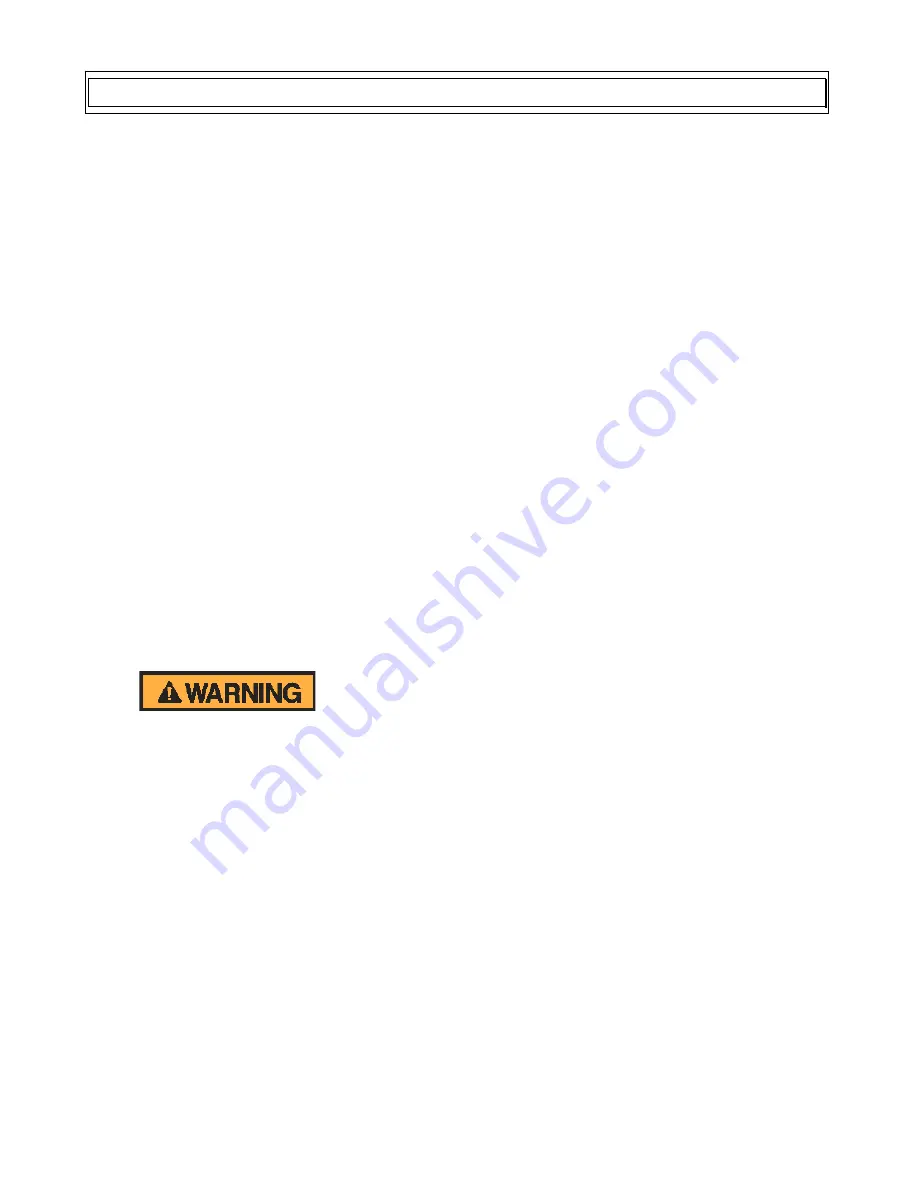
Copyright © 2020 Axxiom Manufacturing, Inc. 29
See Figure 5.1 to help understand the general operation of an AirPrep System. Do not attempt to operate
the AirPrep System before reading all sections of this manual and following all setup procedures. See
Sections 5.1 through 5.14 and Section 6.0.
