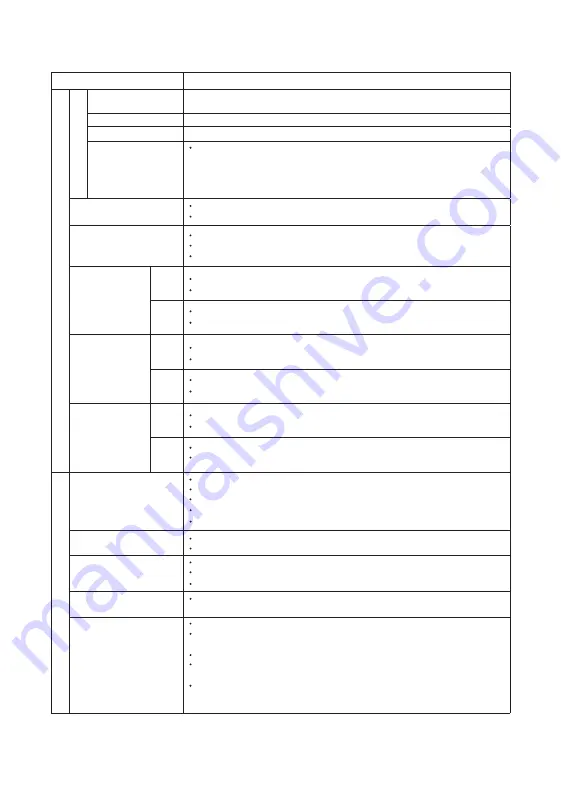
11
2.4.2 Common specifications
Output frequency
Setting range
Maximum frequency
Base frequency
Starting frequency
Carrier frequency
Setting resolution
frequency output
Accuracy (Stability)
Speed
control
range
Speed
control
accuracy
Speed
control
range
Speed
control
accuracy
Speed
control
range
Speed
control
accuracy
Under Vector
control without
speed sensor
Under Vector
controlwith speed
sensor
Control method
Torque boost
Start/stop operation
Voltage /frequency
characteristics
Control
Frequency Setting
Item
Explanation
Under V/F control
of with speed
sensor Under
Dynamic torque
vector control with
speed sensor
25 to 500 Hz (120 Hz under vector control without speed sensor, 200 Hz under
vector control with speed sensor).
25 to 500 Hz (in conjunction with the maximum frequency)
0.1 to 60.0 Hz (0.0 Hz under vector control with/without speed sensor)
0.75 ~ 16 kHz (4T1.5
~
18.5kW).
0.75 ~ 10kHz(2T1.5
~
15 kW,4T22
~
45 kW)
0.75 ~ 6kHz(4T55
~
200kW)
Note: The carrier frequency may automatically drop depending upon the surrounding temper-
ature or output current to protect the inverter. (The automatic drop function can be disabled)
Analog setting: ±0.2% of maximum frequency (at 25 ±10
℃
)
Keypad setting: ±0.01% of maximum frequency (at -10 to +50
℃
)
Analog setting: 1/3000 of maximum frequency (1/1500 for AUI input)
Keypad setting: 0.01 Hz (99.99 Hz or less), 0.1 Hz (100.0 to 500.0 Hz)
Link operation setting: 1/20000 of maximum frequency or 0.01 Hz (fixed)
1 : 100 (Minimum speed: Base speed, 4P, 7.5 to 1500 r/min)
1 : 2 (Constant torque range: Constant output range)
Analog setting: ±0.2% of maximum speed (at 25 ±10
℃
)
Digital setting: ±0.01% of maximum speed (at -10 to +50
℃
)
1 : 200 (Minimum speed: Base speed, 4P, 7.5 to 1500 r/min)
1 : 2 (Constant torque range: Constant output range)
Analog setting: ±0.5% of maximum speed (at 25 ±10
℃
)
Digital setting: ±0.5% of maximum speed (at -10 to +50
℃
)
1 : 1500 (Minimum speed: Base speed, 4P, 7.5 to 1500 r/min)
1 : 4 (Constant torque range: Constant output range)
Analog setting: ±0.5% of maximum speed (at 25 ±10
℃
)
Digital setting: ±0.01% of maximum speed (at -10 to +50
℃
)
Possible to set output voltage at base frequency and at maximum frequency
AVR control ON/OFF selectable. Non-linear V/F pattern with three arbitrary points
Keypad ( RUN/STOP keys), external signals (run forward (run reverse) run/stop
command etc.),Communications link (RS-485).
Auto torque boost (for constant torque load)
Manual torque boost: Desired torque boost (0.0 to 20.0%) can be set
Select application load with function (Constant torque load or variable torque load)
Keypad ( Can use UP/DOWN keys to set)
Analog input:DC0 to ±10V/0 to ±100%( terminal AVI
、
AUI)
:
DC 4 to 20mA/0 to 100% (terminal AVI)
UP/DOWN operation: Multi-frequency (16 steps), 16-bit parallel
Pulse train input (standard): Pulse input = MI7 terminal, Rotational direction =
general terminals
Reference frequency switching, Remote/local mode switching, Auxiliary
frequency setting, Proportional operation setting, and Inverse operation.
V/f control
Dynamic torque vector control
V/F control of with speed sensor
、
Dynamic torque vector control with speed sensor
Vector control without speed sensor
Vector control with speed sensor (with an optional PG interface card mounted)