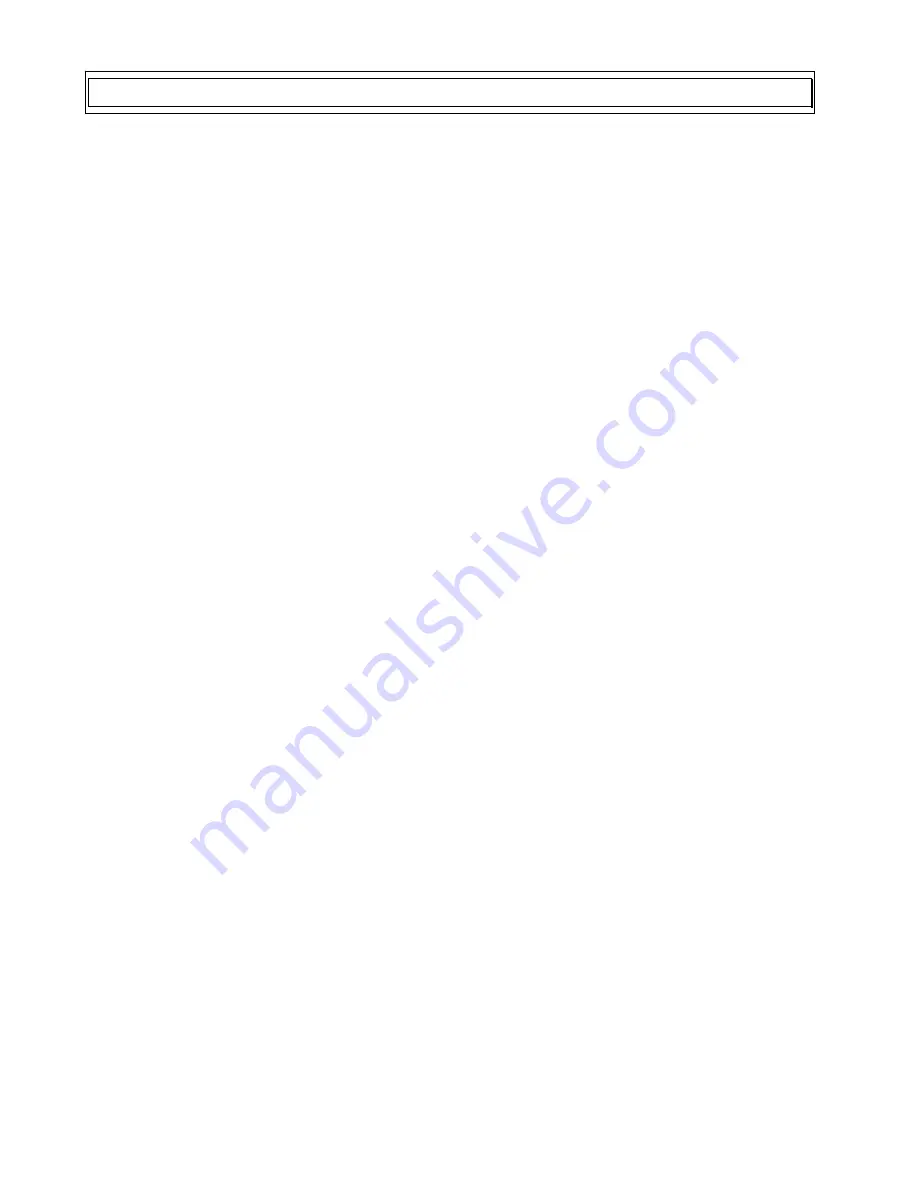
Copyright © 2020 Axxiom Manufacturing, Inc. 23
3.2 Compressed Air Requirements
Blast nozzle
The blast nozzle size and blast pressure determine the compressed air requirements. Available air
flow capacity and/or air compressor size must be considered before selecting the blast nozzle size.
An air source dedicated to the abrasive blast system is preferred to reduce system pressure drops
and back flow of air. If an existing air compressor will be used or a limited air supply is available,
then the blast nozzle must be selected based on these conditions. Be aware that as the blast nozzle
wears the air demand will increase. See Table 1 in Section 13.0 for air consumption by nozzle size
at various pressures. The required air consumption will be used to select the proper size AirPrep
System.
3.3 Air
compressor
size
Air compressor size is crucial to the operation of the abrasive blasting equipment which in turn will
affect the selection of the AirPrep system. Blast nozzle selection and desired productivity must be
evaluated to determine the air flow requirements prior to selecting the air compressor size.
Sufficient air supply capacity is necessary to maintain the system air pressure. Insufficient air flow
capacity will result in reduced blast nozzle pressure and lost productivity. The air compressor must
be large enough to supply:
i.
The sum of blast air requirements for each nozzle at the highest pressure that will be
used (see Section 13.0, Table 1).
ii.
The 12 CFM breathing air supplied to each blast operator respirator.
NOTE
: Reference
OSHA regulations regarding requirements for breathing air, especially when an oil-
lubricated air compressor is used.
iii.
The AirPrep System size should be selected based on the size and capability of the air
compressor to be used to meet the air requirements determined above.
3.4 AirPrep System Air Supply Lines
The air supply hose and fittings connected to the inlet and outlets of the AirPrep System must be
rated at a minimum of 150 psi operating pressure. The air supply hose from the air compressor to
the AirPrep System should be at least the same diameter as the air inlet piping (see Section 2.7).
AirPrep Systems are equipped with smaller secondary outlet ports which can be reduced in size by
installing pipe bushings to match the connecting equipment. Again, the air requirement of the
connecting equipment must be considered so that the proper size piping/hose is selected. See
Section 5.14.
3.5 AirPrep System Air Pressure
The standard maximum operating pressure for AirPrep Systems is 150 psig; however custom
systems may have varying operating pressure. The maximum operating pressure for the AirPrep
System is stamped on the ASME nameplate attached to the vessel. AirPrep Systems equipped with
air motors to drive the cooling fan are supplied with an air pressure regulator. This air regulator is
to reduce the air pressure to the required operating pressure of the fan air motor. The regulator is
pre-set at the manufacturer and should not be altered. The required operating pressure for the fan air
motor is given in Section 11.0, Table 2.
3.0 System
Requirements
Summary of Contents for ACS 1200
Page 8: ...8 Copyright 2020 Axxiom Manufacturing Inc THIS PAGE IS INTENTIONALLY BLANK ...
Page 54: ...54 Copyright 2020 Axxiom Manufacturing Inc 9 2 a ACS 400 2500 Aftercooler System Air Motor ...
Page 62: ...62 Copyright 2020 Axxiom Manufacturing Inc 9 6 a ADS 400 2500 Air Dryer System Air Motor ...
Page 66: ...66 Copyright 2020 Axxiom Manufacturing Inc 9 8 a ADS 400 2500 Air Dryer System Electric Motor ...
Page 75: ...Copyright 2020 Axxiom Manufacturing Inc 75 NOTES ...