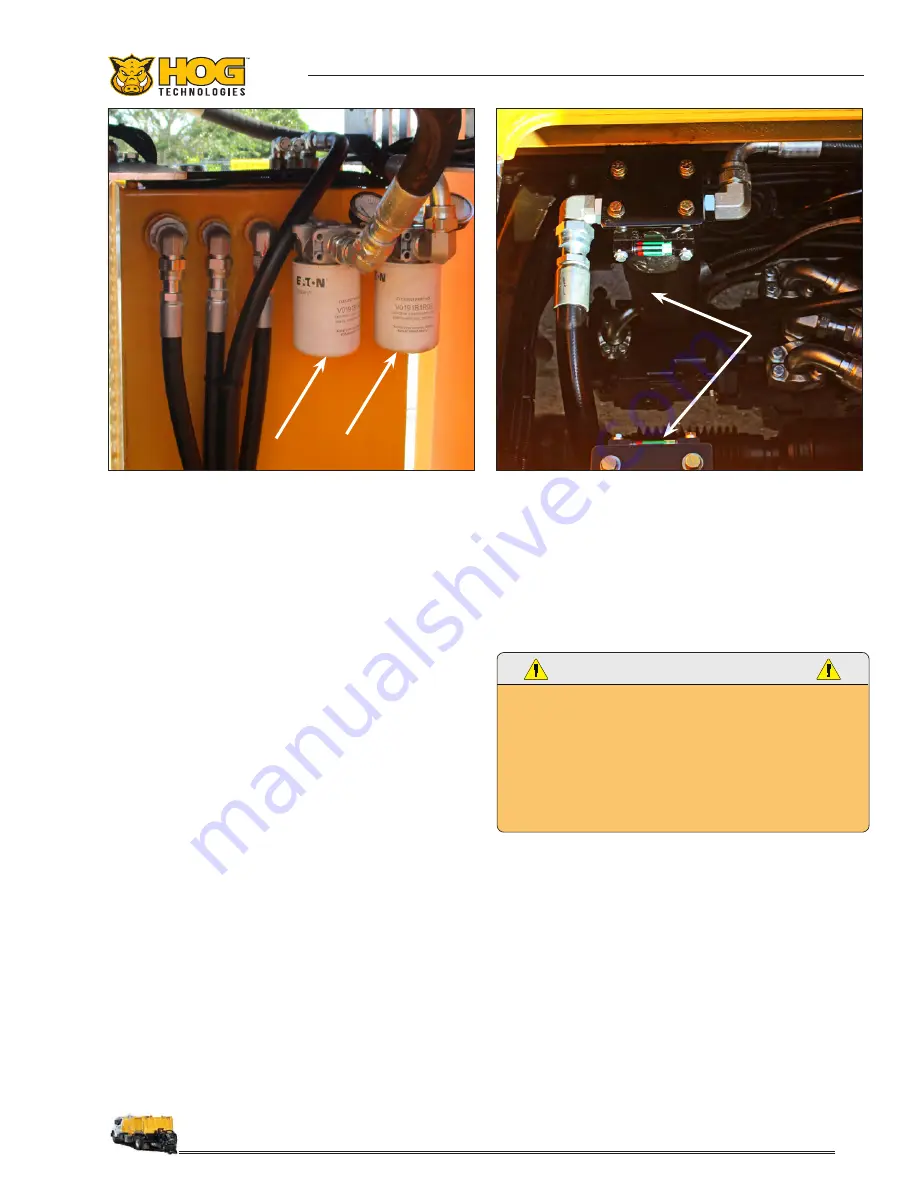
129
Section 4 - lubrication & maintenance
4.11 replacing hydraulic Filters
Before performing any maintenance procedure,
make sure the cutting system is shutdown with
the truck in the service position.
Low Pressure Return Filters
The filters are the spin on type filters located in the
return line near the top of the hydraulic reservoir.
Changing the filters:
1. Make sure the hydraulic system is not pressur-
ized and the fluid is cool. Use a filter wrench
and rotate the filters counterclockwise to re
-
move them.
2.
Lubricate the seal on the new filters with hy
-
draulic fluid.
3.
Install the filters and hand tighten.
4.
Inspect the filters for leaks when the hydraulic
system is activated.
Low Pressure Return Filters & Gauges
On Hydraulic Reservoir
High Pressure Filters
The filters are the spin on type filters located below
the center deck access plate.
WARNING
S O M E H Y D R A U L I C C I R C U I T S A R E E Q U I P P E D W I T H
ACCUMULATORS THAT MAINTAIN PRESSURE IN THE
CIRCUIT AFTER IT IS SHUTDOWN.
ALWAYS MAKE SURE TO FOLLOW PROPER PROCEDURE
TO BLEED PRESSURE FROM THE ACCUMULATORS AND
HYDRAULIC CIRCUITS BEFORE SERVICING THE HIGH
PRESSURE FILTERS.
1. Make sure the hydraulic system is not pres-
surized and the fluid is cool.
2.
Use a filter wrench and rotate the filters coun
-
terclockwise to remove them.
3.
Lubricate the seal on the new filters with hy
-
draulic fluid.
4.
Install the filters and hand tighten.
5.
Inspect the filters for leaks when the hydraulic
system is activated.
High Pressure Filters
Below Deck Access Plate
Summary of Contents for RH7500
Page 1: ...RH7500 Operations Manual ...
Page 2: ......
Page 6: ...6 NOTES ...
Page 10: ...10 NOTES ...
Page 19: ...19 Section 1 Safety Information ...
Page 20: ...20 NOTES ...
Page 108: ...108 NOTES ...
Page 150: ...150 NOTES ...
Page 155: ...155 Appendix 3 Tools Spare Parts ...
Page 156: ...156 Appendix 3 Tools Spare Parts ...
Page 158: ...158 NOTES ...
Page 163: ......