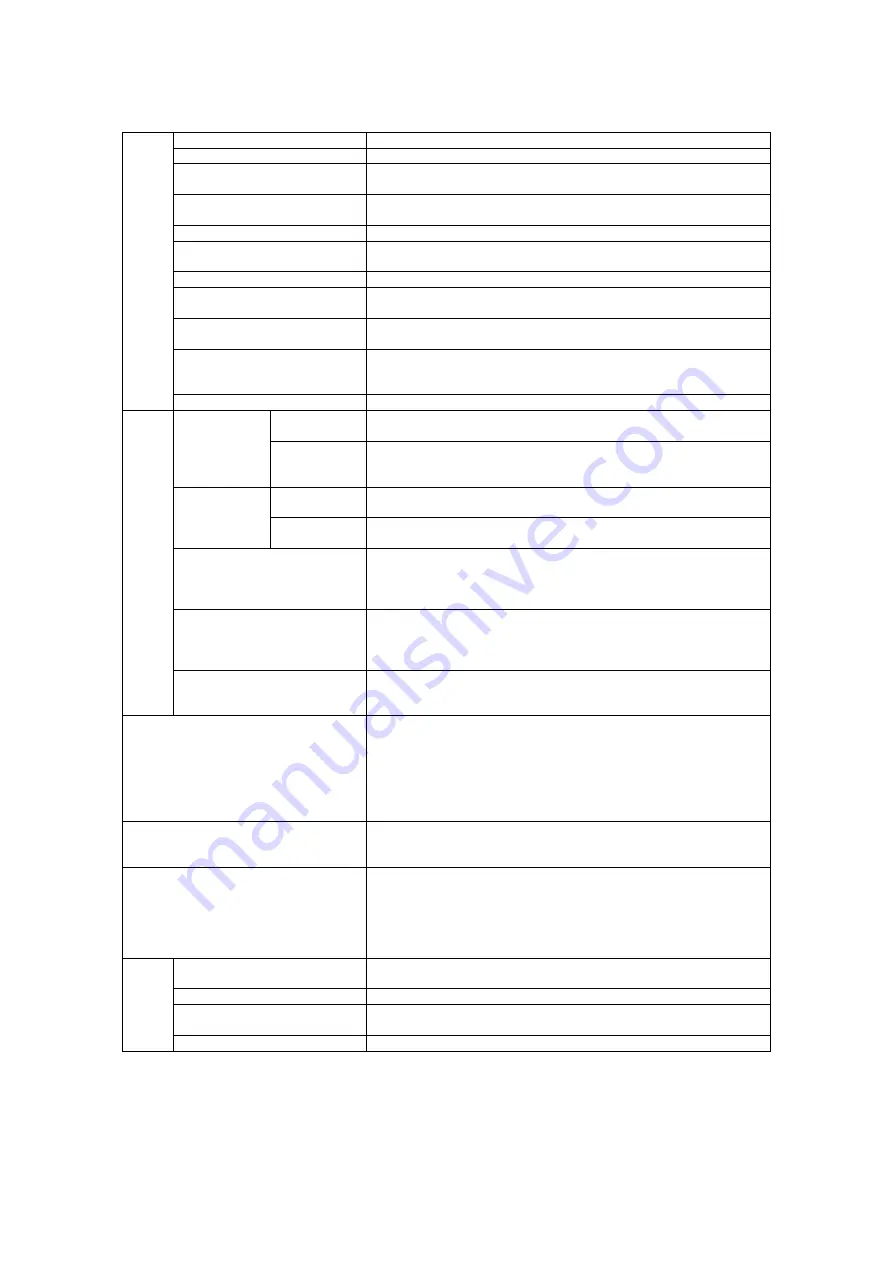
8
Individual Specification
■Standard Specification
C
ont
rol
ling
C
har
a
c
ter
is
tic
s
Control mode
Adopting SVPWM or SPWM modulating techniques
Output frequency range
0.01~400.0Hz
Frequency setting analyzing
degree
0.1Hz
Output frequency analyzing
degree
0.1Hz
PWM load wave frequency
Available to modulate from 2 to 12kHz.
Torque increase
Auto torque-increase and auto slip compensation, at 5Hz the
starting torque can reach 150% of rated torque.
Jog frequency
3 points can be set from 0.1 to 400.0Hz
Acceleration/deceleration
time
0.1 to 600.0seconds. (2 steps of accel/decel time can be set
separately.)
Stall Prevention Level
According to the load characteristics of motor, it’s available to be
set as 50 to 200% of rated current of the drive
DC braking
Available to be operated from 0.1 to 60.0Hz from STOP, braking
current 0 to 100% of the rated current. Starting time 0 to 60.0
sec. Stopping time 0 to 60.0 sec.
V/F curve
V/F curve available to be set
O
per
at
io
n C
har
a
c
ter
is
tic
s
Frequency
setting signal
Digital
Operator
Set by UP and DOWN
External
information
Potentiometer 5K
Ω
, 0-10VDC, multi-function input choosing3-5
(7 velocities: jog-on, up/down command), serial communication
(RS-485)
Running
operating
signal
Digital
Operator
Available to be operated by RUN, STOP and JOG keys.
External
terminals
2 wire style (Fwd/Stop, Rev/Stop, Run/Stop and Fwd/Rev)/ 3 wire
operation, JOG running, Serial Communication Board(RS-485)
Intelligent Input Terminal
Switching of 7 step pre-set available speed; Switching of
First/Second acceleration/deceleration time; prohibiting
acceleration/deceleration and external interrupt input; Jog
running UP/DOWN frequency terminal setting; Count terminals
Intelligent Output Terminal
During running, frequency agreement output, non-zero count
agreement output, over torque output, external interrupt
reference, low voltage detection, operation mode reference, fault
output and external fault interruption.
Analog signal output
Corresponding to output current, output frequency 1( before slip
ratio compensation), output frequency 2( after slip ratio
compensation), output voltage, consumed power, DC bus voltage
Built-in Function
Setting max/min output frequency; momentary power off
restarting; fault restarting; setting of S curve
acceleration/deceleration time; auto-voltage stabilizing output
modulation; digital frequency output signal; fault records;
parameters locking; reset to factory setting; inhibiting reverse run;
over current stalling prevention, over voltage stalling prevention,
electrical thermal relay.
Protection Function
Over current; over voltage, low voltage;’ external fault interruption
input; motor over load; over load of the drive and drive
overheating
Digital operator
Consisting of 6 functional keys, 7 step LED in 4 digits; 4 status
LED indicators. Available to set frequency, display actual output
frequency, output current, self-determined unit parameter
overview of users, modify settings and for parameter locking,
fault displaying. Available to perform running, stop, reset, fwd/rev
run and jog run.
env
iron
m
ent
Operational Environment
temperature
-10
℃
to +50
℃
(+40
℃
parallel installation, no condensation, no
freezing)
Storing temperature
-20
℃
to +60
℃
Operational Environment
dampness
Below 90%RH without moister
Installation height
Lower than 1000m, without corrosive gas, fluid and dust.