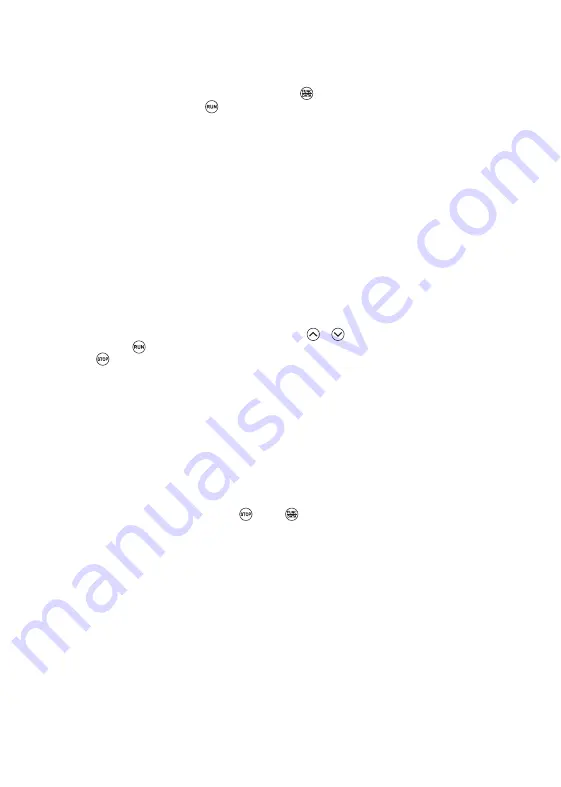
53
(2) Preparation Mechanical System
Take dismantling for motor gearing
(3) Auto-tuning execution procedures
①
Set “1” or “2”in function parameter 03
.
04 and press key.
②
Enter a run command. (press key on keypad as forward running. If it takes reverse running,
change the data of function parameter 00
.
02).
③
After enter a run command, Tuning starts with the motor stopped . Auto-tuning time: max. 40 to 80 s.
④
When function parameter 03
.
04* = 2, after the tuning in
③
above, the motor is accelerated to
around 50% of base frequency and then tuning starts Upon completion of measurements, the motor
decelerates to a stop.
(Estimated tuning time: Acceleration time + 20 to 75 s + Deceleration time)
⑤
When function parameter 03
.
04* = 2, after the motor deceleration to a stop in
④
above, tuning
continues with the motor stopped. (Max. tuning time: 40 to 80 s.)
⑥
Automatically turn the run command OFF to complete tuning
■
Auto-tuning errors
Remove the error cause, Refer to the basic function parameters of V/f Control / Common Dynamic
Torque Vector Control to set and auto-tuning. ■ <1> Auto-tuning errors
4.1.6 Running the inverter for motor operation check
After completion of preparations for a test run as described above, start running the inverter for motor
operation check using the following procedure.
(1) S Set a low reference frequency such as 5 Hz, using
/
keys on keypad.
(2) After pressing key, the inverter starts forward running.
(3) Press key, and the inverter is decelerated and stopped.
(4) Check that the motor is running in the forward direction. and Check for smooth rotation without
motor humming or excessive vibration, Check for smooth acceleration and deceleration.
When no abnormality is found, then increase the reference frequency to start driving the motor.After
test run is passed and it is confirmed there is not any problems, it can be running.
After verifying normal motor running with the inverter in a test run, connect the motor with the machin-
ery and perform wiring for practical operation.
(1) Configure the application related function parameters that operate the machinery.
(2) Check interfacing with the peripheral circuits.
1) Mock alarm
Generate a mock alarm by pressing the “ key + key ” on the keypad for 5 s or more and check
the alarm sequence. The inverter should stop and issue an alarm output signal (for any fault).
2) I/O checking
Check interfacing with peripherals using Menu d "I/O Checking" on the keypad in Programming
mode.
3) Analog input adjustment
Adjust the analog inputs on terminals AVI, ACI, AUI using the function parameters related to the
offset, filter and gain that minimize analog input errors.For details,See Chapter 5" Function Param-
eters List”
4) Calibrating the [AFM] output
Calibrate the full scale of the analog meter connected to the terminal AFM. using the reference
voltage equivalent to +10 VDC. To output the reference voltage, it is necessary to select the analog
output test with the unction code 00
.
31 Calibrate full range of the meter.
5) Clearing the alarm history
Clear the alarm history saved during the system setup with the function parameter (04.97 = 1).
4.1.7 Preparation for practical operation