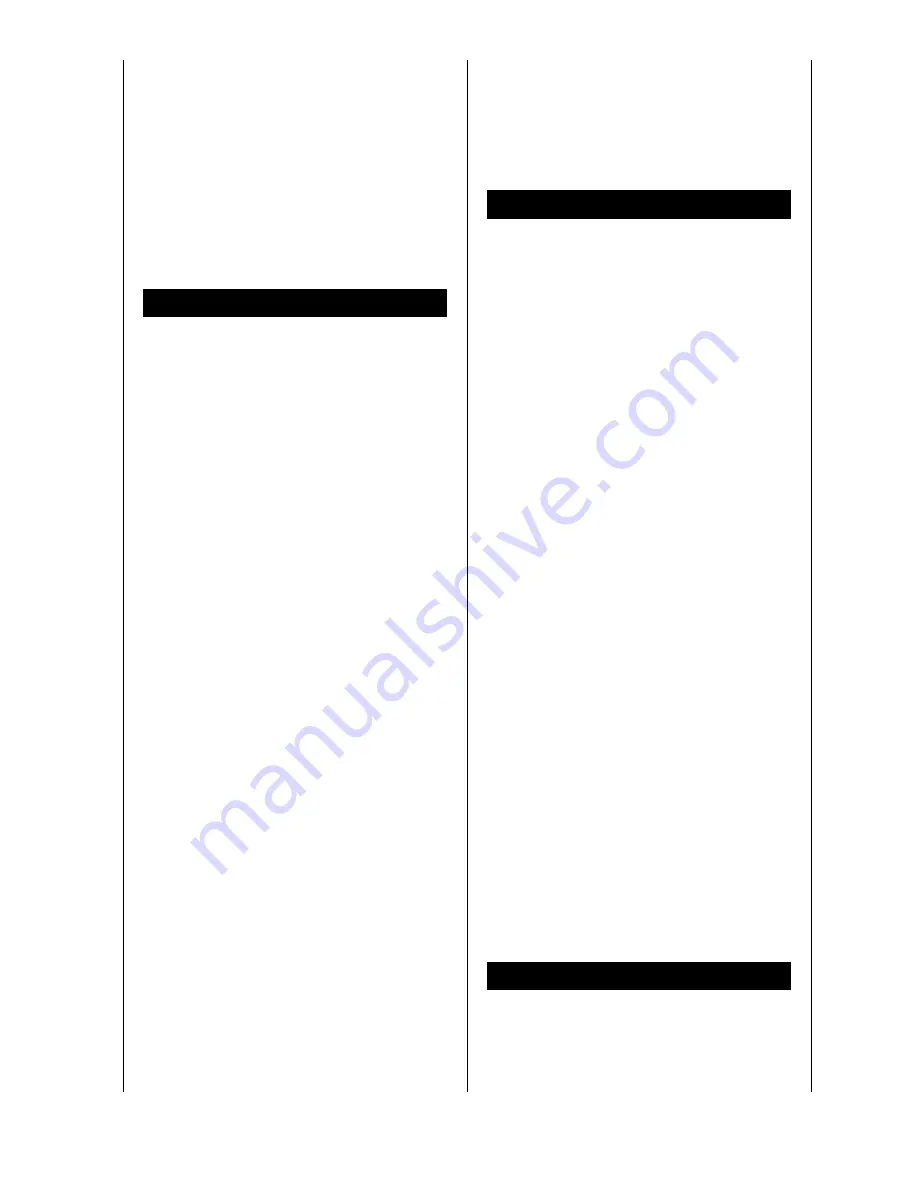
10
5.2)
.
4. Tighten the wing nuts.
5. Put the longitudinal stop on the guide tube at the left
of the saw band, and clamp it. The stop tube must
be parallel to the table groove. A correction can be
performed by releasing the two cylinder head screws
(Fig. 5.3)
.
Installation of the handle, Fig. 6
Mount the handle using a hexagon nut M8 and a washer 8
for the belt tensioning device.
Installation of the handwheel, Fig. 7
Mount the handwheel (ø 120 mm) with a M8 hexagon nut
and a 8 washer for the progressively adjustable speed ad-
justment device.
