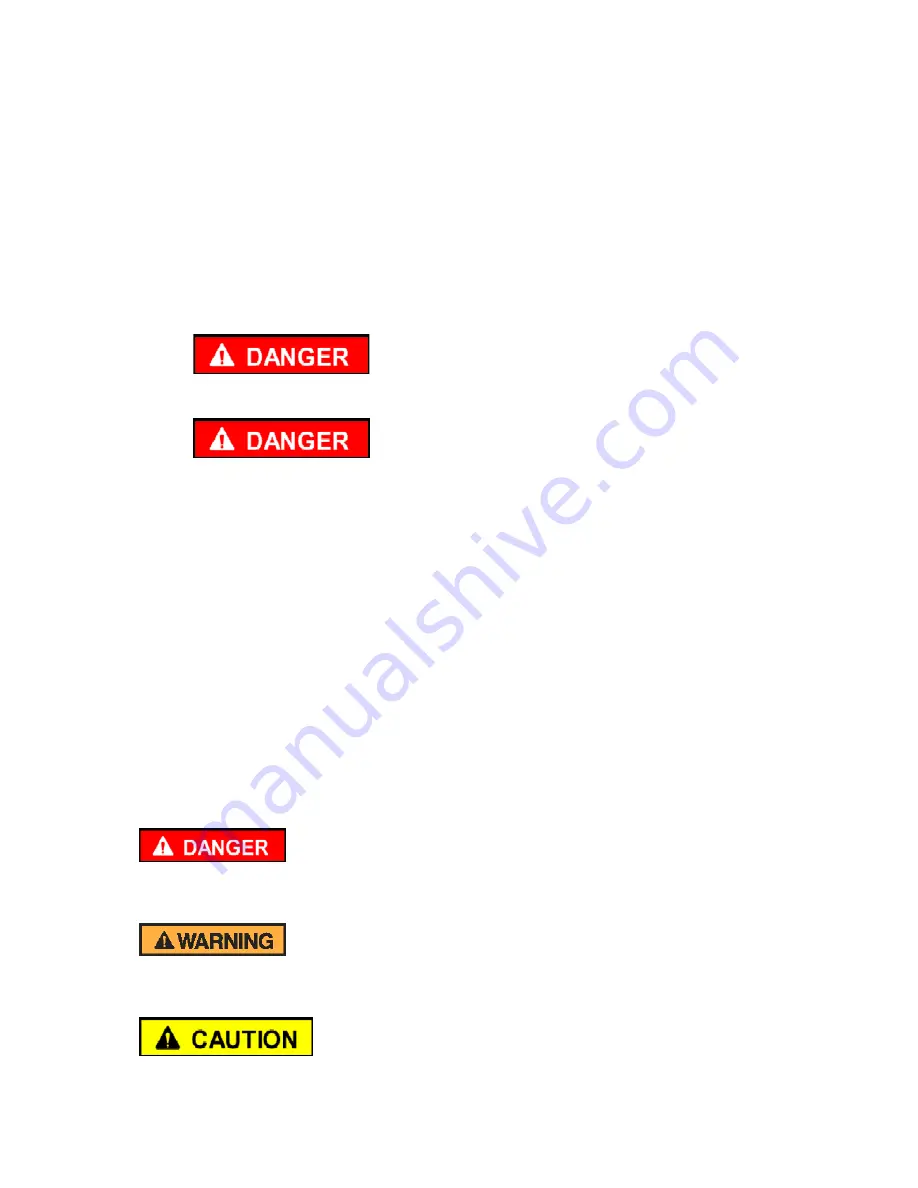
48
Copyright © 2020 Axxiom Manufacturing, Inc.
8.5.7 Air Motor Exhaust Muffler:
Inspect the air motor exhaust muffler monthly. Dirt and grime
accumulation on the exhaust element can restrict air flow and cause a reduction of power
output from the air motor. Remove the muffler and clean with a degreasing agent.
8.5.8. Electric Motor
Keep outside surface free of dirt and grease so motor will cool properly. Make sure cooling
air over motor is not obstructed. The motors are normally furnished with sealed bearing that
do not require maintenance. However, if the motor is equipped with an Alemite fitting,
clean the tip, and apply grease gun. Use 1 to 2 full strokes on motors in NEMA 215 frame
and smaller, 2 to 3 strokes on NEMA 254 through 365 frame and 3 to 4 strokes on NEMA
404 frames and larger. On motors having drain plugs, remove grease drain plug and operate
motor for 20 minutes before replacing drain plug. Refer to motor nameplate. Motors
furnished with ball bearings require lubrication every 6 months.
Electric Shock Hazard. Disconnect electric power to motor before performing any routine
maintenance.
Electric Shock Hazard. Power connections to AirPrep System with electric motors expose
operators to high electrical voltages. Contact with high electrical voltages can result in
serious injury or death. Only qualified personnel should install or perform maintenance on
the electrical system.
8.6
Separator Tank Deliquescent/Desiccant (ADS Systems Only)
Check the deliquescent/desiccant level monthly. At each filling of deliquescent/desiccant check
inside the separator tank for looseness of the deliquescent/desiccant tablets (#9). Extended exposure
to moisture will fuse the tablets together and can possibly block or restrict air flow. Break apart
fused tablets with a long rod or similar device. Fill with tablets to the top of the separator tank
(#12). Note: Minimum tablet size is 5/8” x 3/4". Smaller sizes will reduce air flow through marble
bed (#10).
8.7.
Blast and Air Hoses, Piping, Pipe Fittings, and Wires:
All air hoses, blast hoses, control hoses,
pipe, pipe fittings, and wires are wear items on any abrasive blaster. These components should be
inspected daily for air leaks, cracks, holes, dry rotting, cuts, or any other damage. Repair or replace
any components that show any signs of wear or damage.
Damaged hoses, piping, pipe fittings or wires can cause system malfunctions and can result in
serious injury or death to operating personnel.
Worn hose assemblies can rupture during operation and the resulting pressurized air stream can
cause serious personal injury.
Static electric shock hazard. To minimize chance of static electrical shock to operating personnel
only use anti-static blast hose, properly electrically bond the blast nozzle, blast hose couplings, and
the equipment, and properly install an earth ground to the abrasive blaster. See Section 5.14.
Summary of Contents for ACS 1200
Page 8: ...8 Copyright 2020 Axxiom Manufacturing Inc THIS PAGE IS INTENTIONALLY BLANK ...
Page 54: ...54 Copyright 2020 Axxiom Manufacturing Inc 9 2 a ACS 400 2500 Aftercooler System Air Motor ...
Page 62: ...62 Copyright 2020 Axxiom Manufacturing Inc 9 6 a ADS 400 2500 Air Dryer System Air Motor ...
Page 66: ...66 Copyright 2020 Axxiom Manufacturing Inc 9 8 a ADS 400 2500 Air Dryer System Electric Motor ...
Page 75: ...Copyright 2020 Axxiom Manufacturing Inc 75 NOTES ...