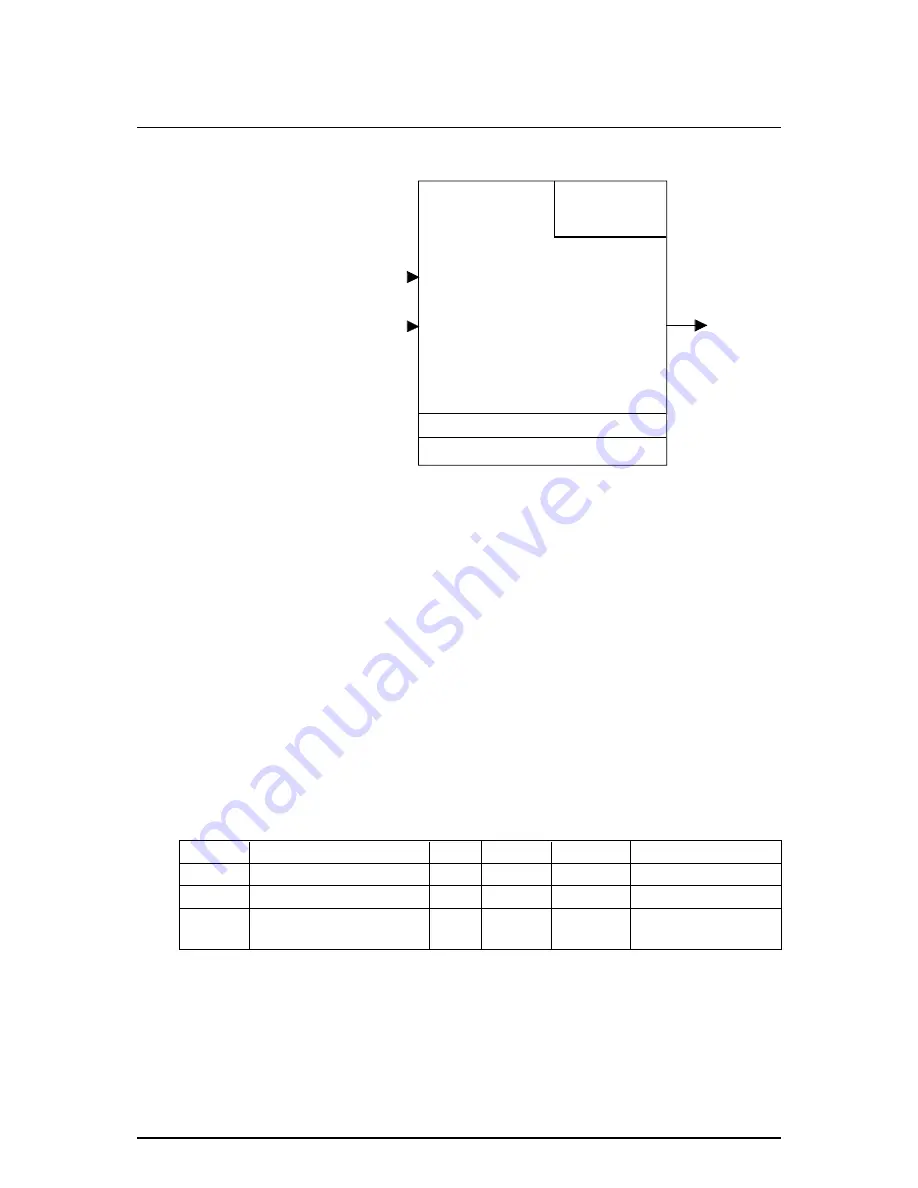
Summary of software elements
PCD2.H31x
Page A-12
SAIA-Burgess Electronics Ltd.
(2H3-AA-E.DOC)
26/762 E2
RdActVel
Instruction:
Read Actual Velocity
[06]
Function description:
This instruction can be use to read the actual velocity of motion. For each
new reading of the velocity this instruction shuld be executed.
The processor format for velocity is 14 bits integer and 16 bits fractional
number. With the present instruction the processor only outputs the integer
part. This means that, at low velocities, values obtained are not comparable
with the result of the 'RdTargVel' instruction, which contains the fractional
part.
If the machine factor is less than 1, low velocities are difficult to read, as
the fractional part of the velocity is not available.
Description of input and output elements concerned:
Par.
Designation/function
Type
Format
Value
Comment
= 1
Module number
K
1 - 16
= 2
Instruction: RdActVel
= 3
PCD register for
actual velocity
R
integer
30 bit *)
dependent on ma-
chine factor
*) Resolution 14 bit
Exec
Function Block
Index modified: no
Processing time: 2.7 ms
= 2
= 1
RdActVel
Module number
= 3
Register
for result
Summary of Contents for PCD2.H310
Page 8: ...Contents PCD2 H31x Page 4 SAIA Burgess Electronics Ltd 2H3 00 E DOC 26 762 E2 Notes...
Page 18: ...Introduction PCD2 H31x Page 1 8 SAIA Burgess Electronics Ltd 2H3 01 E DOC 26 762 E2 Notes...
Page 28: ...Terminals PCD2 H31x Page 4 4 SAIA Burgess Electronics Ltd 2H3 04 E DOC 26 762 E2 Notes...
Page 52: ...Quick start PCD2 H31x Page 6 14 SAIA Burgess Electronics Ltd 2H3 06 E DOC 26 762 E2 Notes...
Page 154: ...SAIA Burgess Electronics Ltd Your suggestions...