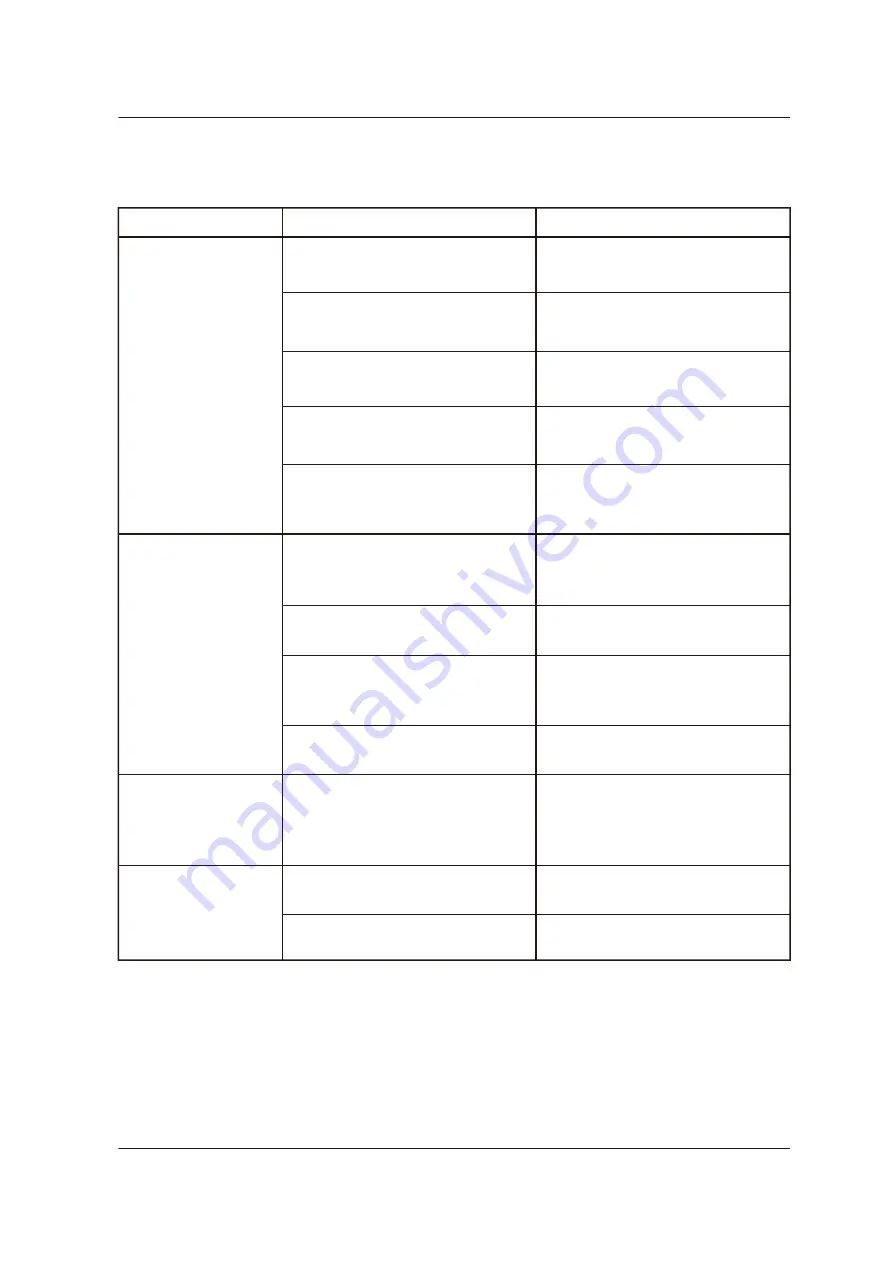
- 29 -
FP120D,FP145D
To prevent serious accidents, disconnect the power supply before inspecting the machine:
Machine doesn’t start
Machine starts but
stops immediately
causing the motor
protector to actuate.
Abnormal noise or
vibration.
No power is supplied.
Contact the electric power company
or check the power source.
Open circuit or poor connection of
the power circuit.
Check the fuse is broken or overload
relay is actuated (shut-off).
The interlock guard is opened.
Check the interlock guard is closed
completely.
Fault of motor, magnetic contactor,
or other component.
Please call service engineer or our
distributor.
The Emergency stop button is
actuated.
Check the hazard is eliminated, then
reset the EMS button and power ON
again.
Voltage drop
Correct the voltage to the rated
voltage, or use an extension cable
that meets the standard.
A 50Hz model is operated at 60Hz
Check the nameplate or call service
engineer.
The outlet is obstructed, and the
miller was operated for oily, sticky
and fibrous material.
Remove the obstruction and confirm
with supplier to sure the intend-use
for what kind material.
Motor abnormal.
Repair the motor or replace with a
new motor by qualified engineer.
The bearing of the motor may be
damaged.
To replace the bearing. Contact the
qualified engineer or our distributor
from whom you purchased the
equipment.
Product doesn’t ideal
The piece is over scope.
Check the specification
Pressure is not reached ideal.
Any other maintenance, service and trouble are welcome to be contacted Yung Lung or our
distributor.
Call supplier or servicer.
Conditions
Reasons
Countermeasure
4.2. Trouble shooting:
CE Instruction Manual
www.samway.com