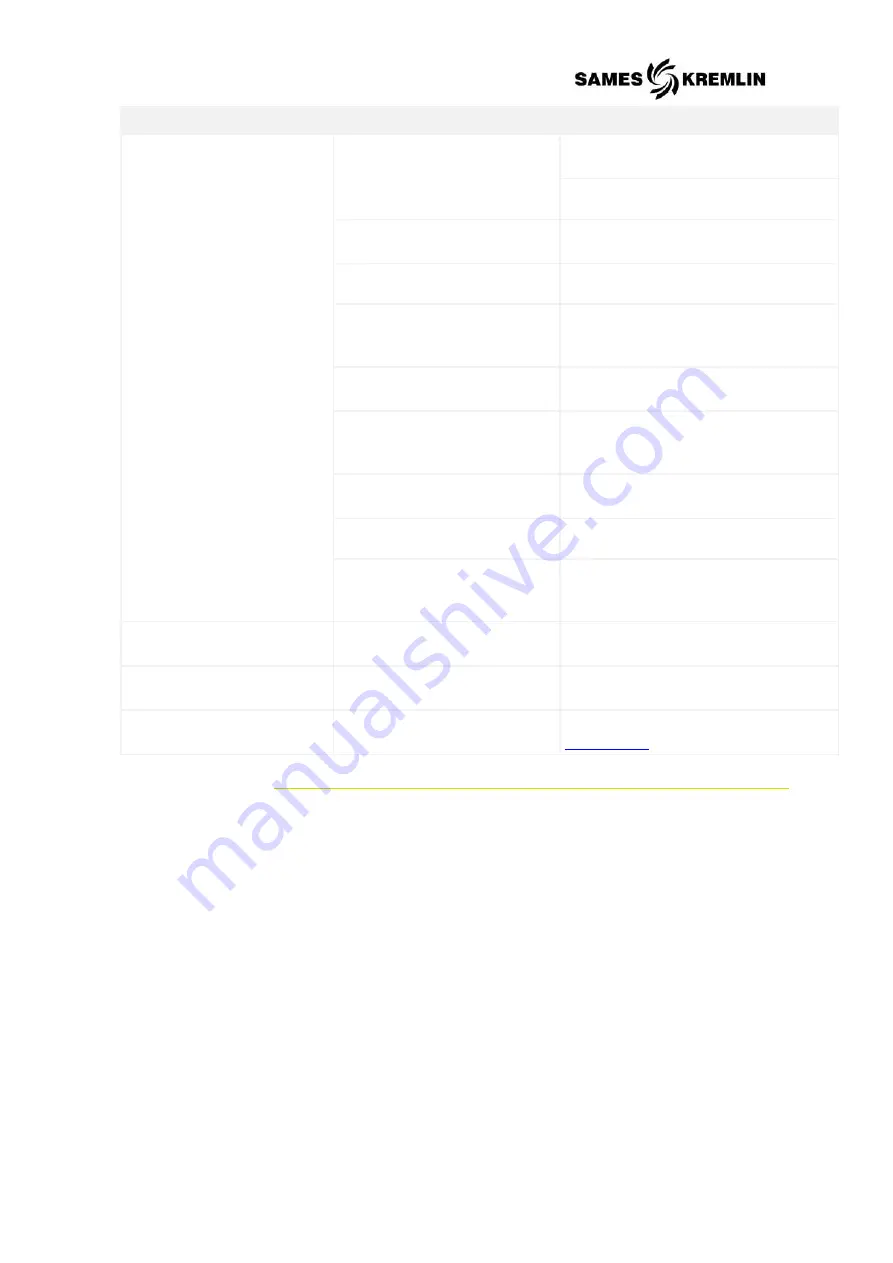
Diagnostic help / Troubleshooting guide
582195110-Complete_Pump-PRIMA-01D100-EN-indA
52
Defaults
Possible causes
Remedies
The pump operates but
does not convey fluid or
stops
Valves clogged up
Clean the pump with the
appropriate cleaning solvent.
Clean or change the valves.
Valves worn or/and
incorrectly mounted
Check and change the parts.
Exhaust hose clogged
Clean or change the exhaust hose.
Hoses leaks, air intake,
suction drop
Check fittings and tighten them up.
Repair and Repair and eliminate
sources of leakage.
No suction at the inlet and
pressure at the outlet
Check ports and if necessary,
change the tightness seals.
Viscosity of the fluid too high High-viscosity fluids are not
conveyable (for limit value refer to
chapter "Technical features")
There are craks or small hoses
on the exhaust hose
Change the exhaust hose.
Air in the pump chamber
Drain the pump.
Air bubble in material
Check the tightness of the
diaphragm washers (tightening
torque: 7.5 N.m. / 5.5 ft/Lbs).
Pump does not stop when
gun trigger is released
Defective valves
Check suction and exhaust valves.
Change them if necessary.
Spraying trouble
Defective spray gun
Refer to spray gun instruction
manual.
Specific problems with
accessories
-
Refer to the instructions for the
Summary of Contents for PRIMA 01D100
Page 85: ...Spare parts 582195110 Complete_Pump PRIMA 01D100 EN indA 85 10 1 Exploded overview...
Page 87: ...Spare parts 582195110 Complete_Pump PRIMA 01D100 EN indA 87 10 3 Upper part and exhaust valves...
Page 88: ...Spare parts 582195110 Complete_Pump PRIMA 01D100 EN indA 88 10 4 Lower part and suction valves...
Page 89: ...Spare parts 582195110 Complete_Pump PRIMA 01D100 EN indA 89 10 5 Distributor...