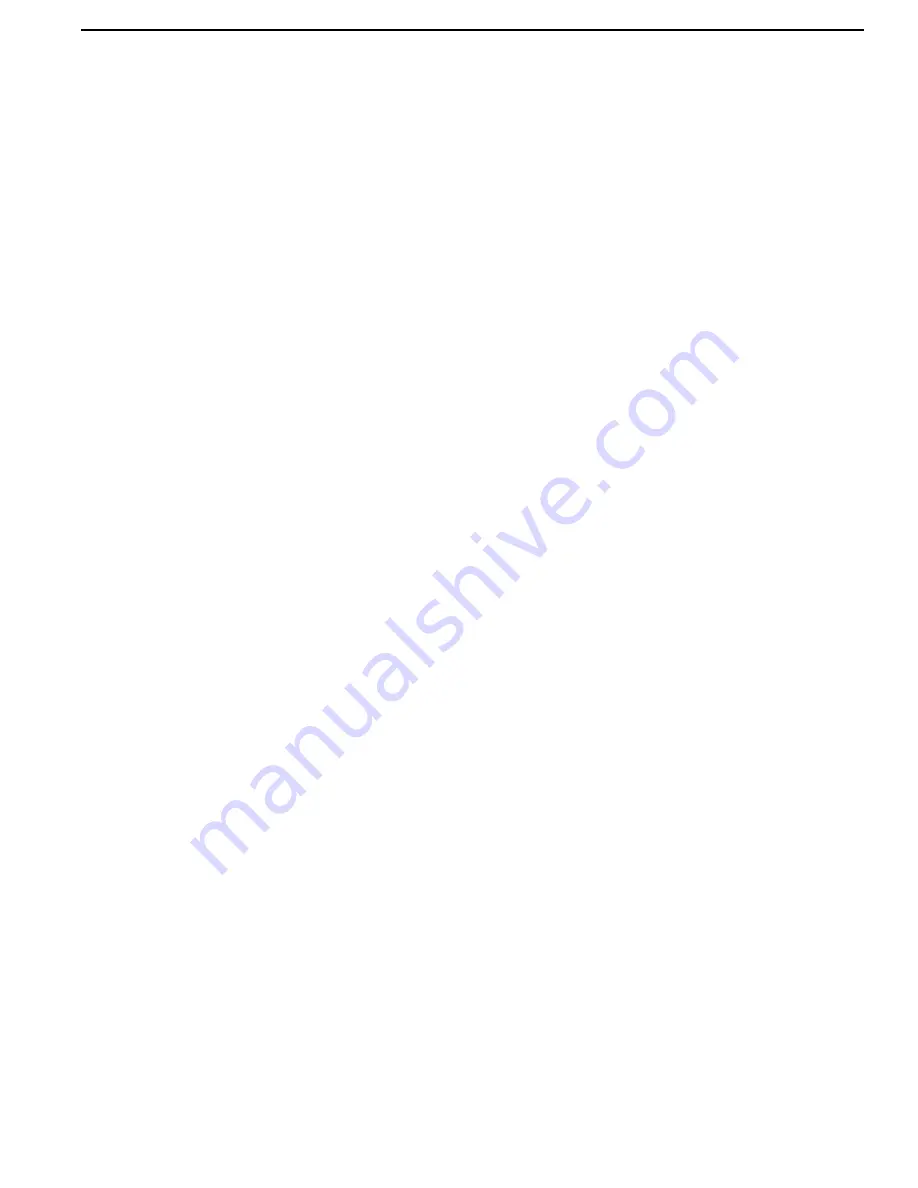
b. Check the capacitor on the motor, and replace it if it has shorted out.
c. Measure motor voltage during attempt to start it. If voltage drops more than 10%, locate and correct the
reason.
d. Check the motor starter relay (contactor) for “burnt” contacts.
2. The 3-Phase (230/380/460 VAC) Electric Motor “hums,” pulls starting current (locked rotor) amperage, does
not rotate, and trips the supply power circuit breaker when attempting to operate the System. The 3-Phase
Electric Motor requires all three power lines (all three phases) to operate, otherwise it will revert to “single phase”
(resulting in extensive damage to the motor’s internal windings). Note that low voltage will also cause the same
symptom.
a. Same troubleshooting steps as that for the Single Phase (115 or 230VAC) Electric Motor, above.
3. The Electric Motor makes an unusual “grinding” sound when operated.
a. Check and replace the front and rear bearings, as necessary.
b. Check if the fan is rubbing against the fan guard.
Booster Pump
Replace ceramic seal approximately every 2000 hours, or at the sign of leakage.
