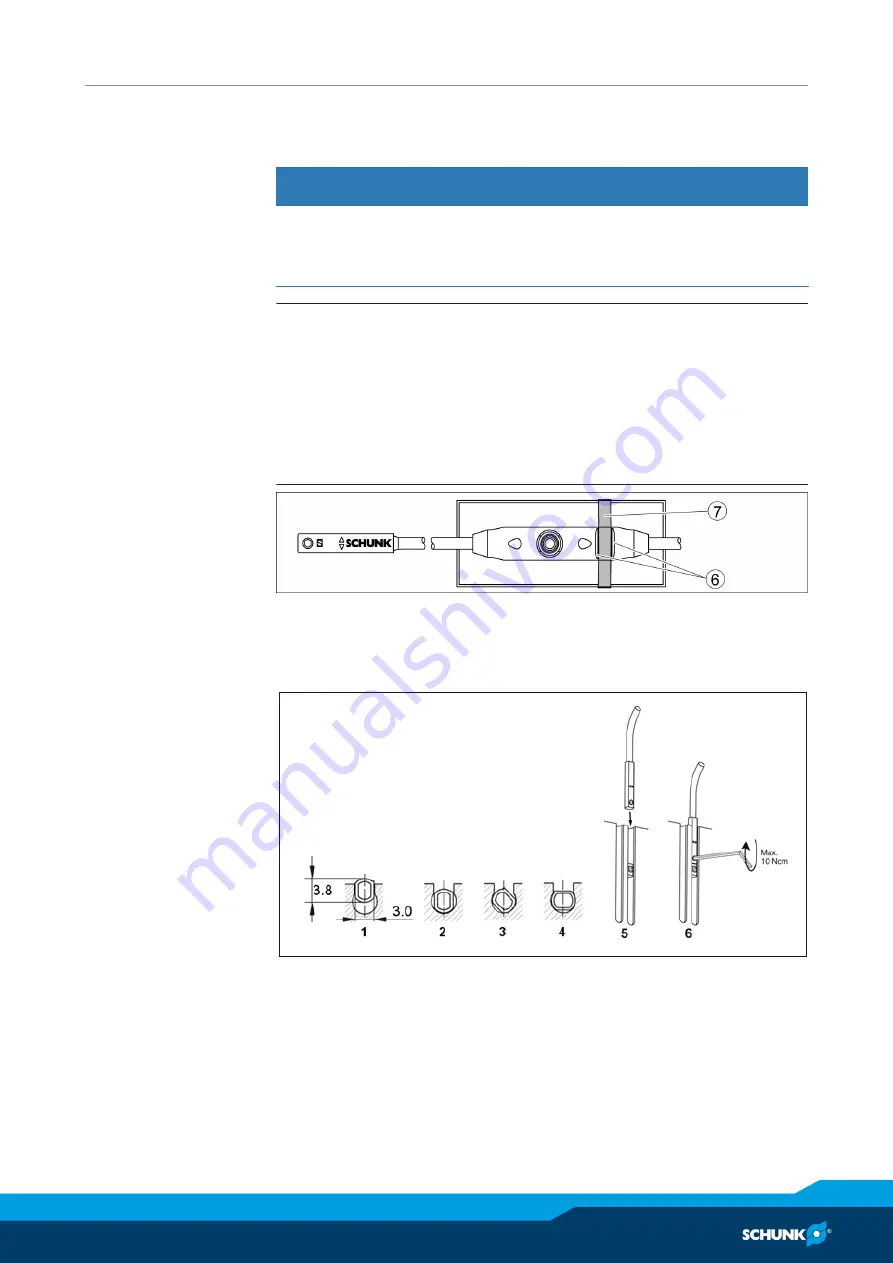
Assembly
09.00 | PWG-plus | Assembly and operating manual | en | 389495
29
Mounting of the
sensor
CAUTION
Sensor can be damaged during assembly.
•
Do not exceed the maximum tightening torque of 10 Ncm for
the set screws!
NOTE
Ferromagnetic material changes the switching positions of the
sensor (e.g. Adapter plate made of ordinary steel).
For ferromagnetic adapter plates:
• The module must be first mounted on the adapter plate.
• Then, the position of the magnetic switchs has to be set.
Ø
To relieve the cable, the electronics have to be fixed in place
using cable ties (7).
There are ribs (6) in place on the electronics for mounting
purposes.
Ø
Turn in the sensor (1 - 4).
OR
Push the sensor axially into the slot until it contacts the stop (5).
Ø
Fix the sensor with an Allen wrench (6).