Initial operation
Please observe the safety instructions prior to the
initial operation of the machine. All protection de-
vices and covers must be mounted when working
with the machine.
Fig. 8
Release and remove the saw band. Insert a new saw band,
and tension it slightly. Turn the band wheel manually in
the cutting direction, and simultaneously perform the final
tension of the saw band. The tension depends on the width
of the saw band. Wide saw bands must be tensioned more
strongly than narrow ones. An excessive tension results in
the premature rupture of the saw band.
Side correction, Fig. 9
1. The saw band should run centrically on the band
wheels.
2. Turn the upper band wheel manually in the cutting
direction, and perform the side correction using the
handle
➀
.
3. Tighten the knurled nut once the adjustment is com-
plete.
Speed regulation, Fig. 10
Please use the handwheel exclusively during the operation
of the device. A non-compliance may result in a damage
of the device.
Turn the handwheel clockwise, decrease the cutting speed.
Increase the cutting speed in the opposite direction within
the
following speed range:
Minimum speed
370 m/min.
For the processing of aluminium, brass, copper, duro-
plastics as well as hard synthetic materials.
Maximum speed
750 m/min.
For the processing of wood.
Saw band guide, Fig. 9
You can adjust the upper saw band guide up to a work
piece height of 205 mm
➂
. The smallest possible distance
to the work piece ensures the optimum band guide and a
safe working!
Counterpressure bearing, Fig. 10
The counterpressure bearings
➀
absorb the feed pressure
of the work piece.
Adjust the upper and lower counterpressure bearings in
such a manner that they slightly strike against the saw
band back.
Guiding rollers, Fig. 10
Adjust the upper and lower guiding rollers
➁
to the cor-
responding saw band width. The front edges of the guiding
rollers may at maximum extend until the tooth root surface
of the saw band. If the guiding rollers slightly touch the
saw band, fix the position of the rollers with the knurled
screw.
The saw band must not choke up!
Working information:
The following recommendations are examples of the safe
use of band saws. See page K4.
The following safe working methods should be seen as an
aid to safety. They cannot be applied suitably completely
or comprehensively to every use. They cannot treat every
possible dangerous condition and must be interpreted
carefully.
• Connect the machine to a
suction unit
when working in
closed rooms. A suction device which conforms with
commercial regulations must be used for suction in
commercial areas.
• Loosen the sawband when the machine is not in opera-
tion (e.g. after finishing work). Attach a notice on the
tension of the saw band to the machine for the next
user.
• Collect unused sawbands and store them safely in a dry
place. Check for faults (teeth, cracks) before use. Do not
use faulty sawbands!
• Wear suitable gloves when handling sawbands.
• All protective and safety devices must be securely
mounted on the machine before beginning work.
• Never clean the sawband or the sawband guide with a
hand-held brush or scraper while the sawband is run-
ning. Resin-covered sawbands impair working safety and
must be cleaned regularly.
• For your own protection, wear protective glasses and
hearing protection. Wear a hairnet if you have long hair.
Roll up loose sleeves over the elbows.
• Always position the sawband guide as near the work-
piece as possible when working.
• Insure sufficient lighting in the work area and around the
machine.
• Always use the fence for straight cuts to keep the work-
piece from tipping or slipping away.
• When working on narrow workpieces with manual feed,
use the
push stick.
• For diagonal cuts, place the saw bench in the appropri-
ate position and guide the workpiece on the fence.
• To cut dove-tails and dove-tailed tenons or wedges swing
the saw bench to the plus or minus position. Insure safe
workpiece guidance.
• For arced and irregular cuts, push the workpiece evenly
using both hands with the fingers together. Hold the
workpiece with your hands on a safe area.
• Use a pattern for repeated arced or irregular cuts.
• Insure that the workpiece does not roll when cutting
round pieces.
• Use the
traverse cutting gauge special accessory
for
safety when making traverse cuts.
• To safely cut round plates, use the
circular cutting unit
special accessory.
Maintenance
Perform resetting, measuring, and cleaning work
exclusively when the motor is turned off. Discon-
nect the mains plug, and wait until the rotating
tool stands still.