An AirPrep System is designed to cool, clean and dry compressed air for use in abrasive blasting
equipment. The system removes moisture and contaminants that shorten the life of equipment controls and
decrease blasting efficiency.
Compressed air enters the AirPrep System at the pre-filter (#1) which filters trash and condensed moisture
from the incoming air. The air flow then enters the aftercooler radiator (#4) where the flow is passed
through a heat exchanger. The heat exchanger is constructed of many tubes through which the compressed
air passes. Air flow created by the fan and air motor assembly (#5) is blown across the heat exchanger
tubes which cools the compressed air. The cooling of the air condenses much of the moisture into water
droplets. The cooled air and water droplets flow into the separator tank (#12) at the inlet. As the air flow
rises through the tank it passes through stainless steel particulate filter (ACS Systems only) or a bed of
marbles then into the deliquescent/desiccant tablets (ADS Systems only). The incoming air flow causes the
condensed moisture to fall to the bottom of the vessel. The moisture collected is drained from the bottom of
the separator tank through the drain valve (#11).
The AirPrep fan air motor is turned on and off by the ball valve (#13). Closing the ball valve will disable
the fan air motor (#5). The AirPrep System
separator vessel
(#12) is depressurized by closing the air
compressor outlet ball valve and then opening the blowdown ball valve (#11) to completely vent the
compressed air.
5.1 AirPrep System Air Inlet
The AirPrep System air inlet is located on the pre-filter (#1). The air inlet port is the same size as
the aftercooler piping (see Section 2.7). On most models there are no fittings or ball valve provided
for the air inlet. Only portable models include inlet/outlet ball valves and crowfeet. Any required
fittings or ball valve must be provided by the owner/operator. Any valves, fittings or hoses installed
on or connected to the AirPrep System air inlet port must have a minimum operating pressure of
150 psi.
Valve, fitting, and/or hose rupture can cause serious injury or death. Do Not install or connect any
valves, fittings or hoses that are not rated for a minimum 150 psi operating pressure.
5.2 Pre-filter
Compressed air enters the system through the air inlet pre-filter (#1) (the maximum inlet pressure
should not exceed 150 psi). The pre-filter removes large particle contaminants and moisture from
the incoming air. The water and debris that is removed by the pre-filter can be drained through the
drain valve (#3) located at the bottom of the pre-filter. This ball valve should be left slightly open
anytime the system is in operation. This allows water to be drained as it is filtered from the air.
Leave the drain valve (#3) closed anytime the AirPrep System is not in use.
5.3 Aftercooler
Radiator
After passing through the pre-filter, the air enters the aftercooler (#4). The aftercooler is a large fan
cooled radiator that reduces the temperature of the compressed air which initiates moisture
condensation. The fan is powered by either an air motor (#5) or an optional electric motor. Refer to
Section 11.0 table 1 for the capacity of the aftercooler unit. The coil surfaces of the aftercooler
radiator must be kept clean to maintain performance (see Section 8.0).
CRITICAL:
All AirPrep
radiators include a 1/4" drain port plugged at the time of manufacture. When operating the system
in an environment where freezing is possible install a ball valve in the radiator drain port to allow
draining of accumulated water. This will protect against damage caused by inside water freezing.
5.0 AirPrep System General Operation
Summary of Contents for ACS 1200
Page 8: ...8 Copyright 2020 Axxiom Manufacturing Inc THIS PAGE IS INTENTIONALLY BLANK ...
Page 54: ...54 Copyright 2020 Axxiom Manufacturing Inc 9 2 a ACS 400 2500 Aftercooler System Air Motor ...
Page 62: ...62 Copyright 2020 Axxiom Manufacturing Inc 9 6 a ADS 400 2500 Air Dryer System Air Motor ...
Page 66: ...66 Copyright 2020 Axxiom Manufacturing Inc 9 8 a ADS 400 2500 Air Dryer System Electric Motor ...
Page 75: ...Copyright 2020 Axxiom Manufacturing Inc 75 NOTES ...