2200 PMC
Page 1: ...Genesis 2200 PMC MANUALE DI RIPARAZIONE REPAIR MANUAL...
Page 38: ...74...
Page 41: ...77 16 SCHEMI ELETTRICI E DI COLLEGAMENTO WIRING DIAGRAMS AND CONNECTION...
Page 42: ...78 17 CONNETTORI CONNECTORS...
Page 43: ...79...
Page 44: ...80 18 LISTA RICAMBI SPARE PARTS LIST 55 05 010 GENESIS 2200 PMC 1x230V...
Page 47: ...83...
Page 48: ...84 07 01 600 SL 4R 4T 11A 11B 11C 22...
Page 50: ...86 19 INSTALLAZIONE KIT ACCESSORI INSTALLATION KIT ACCESSORIES 73 11 014 Kit Push Pull...
Page 51: ...87...
Page 52: ...88 STANDARD U D VERSION OPTIONAL PUSH PULL VERSION...
Page 53: ...89...
Page 54: ...90 MODULO RICAMBI...