Disassembly
Remove the four 3/8-16 bolts holding the volute to the motor bracket. To remove the impeller, remove the bearing
cap on the motor to expose the screwdriver slot on the motor shaft. Hold the motor shaft with a large screwdriver
and remove the impeller by grasping it and turning the impeller counter clockwise. Remove the seal. Two
screwdrivers wedged into the seal at 180° apart serve as tools to wedge the seal out. The ceramic seat is removed
by removing the end-bell gasket.
Reassembly
Clean the motor shaft and the bracket of any corrosion or salt deposits. Replace the end bell gasket and the tap
seat portion into the bracket cavity. Use a new gasket. Place the ceramic seat into the cavity over the shaft. Make
sure that the polished side is toward the end of the shaft. Tap into place evenly using a hollow piece of wood or
plastic tool. If a metal tool is used to tap into place, protect the seat with cardboard or a clean cloth. Lubricate the
shaft with water and soap or a light oil and slip the rotating portion of the seal over the shaft with the carbon element
toward the ceramic. Slide it down onto the shaft as far as possible. Apply blue Loctite to the motor shaft threads.
Hold the motor shaft and reinstall the impeller. Tighten the impeller by turning it clockwise until it is snug. Reinstall
the volute. Tighten the bolts evenly. Thoroughly prime the pump.
Some Electric Motors supplied by Sea Recovery have permanently sealed and lubricated bearings. Others require
lubrication from time to time. If your Electric Motor has grease jerks at each end of the motor (over the front and
rear bearings), the bearings require lubrication every six months. Give three pumps of high temperature motor
bearing lubricant into each grease jerk. Use a Polyurea Base Grease such as Chevron SRI (Polyurea Base) or
Shell Dolium R (Polyurea Base).
DO NOT USE LITHIUM OR SILICONE BASE GREASE.
T-Connector Pressure Pick-Up
Replace kinked hoses or tubes. Disconnect each end of the hose/tube and blow air through it to ensure that it is
not blocked. Replace if damaged.
Pressure Transducers
Pressure Transducers are irreparable and cannot be calibrated. If inoperable, check connections at the transducer
and printed circuit board to ensure that there is no visible corrosion, or loose connections.
Plankton Filter Element (Cleaning)
1. Unscrew the bowl counter-clockwise.
2. Remove the Plankton Filter Elements from the bowl.
3. Remove the O-Ring from the top of the bowl.
4. Clean the mesh screen filter elements with a bristle brush and water spray.
5. Wipe the O-Ring with a damp cloth.
63
Maintenance and Repair
Summary of Contents for Aqua Matic XL Series
Page 2: ......
Page 10: ......
Page 28: ......
Page 38: ......
Page 45: ...45 Commissioning...
Page 46: ......
Page 58: ......
Page 76: ......
Page 89: ...Chapter 10 Appendix 89...
Page 90: ...ABS Certificate of Design Assessment Aqua Matic XL 2200 3600 90...
Page 91: ...FCC Compliance 91 Appendix...
Page 92: ...DNV ISO 9001 Certificate Aqua Matic XL 2200 3600 92...
Page 93: ...Single Phase Electrical Motor Wiring 93 Appendix...
Page 94: ...Three Phase Electrical Motor Wiring Aqua Matic XL 2200 3600 94...
Page 95: ...Three Phase Transformer Wiring 95 Appendix...
Page 96: ...New System Initial Readings Form Aqua Matic XL 2200 3600 96...
Page 97: ...Daily System Readings 97 Appendix...
Page 98: ......
Page 99: ...Chapter 11 Exploded Parts Views 99...
Page 100: ...Exploded Parts View...
Page 103: ...7 8 9 10 11 12 13 14 15 16 17 20 19 18 21 22 23 24 25 26 1 2 3 4 5 6 Exploded Parts View 4...
Page 111: ...14 13 2 16 13 12 3 8 10 9 7 1 5 4 6 14 13 15 15 17 13 12 11 18 15 Exploded Parts View 12...
Page 113: ...19 16 2 21 16 14 3 9 11 10 8 1 5 4 6 12 22 20 18 16 17 15 15 13 7 Exploded Parts View 14...
Page 115: ...2 3 10 12 11 9 1 5 4 21 13 20 18 15 19 18 19 15 17 14 16 8 18 15 7 Exploded Parts View 16...
Page 117: ...10 26 11 9 5 5 4 20 1 7 18 3 2 16 13 15 12 14 13 23 24 21 24 25 Exploded Parts View 18...
Page 119: ...12 10 13 11 5 5 4 6 1 9 20 3 2 17 16 14 18 15 19 17 16 14 18 15 8 7 Exploded Parts View 20...
Page 128: ...6 7 2 3 2 5 10 10 12 1 11 8 9 8 11 6 7 4 2 13 14 29...
Page 138: ...Chapter 12 Electric Diagrams Foldouts 101...
Page 139: ...Aqua Matic XL Series Three Phase Wiring Diagram...
Page 140: ......
Page 141: ......