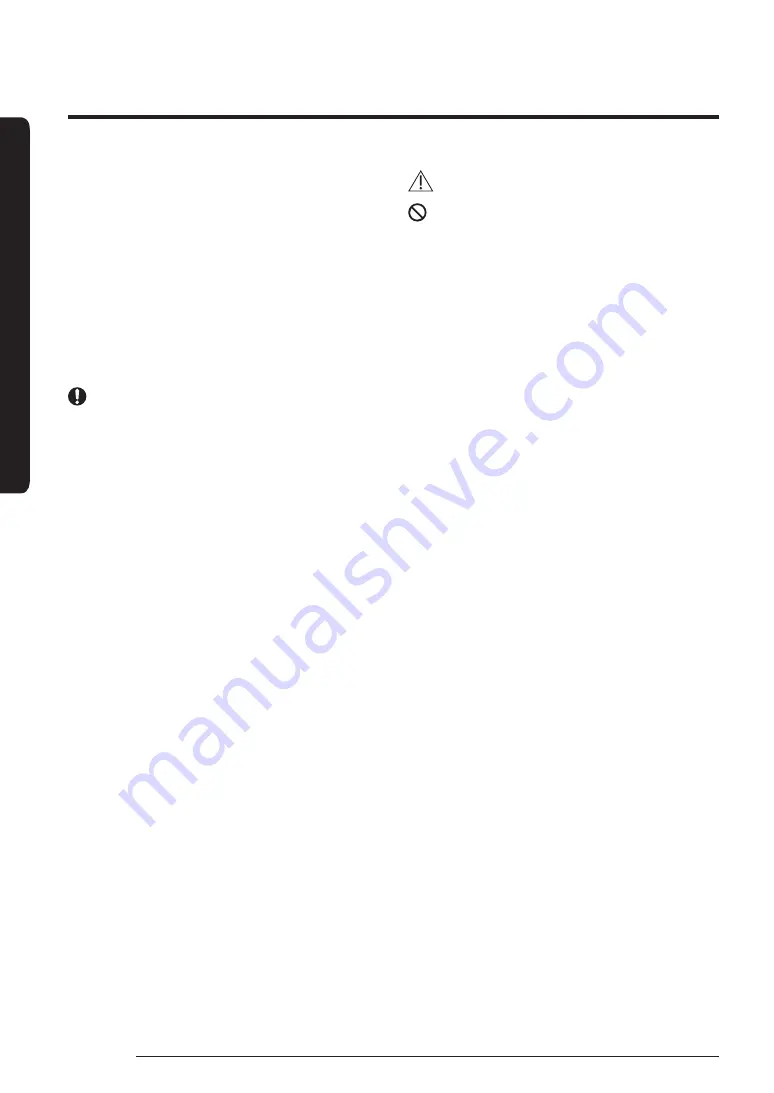
INS
TALLA
TION
Safety information
4
English
Do not operate the product with power switch or
circuit breaker.
ŷ
Potential risk of electric shock or fire.
ŷ
If automatic blackout restore is set, fan may spin
suddenly and it may cause injury.
If fuse load switch is used, do not use incorrect
fuse capacity/size.
ŷ
Usage of incorrect wire may result in product
malfunction or fire.
Do not use flammable gas (such as hair spray or
insecticide) near the product.
ŷ
There are potential risks of electric shock or fire.
If there is any problem (such as burning smell),
stop operation and shut off the circuit breaker.
ŷ
Otherwise, it may cause product malfunction,
electric shock, or fire. Contact the service center.
Use chilled/heating water which is appropriate
according to water maintenance standard.
ŷ
Deterioration of water may cause water leakage.
Contact the merchandise or service center to clean
inside of the product.
ŷ
Error on selecting cleaner and cleaning the
product may harm rubber part and cause water
leakage.
ŷ
If the cleaner reaches to electric parts or motor,
it may cause product malfunction, smoke, or fire.
CAUTION
Do not use the product for preservation purposes.
ŷ
If you use this product for unintended purposes,
such as preservation of machinery, food, art
work or breeding animals or plants, it may cause
damage to their performance, quality or life.
Do not use the holder which is worn out for
longtime usage.
ŷ
It may cause injury due to falling down of the
product.
Do not step onto the product or place any objects
on the product.
ŷ
It may cause injury due to falling down of the
product.
Do not operate the product with the cover of
exterior or electric box opened.
ŷ
It may cause electric shock or fire.
Do not place any objects that are not allowed to be
wet.
ŷ
It may get wet by dripping water caused
by product or refrigerant pipe freezing,
contaminated air filter, blocked drain valve.
Do not change settings for protection device.
ŷ
It may cause fire.
Do not use chilled/heating water for drinking.
ŷ
It is harmful for humans.
ŷ
For hot water supply, use indirect heat exchange.
Do not wash the product with water.
ŷ
It may cause electric shock.
Do not operate protection devices forcibly.
ŷ
This may result in fire or explosion.
Do not touch high temperature part such as
compressor and refrigerant pipe.
ŷ
It may cause burns.
Do not touch inlet or aluminum plate.
ŷ
It may cause injury.
Summary of Contents for AG010KSV Series
Page 85: ...MAINTENANCE 85 English MEMO ...
Page 86: ......