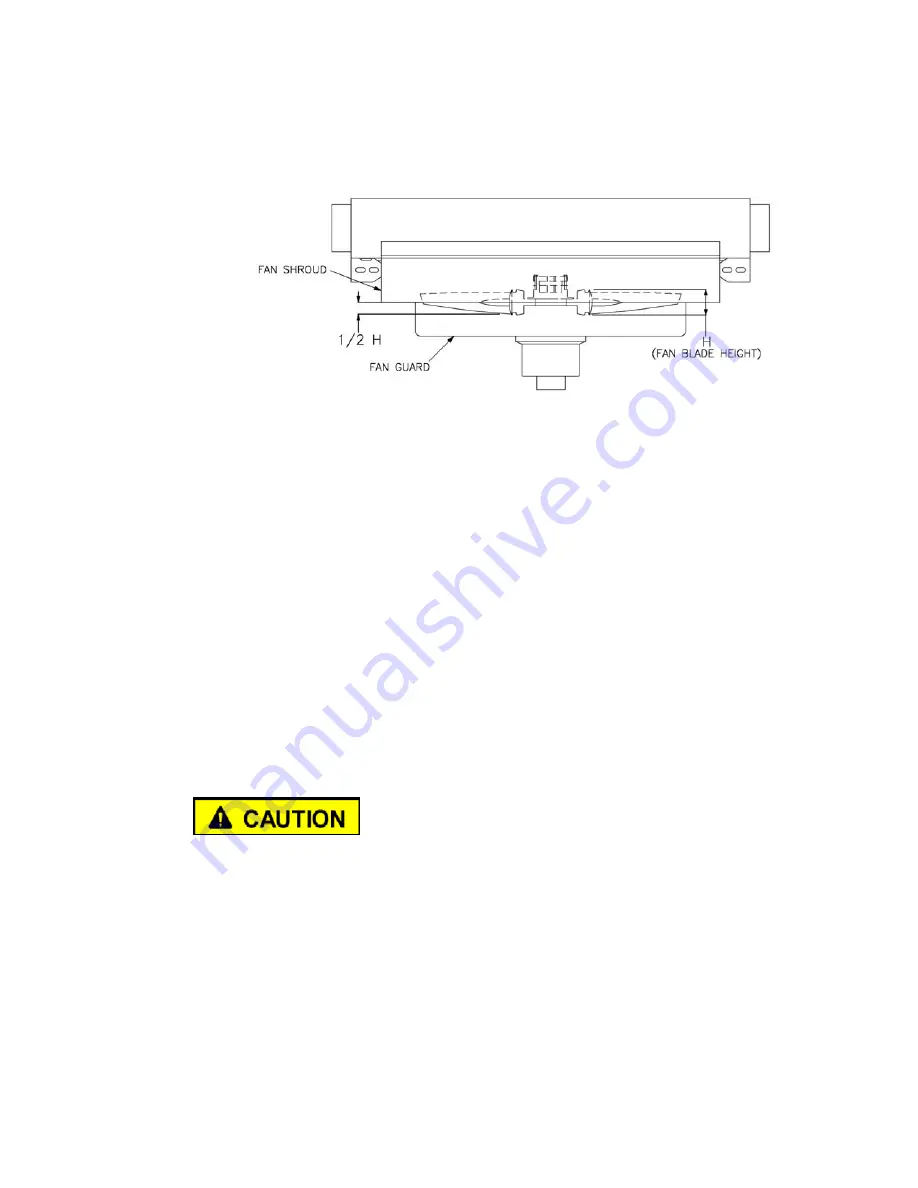
Copyright © 2020 Axxiom Manufacturing, Inc. 47
8.5.2. Fan shroud, Fan, Fan Guard, and Motor
Inspect weekly: Dirt and grease should be removed from these parts. Rusty or corroded
surfaces should be sanded clean and repainted. Replace any component that is damaged or
corroded. Install fan blade assembly as shown in Figure 8.1.
Note:
A corroded fan shroud allows fan air flow to escape resulting in cooling reduction.
Damaged fan guard may not protect personnel from contact with moving parts.
Figure 8.1 – Fan Blade Assembly
8.5.3. Internal Cleaning:
Once a year disconnect piping and circulate a degreasing agent through
the unit to remove sludge from the internal tubes. This will return the unit to full operating
capacity. A thorough cleaning of the entire system in the same manner is desirable to avoid
carry-over from unclean piping. The pre-filter (#1), after-filter (#2), air motor (#5), air filter
(#14), air regulator (#14), and air lubricator (#15) should all be removed and serviced
following this cleaning operation.
8.5.4. Air Motor Air Supply Filter/Regulator:
Once a day completely open the filter/regulator
petcock drain to purge moisture and debris. The aftercooler fan speed can be controlled by
changing the supply air pressure. Confirm that the air motor pressure does not exceed the
specified maximum pressure (see Section 11.0, Table 2).
8.5.5. Air Motor Lubricator:
Once a day fill the air lubricator reservoir (#15) with oil. The air
motor manufacturer recommends a detergent SAE #10 automotive engine oil or GAST
AD220 oil; however, SAE 10W-30 may be substituted. Adjust the oil-fog lubricator (#15)
to the proper flow rate (see note below). The lubricator flow rate is adjusted based upon the
air cfm flow rate required for the air motor. Refer to Section 11.0, Table 2 for air flow and
drip rate requirement. Turn the socket head screw on top of the lubricator to adjust flow
(clockwise to increase flow, counterclockwise to decrease flow).
Failure to properly lubricate the air motor as detailed above will result in costly motor
failure.
Note:
Two types of lubricators have been used in Schmidt® AirPrep Systems. Current
production units are equipped with “oil-fog” lubricators (Style MP). Systems manufactured
prior to September 2016 are equipped with “micro-fog” lubricators (Style L74M). Micro-
fog lubricator drip rates are significantly higher because only a fraction of the drip total
enters the air stream.
Filter/regulator and lubricator arrangement may vary from what is shown in the drawings
included in this manual. Verify the type lubricator then adjust the drip rate accordingly.
8.5.6.
Air Motor
:
If the motor is sluggish or inefficient, disconnect the air line and muffler (#17),
and then add several teaspoons of solvent directly into the motor. Rotate the motor shaft by
hand in both directions for a few minutes. Reconnect the air line and slowly apply air
pressure until there is no trace of solvent in the exhaust air. Re-lubricate the air motor with
a squirt of oil in the chamber. Reassemble and return to service.
Summary of Contents for ACS 1200
Page 8: ...8 Copyright 2020 Axxiom Manufacturing Inc THIS PAGE IS INTENTIONALLY BLANK ...
Page 54: ...54 Copyright 2020 Axxiom Manufacturing Inc 9 2 a ACS 400 2500 Aftercooler System Air Motor ...
Page 62: ...62 Copyright 2020 Axxiom Manufacturing Inc 9 6 a ADS 400 2500 Air Dryer System Air Motor ...
Page 66: ...66 Copyright 2020 Axxiom Manufacturing Inc 9 8 a ADS 400 2500 Air Dryer System Electric Motor ...
Page 75: ...Copyright 2020 Axxiom Manufacturing Inc 75 NOTES ...